The Utilization of Foundry Sand in Concrete An Eco-friendly Approach
In recent years, the construction industry has faced challenges related to waste management and the depletion of natural resources. One innovative solution gaining momentum is the incorporation of foundry sand into concrete mixes. Foundry sand, a byproduct from the metal casting industry, typically consists of high-quality silica sand that is reused multiple times in casting processes. However, after its useful life in foundries, large volumes of this sand often end up in landfills, creating environmental concerns. Utilizing foundry sand in concrete not only addresses waste management issues but also improves certain properties of the concrete, making it an eco-friendly alternative in construction.
Foundry sand possesses several beneficial properties that make it a suitable alternative material for concrete production. It is characterized by its fine grain size, uniformity, and chemical stability, which can enhance the workability and durability of concrete. When incorporated into concrete, foundry sand can replace a portion of traditional aggregates, such as river sand or crushed stone. This substitution can yield an effective reduction in the consumption of natural resources, which is particularly vital in regions facing aggregate shortages.
Research has demonstrated that the integration of foundry sand into concrete mix designs can yield numerous benefits. Notably, the use of foundry sand can improve the compressive strength of concrete. Studies indicate that when foundry sand replaces up to 30% of conventional fine aggregates, the resulting concrete exhibits increased strength and durability compared to standard mixes. This enhancement can be attributed to the superior grain shape and particle distribution of foundry sand, which contributes to a denser concrete matrix.
use of foundry sand in concrete
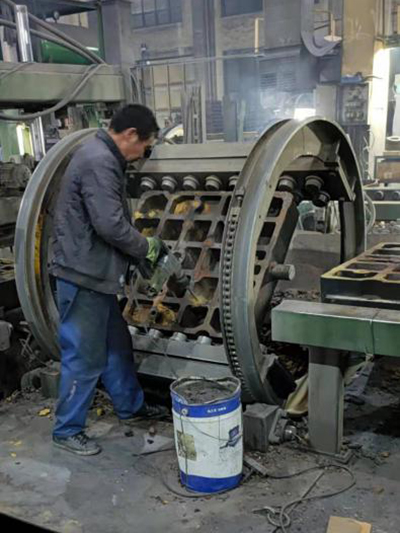
Moreover, foundry sand in concrete helps mitigate the environmental impact of construction activities. Concrete production is energy-intensive and significant CO2 emissions arise from extracting and processing traditional materials. By using foundry sand, the construction industry can reduce its carbon footprint. Additionally, reusing foundry sand helps conserve natural resources and reduces the demand for landfills, thereby promoting sustainable practices in the industry.
Despite its promising advantages, the use of foundry sand in concrete is not devoid of challenges. One primary concern is the potential presence of contaminants in foundry sand, which can derive from the mold release agents, binders, and chemicals used in the casting process. To mitigate these risks, comprehensive testing is required to ascertain the quality of foundry sand before its incorporation into concrete mixtures. Regulatory guidelines are also critical to ensure the safety and efficacy of foundry sand as a concrete ingredient.
The pathway to wider adoption of foundry sand in concrete is gaining traction, fueled by increasing awareness surrounding sustainability in construction. In various countries, initiatives are being undertaken to promote the recycling of industrial by-products like foundry sand, with significant financial incentives for construction companies willing to adopt these materials. Industry collaboration, research, and education will be essential in overcoming barriers to implementation.
In conclusion, the use of foundry sand in concrete represents a promising avenue for sustainable construction practices. By leveraging this by-product from the metal casting industry, we can effectively address waste management issues while enhancing the performance of concrete. As the world moves towards a more sustainable future, the incorporation of foundry sand in construction practices may not only contribute to environmental conservation but also pave the way for innovation and efficiency in material usage. The construction industry stands on the brink of significant transformation—embracing materials like foundry sand could be key to shaping this new, sustainable paradigm.
Post time:Jul . 22, 2024 01:02
Next:Techniques for Smoothing and Finishing 3D Print Surfaces for Optimal Painting Results