The Art and Science of Sand Casting
Sand casting, one of the oldest and most versatile metal casting processes, has remained an essential manufacturing technique in various industries, from automotive to aerospace and beyond. This approach, which utilizes sand as a primary molding material, offers several advantages, making it a preferred choice for many metal components.
The Fundamentals of Sand Casting
At its core, sand casting involves creating a mold from a mixture of sand, clay, and water. The process begins with the production of a pattern, typically made of metal, plastic, or wood, that represents the object to be cast. This pattern is pressed into a sand mixture, forming two halves of a mold. Once the mold is prepared, the pattern is removed, leaving a cavity that replicates the shape of the intended object.
Molten metal is then poured into the cavity, where it fills the space left by the pattern and eventually solidifies. After cooling, the mold is broken away to reveal the finished casting. This process allows for intricate designs, varying sizes, and the production of complex geometries, making it suitable for a wide range of applications.
Benefits of Sand Casting
One of the primary advantages of sand casting is its cost-effectiveness. The raw materials, such as sand and clay, are relatively inexpensive and widely available. Additionally, the molds have a high thermal conductivity, which allows for efficient heat dissipation, leading to improved mechanical properties in the final castings.
Sand casting also accommodates a variety of metals, including aluminum, iron, copper, and bronze, providing manufacturers the flexibility to select materials based on the application’s requirements. Moreover, sand molds can be reused multiple times, especially if the sand is treated correctly, thus boosting productivity and reducing production waste.
sand castings
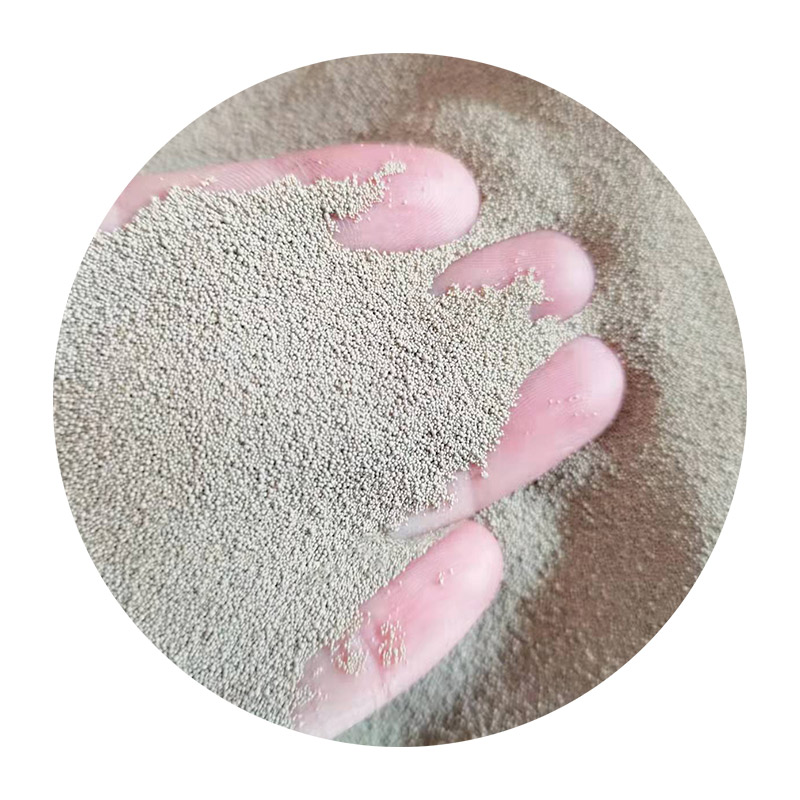
The Versatility of Sand Casting
With its adaptability, sand casting has found applications across numerous industries. In the automotive sector, for instance, it is commonly utilized to produce critical components like engine blocks and transmission cases, where strength and durability are paramount. In the aerospace industry, lightweight yet robust components are often created through sand casting, playing a vital role in the performance and efficiency of aircraft.
Moreover, artists and sculptors have embraced sand casting as a medium for creating intricate sculptures and decorative pieces. The ability to cast in a variety of metals allows for diverse artistic expressions, further showcasing the versatility of this method.
Challenges and Innovations
Despite its many advantages, sand casting is not without its challenges. The process can result in surface imperfections, such as sand inclusions, which may require additional finishing work to achieve the desired quality. Furthermore, the dimensional accuracy of sand castings may not match that of more advanced casting methods. However, ongoing innovations, such as the introduction of 3D printing technologies for creating molds, are addressing these limitations, enhancing precision and reducing lead times.
Conclusion
In summary, sand casting is a time-tested manufacturing process that combines art and science to create a wide range of metal parts and components. Its affordability, versatility, and ability to handle various materials make it a staple in modern manufacturing. As technology continues to evolve, sand casting will undoubtedly remain relevant, adapting to meet the demands of contemporary industry while preserving the heritage of this ancient craft. Whether used in heavy machinery, intricate artworks, or critical aerospace components, sand casting's enduring legacy is a testament to its significance in the world of manufacturing.
Post time:Aug . 12, 2024 10:12
Next:Techniques for Achieving a Smooth Finish in 3D Printed Objects Through Sanding Methods