Sand Casting Processes An Overview
Sand casting, one of the oldest and most versatile manufacturing processes, is widely used in the production of metal parts. Originating from ancient times, this method has evolved into a sophisticated technique suited for various industries, including automotive, aerospace, and art. Sand casting is favored primarily for its ability to create complex shapes and sizes that would be challenging to achieve with other methods.
The Sand Casting Process
The sand casting process typically consists of several key steps pattern creation, mold preparation, pouring, and finishing
.1. Pattern Creation The first step involves creating a pattern of the desired part, usually made from wood, plastic, or metal. The pattern is an exact replica of the final product, including allowances for shrinkage and finishing operations. It can be a single piece or multiple parts that fit together to form a complete mold.
2. Mold Preparation The next step is preparing the mold. The pattern is placed in a mixture of sand, clay, and water, which forms the mold. The sand is compacted around the pattern to create a negative impression. This process can be done using various techniques, including hand packing or mechanical methods. Once the mold is formed, it is removed carefully, ensuring a smooth surface that can accommodate the molten metal.
3. Pouring After the mold is prepared, it is assembled and checked for integrity. The molten metal is then poured into the mold cavity. The temperature, composition, and pouring technique are crucial, as they influence the quality and properties of the final cast.
sand casting processes
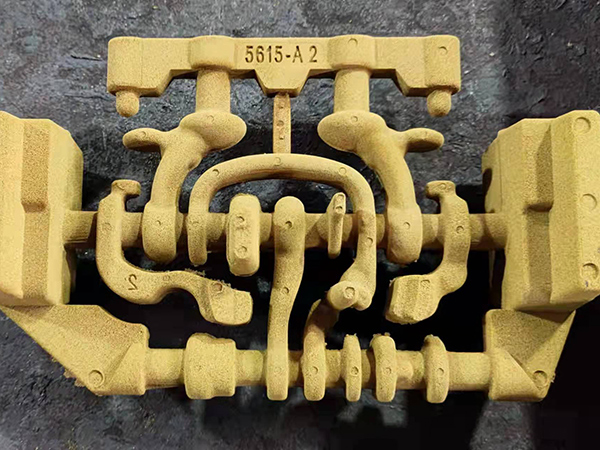
4. Cooling and Finishing After pouring, the metal cools and solidifies, taking on the mold's shape. Once cooled, the mold is broken away, revealing the cast part. Post-casting processes, such as trimming, grinding, and machining, are often necessary to achieve the desired finish and dimensional accuracy.
Advantages of Sand Casting
Sand casting offers several advantages that make it a preferred method in numerous applications. One of the primary benefits is its cost-effectiveness. The materials used for molds—primarily sand—are relatively inexpensive, and the process itself allows for a high degree of flexibility in production.
Furthermore, sand casting can accommodate a wide range of metals, including aluminum, bronze, and iron. It is also capable of producing large and heavy components, making it ideal for industries that require durability and strength.
Another significant advantage is the ability to create complex geometries. The sand casting process enables the production of intricate designs that would be difficult to fabricate using other manufacturing methods. This is particularly beneficial in industries that demand high levels of customization.
Conclusion
In summary, sand casting is a vital manufacturing process with a rich history and a wide array of applications. Its ability to create complex and durable components at a relatively low cost makes it invaluable in modern manufacturing. As industries continue to evolve and demand more innovative solutions, the sand casting process is likely to adapt and remain a cornerstone of metalworking for years to come. Its blend of tradition and technology ensures that sand casting will continue to play a significant role in producing critical components across various sectors.
Post time:Aug . 01, 2024 04:06
Next:Understanding the Costs Involved in Sand Casting Processes and Their Impact on Manufacturing Budget