Foundry Sands The Backbone of Metal Casting
Foundry sands play a critical role in the metal casting industry, serving as the primary material used to create molds in which metal is formed. These sands are integral to the casting process, providing the necessary properties for shaping molten metals into a variety of products, from intricate parts to large components utilized in various industries such as automotive, aerospace, and construction.
The Composition and Types of Foundry Sands
Foundry sands are primarily composed of silica, though they may also contain other minerals. The most common type, silica sand, is derived from quartz and is prized for its high melting point and durability. Other types include olivine sand, which has excellent thermal stability, and zircon sand, known for its resistance to metal penetration and thermal shock.
Each type of sand has unique attributes that suit different casting processes. For instance, green sand, a mixture of silica sand, clay, and water, is widely used in traditional sand casting due to its ability to retain moisture, which helps in mold strength. On the other hand, resin-coated sands are prevalent in more modern casting methods, where resin is applied to the sand to enhance its binding properties and improve the surface finish of the cast product.
The Casting Process
The casting process begins with the creation of a mold, formed by compacting sand around a pattern of the object to be cast. This pattern is removed, leaving a cavity that mirrors the shape of the final product. Molten metal is then poured into the mold cavity, filling it to form the desired object once cooled and solidified.
foundry sands
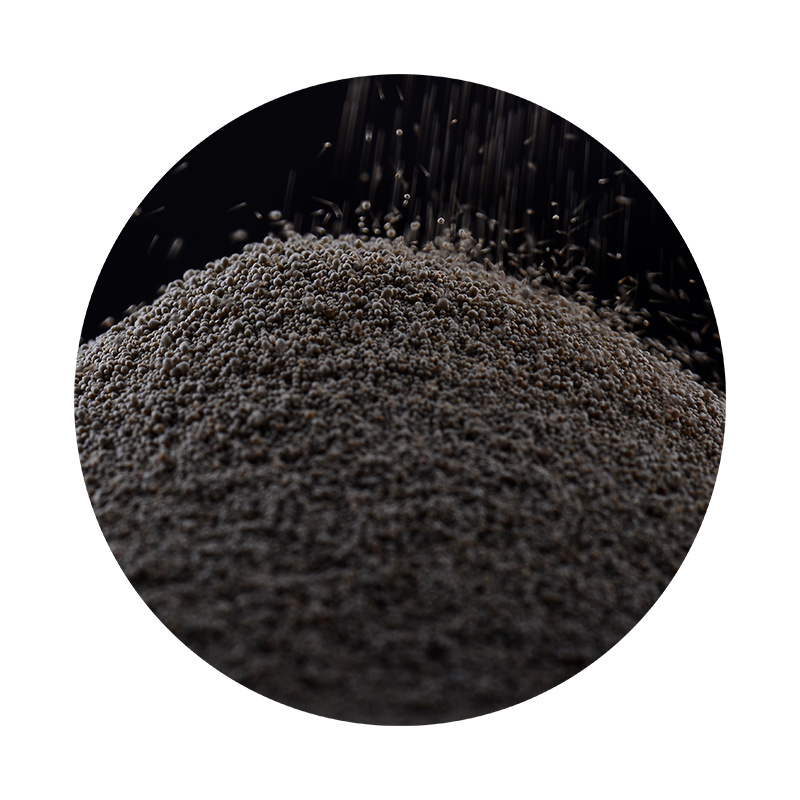
The choice of foundry sand significantly influences the quality of the castings produced. Key properties such as grain size, shape, and the distribution of sand grains can determine the mold’s permeability and strength. For example, fine grains may produce a smoother surface but can reduce the mold’s ability to vent air, while coarser grains may enhance airflow but can lead to a less detailed finish.
Environmental Considerations
While foundry sands are crucial to the industry, their extraction and use raise environmental concerns
. The mining of silica sand can lead to habitat destruction and air quality issues due to dust emissions. However, industry practices have evolved to mitigate these impacts. Many foundries are now adopting more sustainable practices, such as using recycled sand from previous casting operations, which not only conserves natural resources but also reduces waste.Additionally, innovations in foundry sand processing and treatment have led to advancements in the recycling of used sands, allowing them to be cleaned and reused in new mold creations. This not only diminishes the environmental footprint of sand extraction but also reduces operational costs for foundries.
The Future of Foundry Sands
As industries increasingly prioritize sustainability and efficiency, the future of foundry sands looks promising. Research continues to explore the development of alternative materials and additives that could enhance the properties of foundry sands, improving the casting process while minimizing environmental impacts. Furthermore, advancements in technology, such as 3D printing for mold creation, present exciting possibilities for the evolution of how foundry sands are utilized.
In conclusion, foundry sands are indispensable to the metal casting process, providing the foundation upon which industry relies for producing high-quality metal parts. As the industry navigates the challenges of sustainability and innovation, ongoing developments in foundry sand use promise to shape the future of metal casting, ensuring it remains efficient and environmentally responsible.
Post time:Aug . 06, 2024 15:10
Next:Understanding the Precision of Sand Casting Techniques for Enhanced Manufacturing Outcomes