Understanding Resin Sand Applications and Benefits
Resin sand, a critical component in modern foundry processes, has revolutionized the way casting is conducted in various industries. Unlike traditional sand, resin sand is a mixture of sand, resin, and hardening agents, which creates a more durable and efficient medium for producing high-quality castings. This article will delve into the composition, advantages, and varied applications of resin sand, highlighting why it has become increasingly popular in casting processes.
Composition of Resin Sand
At its core, resin sand consists of high-quality silica sand coated with a thermosetting resin, typically phenolic or furan-based. The addition of hardeners allows the sand to set quickly and maintain its shape during the casting process. This unique combination offers superior properties such as excellent dimensional accuracy, a smooth surface finish, and high strength at various temperatures. The use of resin enables the sand to bond effectively without the need for water, contrasting sharply with traditional green sand molds.
Advantages of Resin Sand
One of the most significant advantages of resin sand is its ability to produce intricate designs and complex geometries. The high tensile strength of resin-coated sand allows for thinner walls and more detailed patterns, reducing the need for post-processing. Additionally, the absence of moisture in resin sand minimizes defects such as gas holes and steam-related issues, which are common with traditional methods.
Another key benefit is the improved surface finish that resin sand provides. Castings produced with resin sand typically exhibit a much smoother surface, resulting in less machining and finishing required, ultimately saving both time and costs in production. Moreover, the thermal stability of resin sand enables it to withstand higher temperatures, making it suitable for high-performance applications in industries such as automotive, aerospace, and oil and gas.
resin sand
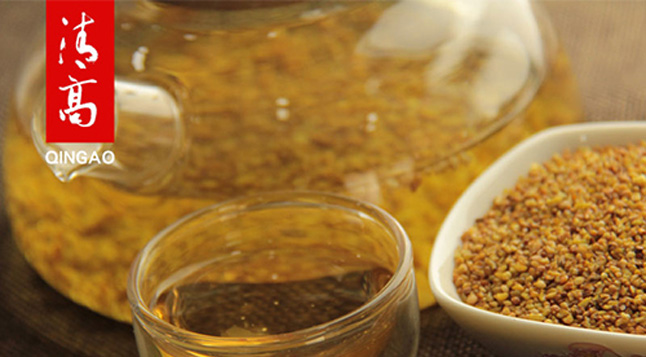
Applications of Resin Sand
Resin sand finds its application across diverse sectors. In the automotive industry, it is commonly used for producing engine blocks, transmission cases, and custom parts where precision and durability are paramount. The aerospace sector also utilizes resin sand for creating lightweight yet strong components, particularly in turbine housings and other critical aircraft parts.
In the oil and gas industry, resin sand is employed to manufacture valves and fittings that can withstand extreme conditions, ensuring resilience and reliability in harsh operational environments. Furthermore, the growth of additive manufacturing techniques has opened up new avenues for resin sand, facilitating the creation of molds for complex geometries that were previously challenging to achieve.
Environmental Considerations
With the increasing focus on sustainability, resin sand technology has also evolved to address environmental concerns. Innovative practices, such as using organic binders and recycling spent sand, have emerged in response to the industry's need for greener alternatives. Such initiatives not only reduce waste but also minimize the overall carbon footprint of the casting process.
Conclusion
In conclusion, resin sand represents a significant advancement in casting technology, offering a multitude of benefits that enhance the efficiency and quality of castings. Its superior strength, intricate casting capabilities, and reduced need for post-processing make it an ideal choice for industries that demand precision and durability. As technology continues to evolve and the push for sustainability grows, resin sand will likely play an even more pivotal role in the future of manufacturing and engineering processes. By embracing this innovative material, industries can not only meet their production needs but also contribute to a more sustainable future.
Post time:Aug . 05, 2024 19:50
Next:Comprehensive Sand Casting Solutions for Precision Parts Manufacturing and Customized Design Services