Exploring Dry Sand Casting A Sustainable Approach to Metal Casting
Dry sand casting is an innovative metal casting process that has gained attention in various manufacturing sectors due to its efficiency and sustainability. Unlike the traditional sand casting methods that use wet sand mixtures, dry sand casting employs a sand mixture that is bound with a resin or hardener, allowing for improved dimensional accuracy and finer surface finishes. This article explores the process of dry sand casting, its advantages, applications, and its contribution to sustainable manufacturing.
The Process of Dry Sand Casting
The dry sand casting process begins with the preparation of the sand mixture. The sand is typically silica-based and mixed with a resin binder. This mixture is then compacted into a mold around a pattern that represents the final shape of the metal object. The use of a dry sand mixture allows for quick hardening of the mold, as the resin cures under heat instead of using moisture. After the mold is set, it is ready for pouring molten metal.
Once the metal is poured into the mold cavity, it solidifies and takes on the shape of the pattern. After cooling, the mold is broken apart to reveal the cast metal object. The resulting product often requires minimal finishing, saving both time and resources in the manufacturing process.
Advantages of Dry Sand Casting
One of the primary advantages of dry sand casting is the superior surface finish it provides. The resin-coated sand allows for finer details and smoother surfaces compared to traditional wet sand casting, where moisture can lead to rougher finishes. This characteristic makes dry sand casting particularly suitable for industries that require high-quality surface finishes, such as automotive and aerospace.
dry sand casting
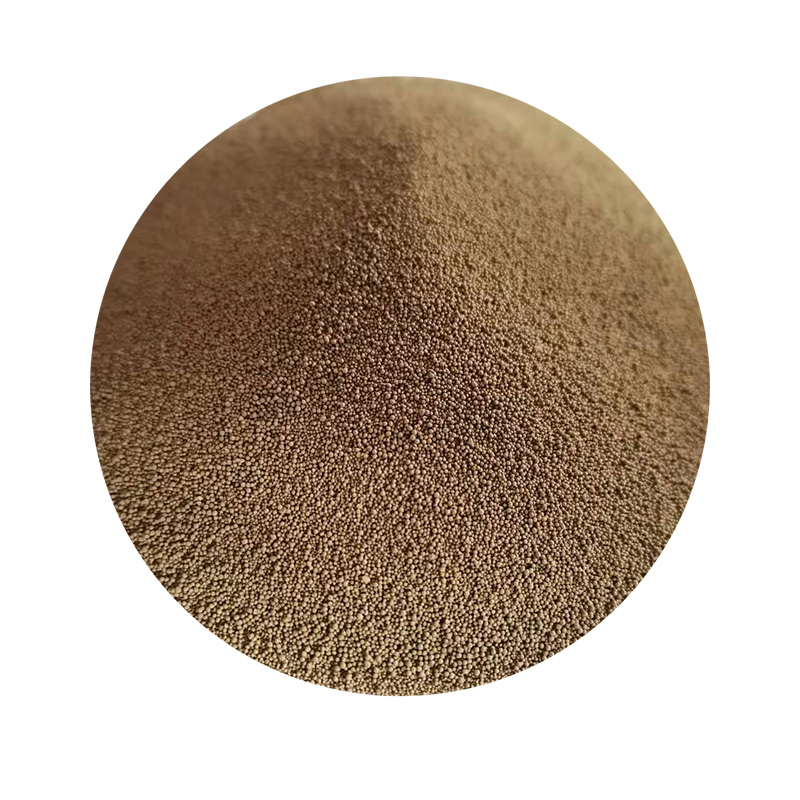
Another significant benefit is the reduction in cycle time. Because the molds set quickly and do not rely on moisture, production can occur at a faster rate. This efficiency is further enhanced by the ability to reuse the sand, making the process more economical and environmentally friendly.
Additionally, dry sand casting generates less waste compared to traditional methods. The resin-bonded sand can be reused several times before it requires replacement, significantly reducing the environmental footprint of the casting process. This reuse of materials aligns with the principles of sustainable manufacturing, making dry sand casting an appealing option for businesses looking to lessen their impact on the environment.
Applications of Dry Sand Casting
Dry sand casting is versatile and can be used for a wide range of applications across various industries. It is frequently employed in the production of intricate components in the automotive, aerospace, and industrial machinery sectors. Items such as engine blocks, turbine housings, and complex structural components can be effectively produced using this method.
Moreover, dry sand casting is increasingly being recognized in the development of prototypes. Rapid prototyping is essential for product development, and the ability to create high-quality prototypes efficiently makes dry sand casting an ideal choice for manufacturers striving to innovate quickly.
Conclusion
In conclusion, dry sand casting has emerged as a beneficial metal casting technique that offers improved surface finishes, reduced cycle times, and environmentally friendly practices. As industries continue to prioritize sustainability and efficiency, the adoption of processes like dry sand casting will likely increase. By combining traditional casting methods with modern innovations, dry sand casting not only meets the demands of contemporary manufacturing but also paves the way for a more sustainable future. The ongoing adoption and development of this technique will play a crucial role in shaping the next generation of metal casting processes.
Post time:Aug . 15, 2024 14:49
Next:Exploring the Importance of Facing Sand in Modern Metal Casting Processes and Techniques