Lost Foam Casting Materials An Overview
Lost foam casting is an innovative and versatile method used in metal casting that allows for the production of complex shapes with high precision. This technique has gained traction in various industries, including automotive, aerospace, and artistic applications. Central to the success of lost foam casting are the materials used, which play a critical role in determining the overall quality and efficiency of the casting process.
Understanding Lost Foam Casting
In the lost foam casting process, a foam pattern is created, which is then coated with a refractory material to form a shell. The foam pattern is subsequently vaporized when molten metal is poured into the mold, hence the term lost foam. This method eliminates the need for traditional cores and allows for intricate designs to be cast directly, reducing the need for machining and assembly in finished products.
Key Materials Used in Lost Foam Casting
1. Pattern Materials The primary material used for patterns in lost foam casting is typically polystyrene foam. This lightweight material is inexpensive, easy to shape, and provides the required dimensional precision. Some applications may also make use of other foam types, such as polyurethane foam, which can offer different properties such as thermal and chemical resistance.
2. Coating Materials The coatings applied to the foam pattern are critical for molding. These coatings must be able to withstand the high temperatures of the molten metal and prevent reaction with the foam. Commonly used materials include silica sand mixed with a binder, ceramic materials, and various inorganic coatings. The coatings help to create a strong mold shell that can handle the thermal shock when the molten metal is poured in.
3. Binder Materials Binders play an important role in holding the sand grains together in the mold doppelgänger and ensuring structural integrity during the casting process. Various compounds are used as binders, including phenolic resins, sodium silicate, or even water glass. The choice of binder affects both the properties of the mold and the quality of the final casting.
lost foam casting materials
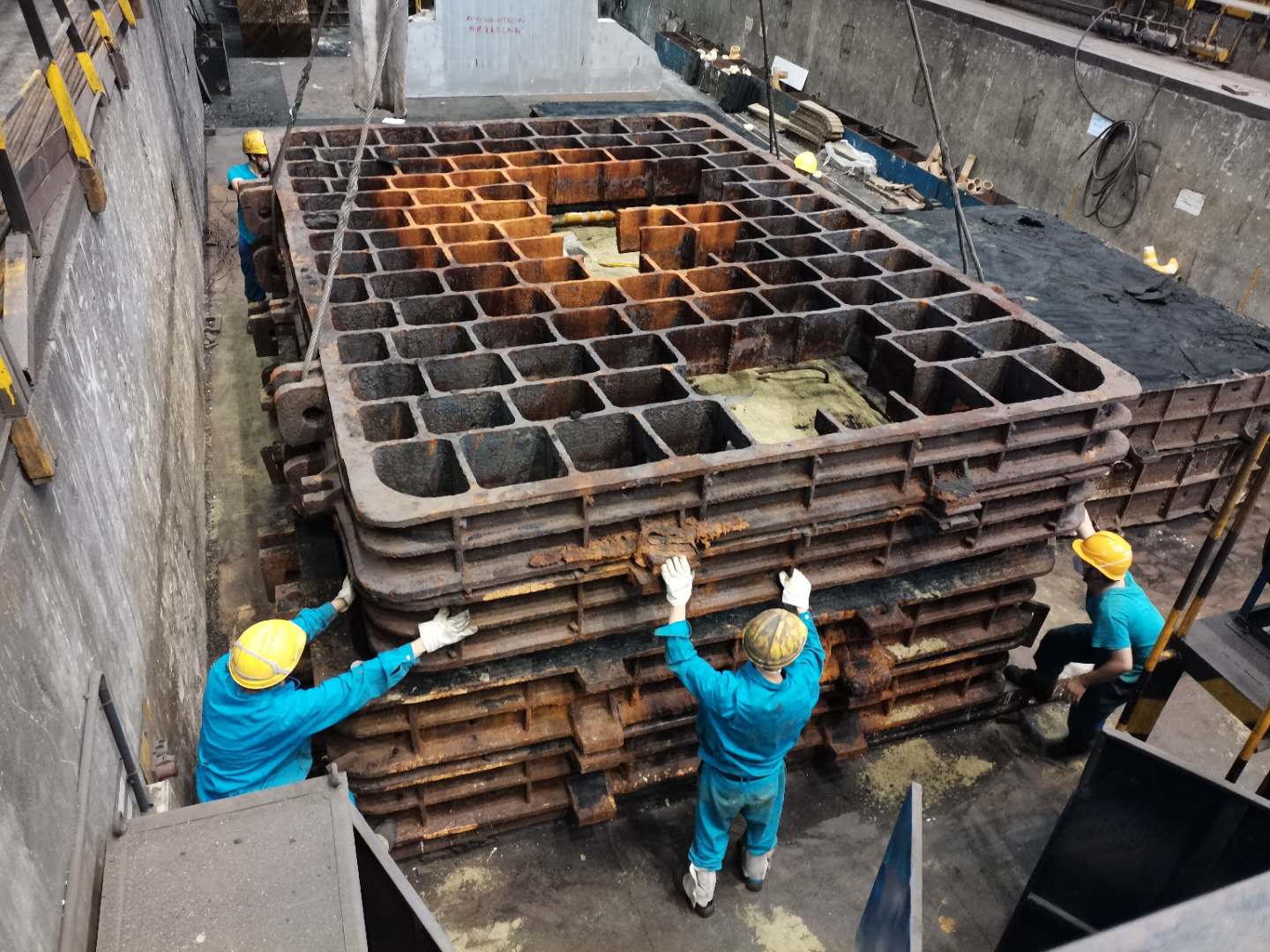
4. Metal Alloys The selection of metal alloys used in lost foam casting also influences the final product. Common choices include aluminum, iron, and various steel alloys, each with unique properties that suit different applications. The metallic feed must be compatible with the mold materials to avoid defects and ensure a smooth casting process.
5. Furnaces and Heating Equipment The choice of furnace for melting the metal is crucial as it must provide a consistent heating source and the ability to reach the desired temperatures efficiently. Induction furnaces are commonly used due to their ability to heat metals uniformly and minimize oxidation.
Advantages of Using Lost Foam Casting Materials
The materials used in lost foam casting confer several advantages over traditional casting methods. One of the most significant benefits is the ability to create complex geometries without the need for additional tooling, which reduces production costs and time. Furthermore, the process leads to less waste material since there is no need for cores or multiple runs.
Additionally, the high dimensional accuracy and surface finish achieved through this method often eliminate the need for extensive post-processing, contributing to reduced lead times and improved efficiency.
Conclusion
Lost foam casting presents an excellent option for manufacturers seeking to produce high-quality components with intricate designs. The selection of appropriate materials for patterns, coatings, binders, and metal alloys is fundamental to the success of this casting method. As industries continue to seek advanced manufacturing techniques that enhance productivity and minimize waste, lost foam casting stands out as a viable and continuing choice for innovative material processing.
Post time:Aug . 07, 2024 14:30
Next:Exploring the Benefits and Techniques of Hard Sand Casting in Modern Manufacturing Processes