Hard Sand Casting An In-Depth Look at a Traditional Manufacturing Process
Hard sand casting, also known as green sand casting, is a traditional and widely used metal casting process that leverages the properties of sand to create intricate metal parts. This method has been utilized for centuries and remains popular today due to its versatility, cost-effectiveness, and ability to produce high-quality castings. In this article, we will explore the fundamentals of hard sand casting, its advantages, applications, and the challenges associated with the process.
The Fundamentals of Hard Sand Casting
At its core, hard sand casting involves the creation of a mold from a mixture of sand, clay, and water. The term hard in hard sand casting refers to the strong bonding characteristics provided by the clay when combined with sand. This mixture is shaped into a mold through a two-part process
1. Pattern Creation First, a pattern of the desired part is created, typically out of metal or plastic. The pattern is then pressed into the sand mixture to form the mold cavity.
2. Mold Assembly After the mold is created, it is assembled into two halves and reinforced to withstand the pouring pressure of molten metal.
Once the mold is prepared, molten metal—such as aluminum, iron, or bronze—is poured into the cavity
. After cooling, the mold is broken apart to reveal the solidified casting.Advantages of Hard Sand Casting
1. Cost-Effectiveness One of the major advantages of hard sand casting is its cost-effectiveness. The materials used for the sand mixture are relatively inexpensive and readily available. Additionally, the process requires minimal investment in machinery, making it accessible for small and large manufacturers alike.
hard sand casting
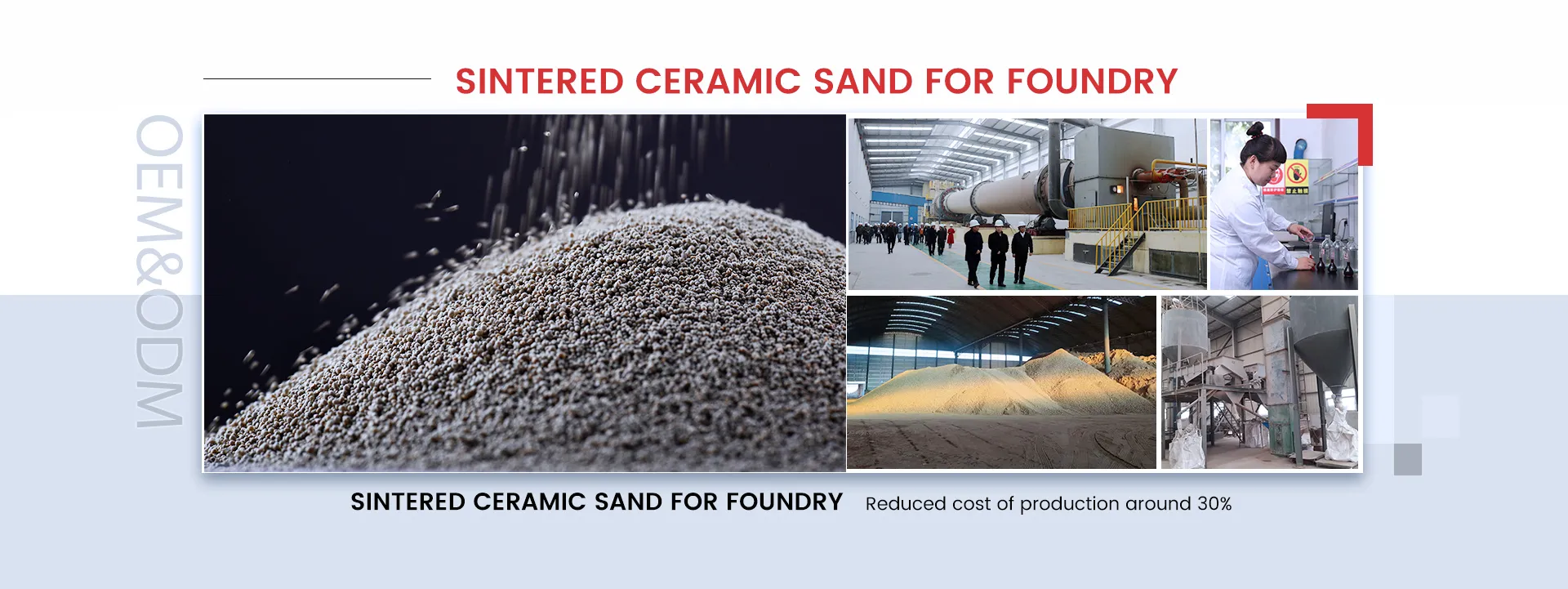
2. Versatility Hard sand casting can accommodate a wide variety of metals and alloys, which allows for the production of diverse components tailored to specific applications. This versatility extends to the production of both small and large castings, from intricate parts for machinery to heavy components for structural applications.
3. High Tolerance and Finish Modern advancements in sand casting technology have improved the surface finish and dimensional tolerances. This enables manufacturers to produce parts that meet stringent specifications and reduce the need for secondary machining operations.
4. Recyclability Another significant advantage is the ability to recycle the sand. After a casting is produced, the sand can be cleaned and reused for subsequent mold-making processes, minimizing waste and promoting sustainability.
Applications of Hard Sand Casting
Hard sand casting is utilized across various industries, including automotive, aerospace, construction, and consumer products. It is particularly effective for producing engine blocks, transmission housings, and other heavy machinery components. Moreover, artistic applications, such as sculptures and decorative items, often use sand casting to create unique and detailed works of art.
Challenges in the Hard Sand Casting Process
Despite its many advantages, hard sand casting does present some challenges. The process requires skilled labor to ensure that the molds are created accurately and that pouring is done correctly to avoid defects, such as porosity and surface imperfections. Moreover, the sand mixture's quality must be carefully controlled, as variations can lead to inconsistent castings.
In conclusion, hard sand casting remains a cornerstone of the metal manufacturing industry, offering a blend of cost-effectiveness, versatility, and quality. While challenges exist, the continuous improvement in materials and techniques means that hard sand casting will likely thrive, adapting to new technologies and demands in the ever-evolving landscape of production. Whether for industrial applications or artistic endeavors, hard sand casting's unique properties and capabilities make it an enduring choice in the world of metal fabrication.
Post time:Jul . 20, 2024 01:04
Next:Effective Techniques for Smoothing and Finishing Ceramic Surfaces with Sanding Methods