The Art and Science of Sand Casting in Metalworking
Sand casting, a pivotal method in metalworking, has long been a preferred technique for producing a variety of metal parts and components. The process, which involves creating a mold from sand, offers a unique combination of artistic craftsmanship and scientific reproducibility, making it applicable across various industries, from automotive to aerospace. This article delves into the principles of sand casting, its advantages, and the future of this age-old practice.
Understanding the Sand Casting Process
At its core, sand casting involves several fundamental steps pattern making, mold making, melting, pouring, and finishing. The initial step is creating a pattern, usually made from metal, plastic, or wood, which mirrors the desired final product. This pattern is then used to create a mold by packing sand around it. The sand must be mixed with a binding agent—typically a clay-like substance—to hold its shape during the casting process.
Once the mold is prepared, the next step involves melting the metal. Various metals can be used in sand casting, including aluminum, cast iron, and bronze. The choice of metal depends on the desired properties of the final product. After reaching the appropriate temperature, the molten metal is carefully poured into the mold cavity. Once the metal cools and solidifies, the mold is broken away to reveal the cast part, which often requires additional finishing processes such as machining or surface treatment to achieve the desired specifications.
Advantages of Sand Casting
One of the primary advantages of sand casting is its versatility. This process can accommodate a wide range of part sizes, from small components to large industrial pieces, with complex shapes that would be difficult to achieve using other manufacturing methods. Additionally, the materials used—primarily sand—are relatively inexpensive and widely available, leading to cost-effective production.
Another significant benefit is the ability to produce low quantities of customized parts without the need for expensive tooling. This flexibility makes sand casting an ideal choice for prototyping and small production runs, allowing engineers and designers to iterate quickly during the development phase.
sand cast metal
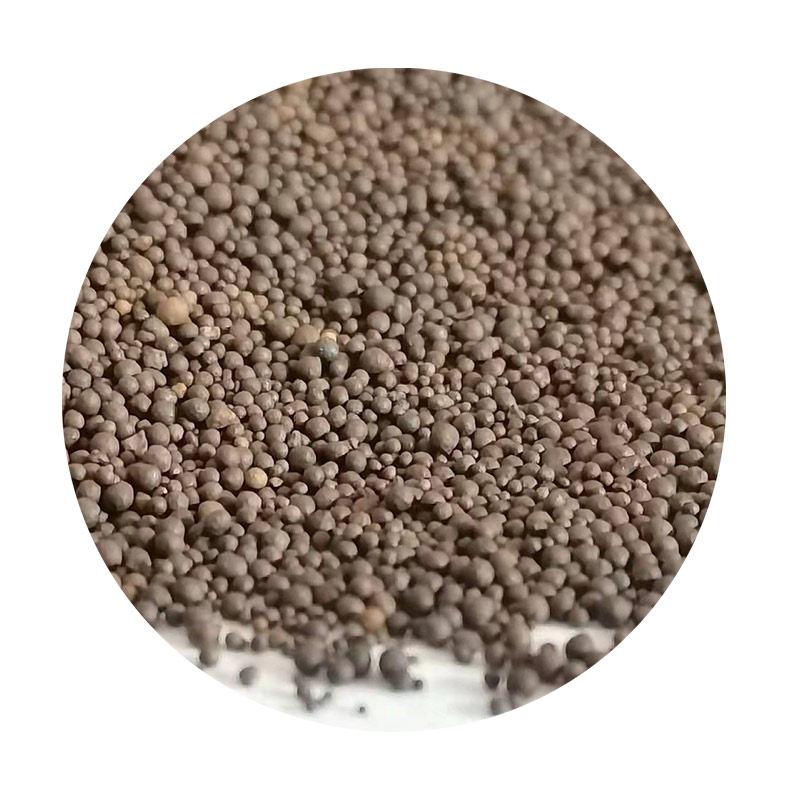
Moreover, the sand casting process is environmentally friendly compared to other casting methods. The materials used can be recycled, and advancements in technology have led to more sustainable practices within the industry, such as the use of reclaimed sand and eco-friendly binders.
Challenges and Innovations
Despite its many advantages, sand casting is not without challenges. The process can produce defects such as porosity, inclusions, or dimensional discrepancies, necessitating careful quality control. Additionally, the surface finish of sand-cast components may not be as smooth as those produced through other methods, which can require additional finishing processes.
Yet, innovations in sand casting technology continue to emerge. Advances such as 3D printing are being integrated into the mold-making process, enhancing precision and reducing production time. Automation and robotics are also being incorporated into sand casting facilities, increasing efficiency and reducing labor costs.
The Future of Sand Casting
Looking ahead, the future of sand casting appears promising. As industries increasingly seek sustainable production processes, the eco-friendly nature of sand casting will likely propel its continued relevance. Additionally, the ability to customize parts quickly and cost-effectively aligns well with the current trend towards personalized manufacturing in sectors such as automotive and consumer goods.
In conclusion, sand casting remains a fundamental method in metalworking that marries art and science. Its versatility, cost-effectiveness, and ongoing innovations ensure that it will continue to play a crucial role in manufacturing for years to come. As technology evolves, it will be fascinating to see how sand casting adapts and integrates new techniques to meet the demands of modern industry.
Post time:Aug . 19, 2024 19:13
Next:Exploring the Benefits and Techniques of Resin Sand Casting in Metal Fabrication