The Role of Furan Resin in Sand Casting
Sand casting is one of the oldest and most versatile foundry processes used for producing metal parts. This method involves pouring molten metal into molds made of sand, which can be shaped to create intricate designs. Among the various materials used in sand casting, furan resin has gained significant attention due to its beneficial properties and advantages over traditional binding agents.
Furan resin is a thermosetting polymer derived from furan, a compound that is usually sourced from natural ingredients like sugarcane, lignin, and other biomass. Its unique chemical structure allows it to provide superior strength and durability when used as a binder in sand molds. The use of furan resin in sand casting is often favored for several reasons.
1. Enhanced Strength and Durability
Furan resin provides excellent strength characteristics that are essential in the sand casting process. When mixed with sand, the resin creates a mold that can withstand the thermal and mechanical stresses of molten metal. The high heat resistance of furan resins means that they maintain integrity even at elevated temperatures, which is crucial during the casting of metals like aluminum, iron, and steel.
2. Low Moisture Content
One of the problems often encountered in traditional sand casting is the moisture content in the sand, which can affect the quality of the castings. Furan resin is mixed with dry sand, significantly reducing the amount of moisture present in the mold. This low moisture content helps prevent defects such as sand adhesion or mold collapse, resulting in higher quality castings.
furan resin sand casting
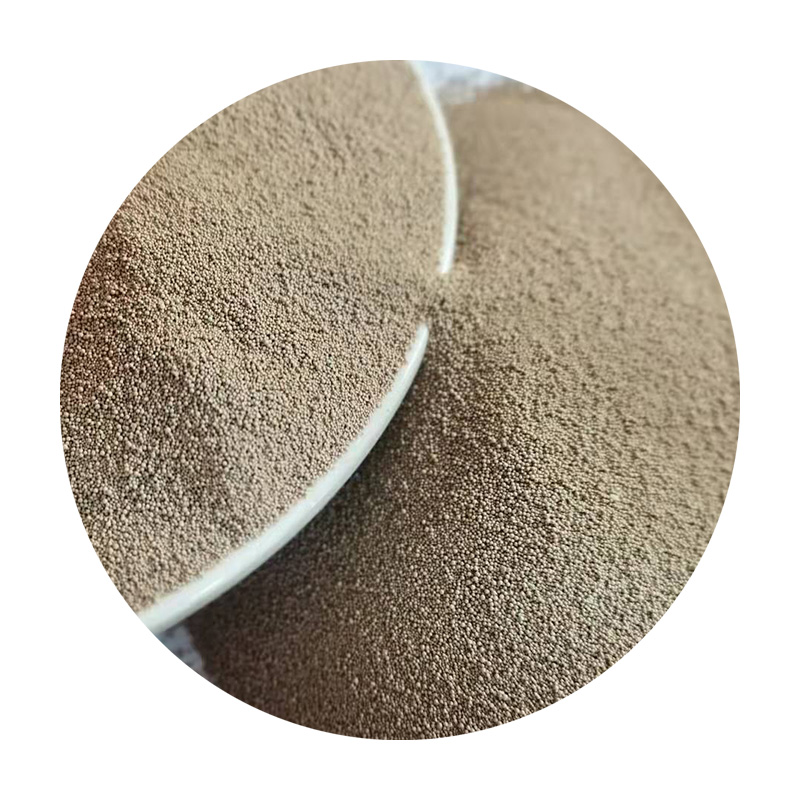
The surface finish of cast parts is an important factor in various applications, especially in industries like automotive or aerospace where precision is crucial. Furan resin leads to smoother mold surfaces, which in turn produce castings with improved surface quality. This reduces the need for post-casting machining processes, saving both time and cost.
4. Eco-Friendly Characteristics
With the increasing demand for sustainable practices in manufacturing, furan resin stands out as a more environmentally friendly alternative to conventional phenolic resins. As it can be derived from renewable resources, the use of furan resin aligns with modern sustainability goals. Additionally, furan resins have lower volatile organic compounds (VOCs), making them safer for workers and minimizing harmful emissions during the casting process.
5. Versatility in Applications
Furan resin is suitable for a wide range of applications, including the production of complex designs—something that can be challenging with other binding agents. Its ability to maintain shape and detail makes it an ideal choice for intricate molds. Industries ranging from automotive to general manufacturing can benefit from its properties, making furan resin an appealing option for many foundries.
Conclusion
In conclusion, the integration of furan resin into sand casting represents a significant advancement in foundry technology. Its enhanced strength, low moisture content, improved surface finish, eco-friendly characteristics, and versatility make it a preferred choice for many manufacturers. As industries continue to evolve and seek better methods for metal casting, furan resin is poised to play a crucial role in driving the future of sand casting techniques. By embracing innovative materials like furan resin, foundries can not only improve the efficiency of their processes but also contribute to sustainable manufacturing practices.
Post time:Jul . 24, 2024 01:08
Next:Exploring the Unique Offerings and Values of Golden Sands Corporation in Today's Market Environment