Resin Bonded Sand Casting A Modern Approach to Metal Casting
Resin bonded sand casting is an innovative method of producing intricate metal parts that are widely used in various industries, such as automotive, aerospace, and consumer goods. This technique combines traditional sand casting with modern resin technology, resulting in high-quality castings that offer improved accuracy, surface finish, and dimensional stability.
What is Resin Bonded Sand Casting?
At its core, resin bonded sand casting involves mixing sand with a phenolic resin binder, which is activated by heat. This mixture is then shaped into a mold using patterns that represent the final metal product. Once the mold is formed and cured, molten metal is poured into the cavity, solidifying to create the desired component. The key advantage of using resin as a binder is its ability to create a strong and rigid mold that can withstand the high temperatures involved in metal casting.
Advantages of Resin Bonded Sand Casting
1. High Precision and Complexity One of the most significant benefits of resin bonded sand casting is its ability to produce complex shapes with high precision. The resin binder allows for finer detail in the mold, enabling manufacturers to create intricate designs that would be difficult or impossible to achieve with traditional sand casting methods. This precision is crucial in industries where part performance directly affects safety and functionality.
2. Superior Surface Finish Parts produced through resin bonded sand casting often exhibit a better surface finish compared to those made using traditional methods. The fine grain structure of the sand, combined with the properties of the resin, helps reduce surface imperfections, which can lead to lower machining costs and enhanced aesthetic appeal. This advantage is particularly important in industries that prioritize both function and aesthetics.
resin bonded sand casting
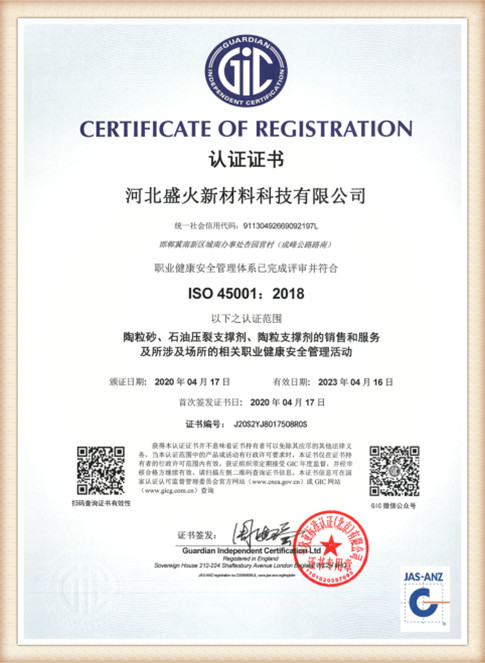
3. Enhanced Dimensional Stability The dimensional stability of resin bonded molds is considerably higher than that of traditional sand molds. Unlike conventional methods that may experience sand shifting or expansion during the casting process, resin bonded sand maintains its shape and integrity. This reduces the risk of defects such as warping and misalignment, leading to more consistent part production.
4. Faster Production Times The speed at which molds can be created using resin bonded sand casting is another noteworthy advantage. The curing process of the resin is relatively quick, enabling faster mold turnaround times. This efficiency is essential in today's fast-paced manufacturing environment, where time-to-market is a critical factor for success.
5. Environmentally Friendly Options Recent advancements in resin technology have led to the development of more environmentally friendly binders, reducing the ecological footprint of the casting process. Manufacturers can now produce high-quality castings with fewer harmful emissions, making it a more sustainable choice for producing metal components.
Applications of Resin Bonded Sand Casting
The versatility of resin bonded sand casting allows it to be used in a wide range of applications. It is commonly employed in the production of engine blocks, transmission housings, and other automotive components where precision and durability are paramount. The aerospace industry also benefits from this method, producing critical parts that require stringent quality and performance standards. Additionally, consumer goods such as decorative hardware and fittings often utilize resin bonded sand casting for their intricate designs and superior finishes.
Conclusion
In summary, resin bonded sand casting represents a significant advancement in metal casting technology. Its ability to produce high-precision, complex parts with excellent surface finishes and dimensional stability makes it an attractive option for various industries. As technology continues to evolve, the adoption of resin bonded sand casting is likely to increase, paving the way for more innovative and efficient manufacturing solutions.
Post time:Aug . 18, 2024 08:56
Next:Tips for Sanding and Smoothing Your 3D Printed Models Effectively