The Importance of Sand Used in Foundry Applications
Sand is an essential material in the foundry industry, pivotal for the manufacturing of metal castings. It serves as the backbone of sand casting processes, where molten metal is poured into sand molds to create various metal products, ranging from automotive components to intricate artistic sculptures. Understanding the significance of sand and its properties can greatly enhance the efficiency and quality of castings.
Types of Sand Used in Foundry
The most commonly used sand in foundries is silica sand, primarily due to its availability and favorable properties. Silica sand consists mainly of silicon dioxide (SiO2) and provides excellent thermal stability, abrasion resistance, and strength. Foundries often treat silica sand with various binding agents and additives to enhance its performance further.
Another popular type of sand in foundries is olivine sand, known for its high melting point and low thermal expansion. Olivine sand is particularly advantageous for casting non-ferrous metals like aluminum because it produces fewer defects and results in smoother surfaces. Other specialty sands, such as zircon sand and chromite sand, are used for specific applications due to their unique characteristics, including high strength and resistance to thermal shock.
Key Properties of Foundry Sand
The effectiveness of sand in foundry applications hinges on several critical properties. Firstly, grain size and distribution significantly impact mold strength and surface finish. Finer sands yield smoother finishes but may lead to poor mold strength, while coarser sands provide greater strength at the cost of surface finish quality.
Secondly, the roundness and sphericity of sand grains affect the flowability and packing density of the mold material. Rounder grains tend to pack more efficiently, leading to better mold integrity and reduced likelihood of defects during casting. Additionally, moisture content plays a crucial role in sand performance, as the right amount of water enhances the sand's binding properties, ensuring that molds maintain their shape until the metal is poured.
sand used in foundry
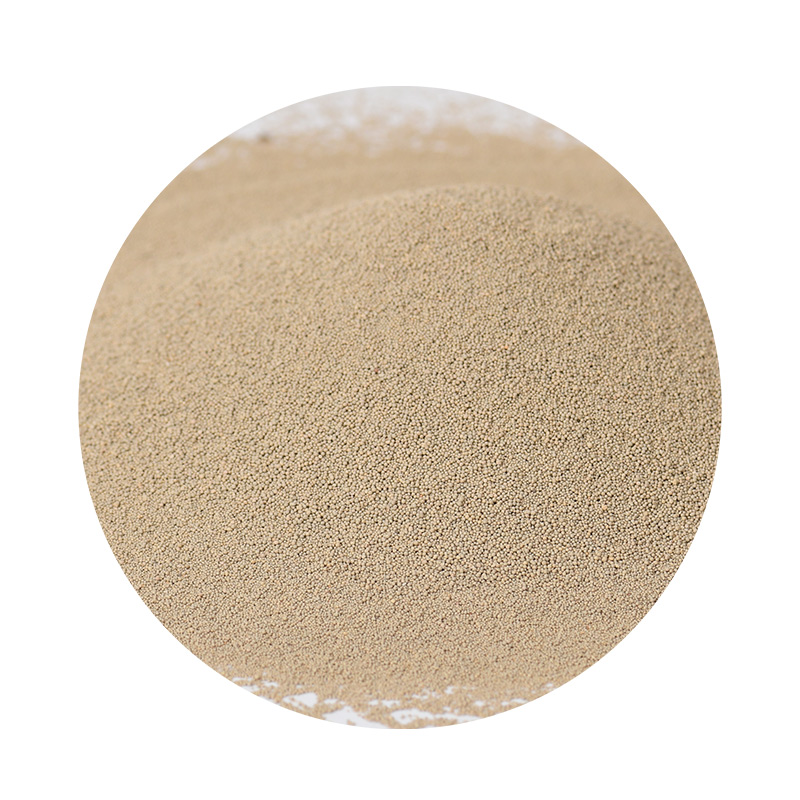
The Role of Sand in the Casting Process
In the sand casting process, the first step involves creating a mold by compacting the sand around a pattern. This pattern is a replica of the component to be cast and is typically made of metal or other rigid materials. Once the mold is formed, the pattern is removed, and the mold cavity is prepared for pouring.
After pouring the molten metal into the sand mold, cooling occurs, allowing the metal to solidify. The sand's properties are crucial at this stage, as they must withstand the heat and pressure of the molten metal without deforming. Once the metal has cooled and hardened, the sand mold is broken apart to reveal the finished casting.
Environmental Considerations
The use of sand in foundries also raises environmental concerns. The extraction and processing of sand can lead to habitat disruption and other ecological impacts. Additionally, waste sand generated after casting can create disposal challenges. Many foundries are now exploring ways to recycle spent foundry sand for use in construction, road building, and landscaping, thereby reducing their environmental footprint and promoting sustainability.
Conclusion
In conclusion, sand is a fundamental element in foundry operations, with its types and properties directly influencing the quality of castings produced. From silica to olivine, the choice of sand impacts mold creation and ultimately the success of the casting process. With growing awareness of environmental issues, the foundry industry is tasked with finding innovative methods to recycle and reuse sand, ensuring its continued relevance in metalworking. As technology evolves, so too will the techniques and materials used, but the foundational importance of sand in foundry applications remains irrefutable.
Post time:Aug . 10, 2024 21:00
Next:Sand Casting Processes for Producing Durable Stainless Steel Parts and Components Efficiently