Investment Casting Sand A Key Component in Precision Manufacturing
Investment casting, also known as lost-wax casting, is a highly sophisticated manufacturing process that produces intricate and precise metal parts. One of the critical components of this process is the type of sand used for creating molds. The selection of investment casting sand plays a significant role in determining the quality and accuracy of the final product. This article will explore the various types of sand used in investment casting, their properties, and their impacts on the casting process.
The primary function of investment casting sand is to create a mold that can withstand the high temperatures involved in melting metals. Unlike traditional sand casting, which typically uses silica sand, investment casting often employs special types of sand that are chemically bonded. This ensures that the molds can handle molten metal without deforming or breaking, while also allowing for fine detail reproduction.
One of the commonly used sands in investment casting is zircon sand. Zircon sand possesses excellent thermal resistance and can withstand extremely high temperatures, making it an ideal choice for casting high-melting-point alloys. Moreover, zircon sand also provides a smooth surface finish, which is crucial for applications where surface quality is paramount, such as in aerospace or medical devices.
Another significant type of investment casting sand is olivine sand. This type of sand is known for its high melting point and stability under heat, making it suitable for use in high-temperature metal casting processes. Olivine sand also exhibits low thermal expansion, which minimizes the risk of defects in the finished casting. This characteristic allows for superior dimensional accuracy, essential for components that require precise measurements.
investment casting sand
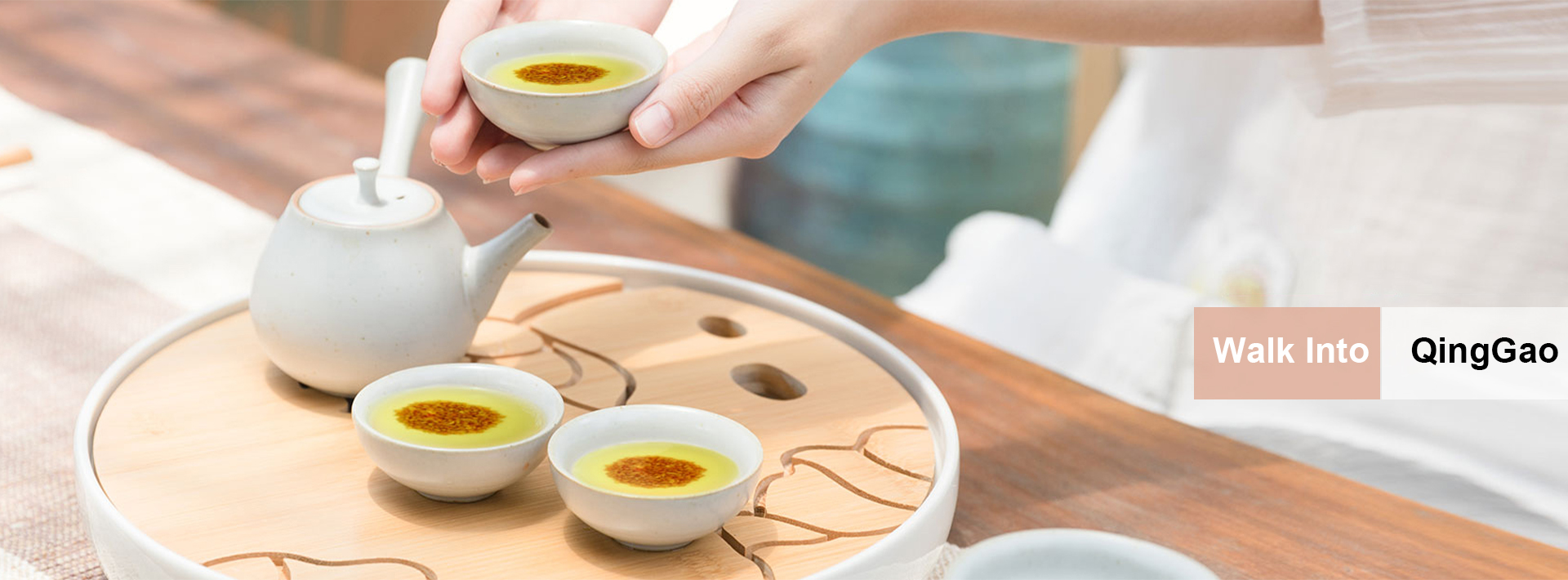
In addition to zircon and olivine sands, ceramic sand is another notable material in the investment casting process. Ceramic sands are engineered to withstand the rigors of high-precision casting. With their fine grain structure, they produce casts with smooth finishes that reduce the need for extensive post-casting machining. This property is particularly valued in industries that require tight tolerances and intricate geometries.
The selection of casting sand is not just about mechanical properties; it also involves a careful consideration of environmental and economic factors. The trend towards sustainability has led to developments in the use of recyclable sands and eco-friendly binders. Utilizing recycled materials in the casting process not only reduces waste but also lowers production costs. This shift is particularly relevant given the increasing global emphasis on sustainable manufacturing practices.
Moreover, the choice of sand can significantly influence the casting's performance characteristics. For example, the sand's thermal conductivity can affect how quickly the molten metal solidifies, which in turn can lead to either improved mechanical properties or increased defects. Hence, precise control over the casting environment, including the type of sand, is vital for achieving the desired results.
In conclusion, investment casting sand is a crucial element in the manufacturing process of precision metal components. The properties of different sands, such as thermal resistance, surface finish quality, and environmental considerations, play a fundamental role in the effectiveness and efficiency of the investment casting method. As industries continue to demand higher performance and sustainability, the evolution of investment casting sands will likely lead the way in innovation and efficiency in metal manufacturing. By understanding the role of investment casting sand, manufacturers can enhance their capabilities and ensure the production of top-quality components that meet the rigorous demands of modern applications.
Post time:Aug . 09, 2024 03:10
Next:Exploring the Features and Benefits of G2 Super Sand for Optimal Outdoor Applications