The Art and Science of Iron Sand Casting
Iron sand casting is a fascinating process that blends traditional craftsmanship with modern engineering techniques. This method of manufacturing has been utilized for centuries, evolving over time to meet the demands of various industries. Iron sand, which is primarily composed of iron oxide, serves as a key resource in this casting process, providing both material properties and advantages that make it a preferred choice in many applications.
The Basics of Iron Sand Casting
Iron sand casting involves creating a mold from a mixture of sand and a binding agent, typically clay or resin, into which molten iron is poured. The process begins with the preparation of the mold, which is shaped to form a negative impression of the object to be cast. The use of iron sand is crucial because it has high thermal conductivity, enabling it to withstand the intense heat of molten iron without deforming.
Once the mold is prepared, it is filled with molten iron, which is heated to a temperature of approximately 1,500 degrees Celsius. The iron fills the cavity of the mold, solidifying as it cools. After a cooling period, the mold is removed, revealing the finished casting. This process can be repeated to create multiple copies of the same item, making it an efficient solution for mass production.
Advantages of Iron Sand Casting
One significant advantage of iron sand casting is its cost-effectiveness. The abundance of iron sand makes it a readily available material, lowering raw material costs. Furthermore, the durability of iron sand molds allows for repeated use, which enhances the economic efficiency of the manufacturing process.
Additionally, iron sand casting offers greater design flexibility compared to other casting methods. Manufacturers can produce intricate designs and complex shapes, meeting the specific requirements of various industrial applications. This versatility is particularly beneficial in the automotive and aerospace industries, where custom parts are often needed.
iron sand casting
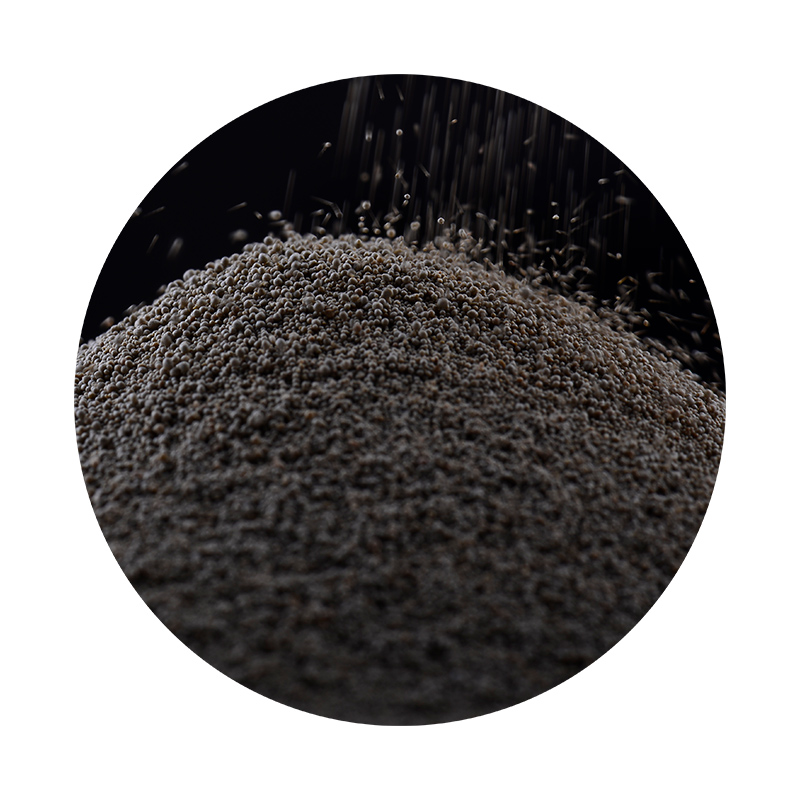
The process is also environmentally advantageous. The use of natural sand minimizes the need for synthetic materials, and advancements in eco-friendly binding agents have further reduced the environmental footprint of the casting process. Recycled foundry sand can also be utilized, promoting sustainability by minimizing waste.
Applications of Iron Sand Casting
Iron sand casting is employed in a variety of industries. In the automotive sector, it is used for producing engine blocks, transmission housings, and other components that require robustness and precision. In construction, cast iron products like manhole covers and pipes benefit from the strength and durability that iron sand casting offers.
Moreover, artistic applications of iron sand casting cannot be overlooked. Sculptors and artists have long utilized this method to create intricate metal sculptures and decorative pieces, benefiting from the unique finish and detail that iron sand can provide.
The Future of Iron Sand Casting
As industries continue to innovate, the future of iron sand casting looks promising. Research into advanced materials and technologies, such as 3D printing of molds and automation of the casting process, are likely to enhance efficiencies and reduce costs further. Additionally, growing environmental awareness will encourage ongoing advancements towards sustainable practices in the industry.
In conclusion, iron sand casting remains a vital process in modern manufacturing. Its combination of economic viability, design flexibility, and environmental sustainability positions it as a significant player in the future of industrial production. As technology continues to advance and new methods are developed, iron sand casting will undoubtedly adapt, maintaining its relevance in an ever-evolving landscape.
Post time:Aug . 20, 2024 07:41
Next:Créamha dhréacht te, créamh fóirne glóire, brící ghréine.