Steel Sand Casting A Comprehensive Overview
Steel sand casting is a widely utilized manufacturing process that is essential in converting molten steel into intricate shapes and components. This method is particularly favored due to its versatility and efficiency in producing complex geometries, making it integral to various industries such as automotive, aerospace, construction, and machinery.
At its core, sand casting involves the creation of a sand mold, which is used to shape the molten steel as it cools and solidifies. The first step in this process is pattern making, where a replica of the desired object is created from materials like wood, metal, or plastic. The pattern is then used to form a mold in a mixture of sand and a binding agent, which can withstand the high temperatures of molten steel.
One of the significant advantages of steel sand casting is its ability to produce large and heavy components
. Steel, known for its strength and durability, is often used in applications that require high tensile strength and impact resistance. The sand casting process can accommodate components weighing several tons, making it ideal for producing parts such as engine blocks, frames, and heavy-duty machinery components.Once the mold is prepared, it is preheated to reduce thermal shock when the molten steel is poured. The molten steel is typically poured at temperatures around 1400 to 1600 degrees Celsius, allowing it to flow into the intricate cavities of the mold. The sand mold must be designed to facilitate the removal of trapped air, ensuring a proper fill. Techniques such as using vents or ramming the sand can help achieve this.
steel sand casting
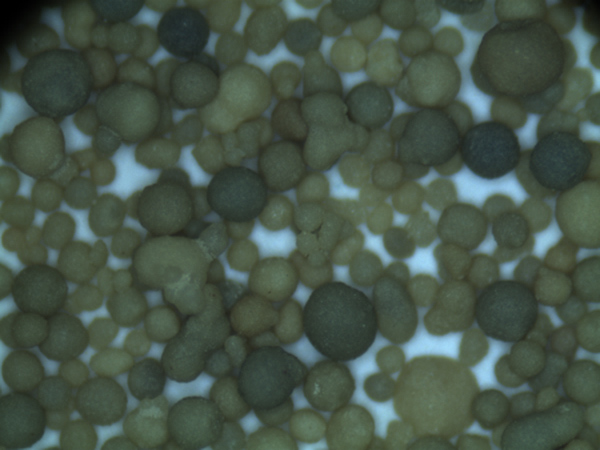
As the molten steel cools, it undergoes a transformation, solidifying into the shape of the mold. Depending on the complexity and thickness of the casting, cooling times can vary. After sufficient time has passed, the mold is broken away, revealing the cast steel component.
Post-casting processes are critical for achieving the desired surface finish and dimensional accuracy. This often involves cleaning the castings to remove sand residue, followed by machining to ensure precise dimensions. Heat treatment may also be applied to enhance the mechanical properties of the steel, tailoring the final product for its intended use.
Despite its many advantages, steel sand casting also presents certain challenges. One common issue is the potential for defects such as porosity, which can weaken the final product. Proper mold design, careful control of the pouring process, and post-casting inspection can mitigate these risks. Another challenge lies in the environmental impact associated with sand casting, particularly concerning the disposal of used sand and the emissions generated during the process.
To address these environmental concerns, innovations in sand casting techniques are underway. Reusable sand systems and environmentally friendly binders are being developed to minimize waste and improve sustainability. Moreover, advancements in additive manufacturing are being explored to enhance pattern-making and mold creation processes, further increasing efficiency.
In conclusion, steel sand casting is a vital manufacturing technique that plays a significant role in producing high-strength steel components across various industries. Its ability to create complex shapes, combined with the durability of steel, makes it an invaluable process. However, ongoing efforts to enhance sustainability and address potential defects are essential to ensure that steel sand casting remains a preferred method in the competitive landscape of modern manufacturing. As technology continues to evolve, the future of steel sand casting looks promising, offering new opportunities for innovation and efficiency.
Post time:Aug . 06, 2024 06:01
Next:Exploring the Benefits and Applications of the Lost Foam Casting Technique in Modern Manufacturing