Coated Sand Casting An Overview
Coated sand casting is a widely used metal casting process that employs coated sand to create molds for various metal parts. This method has gained popularity in industries such as automotive, aerospace, and heavy machinery due to its ability to produce intricate shapes with superior surface finish and dimensional accuracy. This article explores the principles behind coated sand casting, its advantages, the materials used, and its applications in modern manufacturing.
The Principles of Coated Sand Casting
The coated sand casting process involves the use of a mixture of sand grains coated with a binding agent, typically a resin. The sand grains are combined with a specific coating to enhance their binding properties and improve the overall integrity of the mold. This process typically includes the following steps
1. Preparation of the Coated Sand The sand is coated with a resin binder and sometimes an additional hardening agent. This mixture is then thoroughly blended to achieve a uniform consistency. The most common types of binders used include phenolic resins, furan resins, and epoxy resins.
2. Mold Creation The coated sand mixture is packed around a pattern to form a mold. The pattern is removed after the sand has been compacted, leaving a cavity that mirrors the shape of the desired part.
3. Curing The coated sand mold is then cured to harden it, ensuring that it can withstand the stresses of the molten metal pouring. Curing can be achieved through various methods, such as heat curing or using chemical agents that promote hardening.
4. Metal Pouring Once the mold has been prepared and cured, molten metal is poured into the cavity. The coated sand's properties allow it to maintain its shape, preventing defects such as sand erosion during the pouring process.
5. Cooling and Finishing After the metal has cooled and solidified, the mold is broken away to reveal the cast part, which may require further finishing processes, such as machining or surface treatment.
Advantages of Coated Sand Casting
coated sand casting
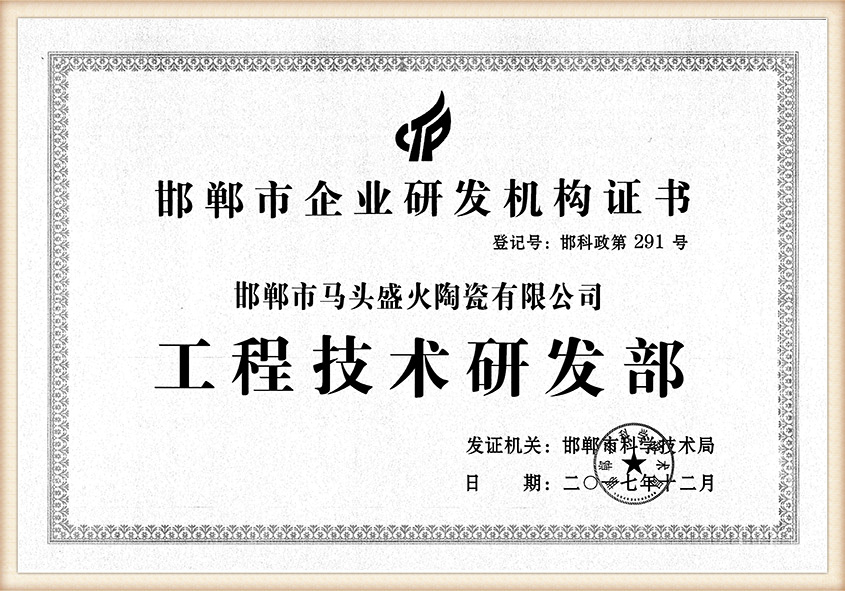
Coated sand casting offers several notable advantages over conventional sand casting methods
. Some of these benefits include- Improved Surface Finish The coated sand provides a smoother surface finish, reducing the need for post-casting machining and thereby saving time and costs in production.
- Enhanced Dimensional Accuracy The process allows for tighter tolerances and more complex geometries, which are essential in many high-precision applications.
- Versatility Coated sand casting is suitable for a wide range of metals, including aluminum, brass, steel, and cast iron, making it a versatile choice for various industries.
- Reduced Gas Porosity The use of coated sand minimizes gas defects in the final casting, resulting in stronger parts with better integrity.
Applications
Coated sand casting is utilized in numerous applications across different sectors. In the automotive industry, it is used to manufacture engine components, transmission cases, and complex brackets. The aerospace sector benefits from the lightweight and high-strength properties of cast components produced through this method. In heavy machinery, coated sand casting is employed for making parts that require resilience and high wear resistance.
Conclusion
In summary, coated sand casting is a sophisticated and effective metal casting process that combines the best qualities of sand casting with advanced coating technologies. Its ability to produce high-quality, intricate parts makes it indispensable in modern manufacturing. As technology continues to advance, the capabilities and applications of coated sand casting are expected to evolve, fulfilling the growing demands of industries that require precision-engineered components.
Post time:Aug . 18, 2024 06:40
Next:Comprehensive Sand Casting Solutions for Diverse Manufacturing Needs