Metal Sand Casting A Comprehensive Overview
Metal sand casting is a versatile and widely-used manufacturing process that produces intricate and durable metal components. It involves the use of sand as a primary mold material, which allows for the creation of complex shapes and designs. This method has a rich history and continues to evolve with advancements in technology and materials.
The Sand Casting Process
The sand casting process begins with the creation of a mold. A pattern, typically made of metal, plastic, or wood, is produced to represent the final part. This pattern is then placed into a mixture of sand and binding agents, forming the mold. The most common type of sand used is silica sand, known for its excellent thermal properties and ability to retain shape during the pouring of molten metal.
After the mold is prepared, the next step is to melt the metal that will be cast. Various metals can be used in sand casting, including aluminum, steel, iron, and brass. The choice of metal depends on the required properties of the final product. Once the metal reaches its liquid form, it is poured into the mold cavity. After sufficient cooling time, the sand mold is broken away to reveal the finished casting.
Advantages of Metal Sand Casting
One of the most significant advantages of sand casting is its ability to produce a wide range of sizes and shapes, from small intricate parts to large industrial components. This flexibility makes it an ideal choice for various applications across different industries, including automotive, aerospace, and construction. Furthermore, sand casting can accommodate different types of metals, which opens up opportunities for innovative designs and performance characteristics.
metal sand casting
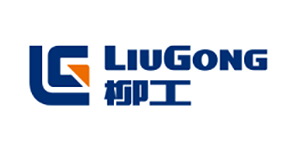
Another benefit is the cost-effectiveness of the process. While the initial setup for pattern making may be expensive, the low cost of sand and the ability to reuse sand for multiple castings help maintain overall costs down. The sand casting process is also highly scalable, enabling manufacturers to produce both small and large production runs without significant changes to equipment or processes.
Environmental Considerations
In recent years, there has been an increased focus on sustainability within the manufacturing sector, and metal sand casting is no exception. The use of environmentally-friendly binders and recycled materials is becoming more common. Manufacturers are also looking at ways to reduce waste and improve energy efficiency in the melting process, thereby minimizing the environmental impact of sand casting operations.
Challenges and Innovations
Despite its many advantages, metal sand casting is not without challenges. The process can produce defects such as sand inclusions, gas porosity, and dimensional inaccuracies. To mitigate these issues, manufacturers invest in precision pattern design, advanced mold materials, and post-casting inspection techniques. As technology evolves, innovations such as 3D printing for mold creation are starting to revolutionize the industry. This allows for more complex geometries and reduced lead times, further enhancing the capabilities of sand casting.
Conclusion
In conclusion, metal sand casting remains a vital manufacturing process that combines tradition with modern advancements. Its flexibility, cost-effectiveness, and ability to produce complex shapes make it an enduring choice for many industries. As manufacturers continue to adapt and innovate, the future of metal sand casting looks promising, with a focus on sustainability and quality improving the landscape of metal component production. As technology progresses, it will be exciting to see how this age-old technique evolves to meet the demands of contemporary manufacturing.
Post time:Jul . 31, 2024 06:15
Next:Top Sand Casting Companies for Innovative Metal Fabrication Solutions and High-Quality Manufacturing Processes