The Steel Sand Casting Process A Comprehensive Overview
Steel sand casting is a widely utilized manufacturing technique that transforms molten metal into intricate components with precision and durability. This process is particularly favored in industries such as automotive, aerospace, and heavy machinery, where the demand for complex shapes and high strength materials are paramount. With its unique blend of versatility and cost-effectiveness, the steel sand casting process is an essential facet of modern engineering.
The Basics of Sand Casting
At its core, sand casting involves creating a mold from a sand and binder mixture. This mixture is compacted around a pattern that represents the final product. Once the mold is formed, the pattern is removed, leaving a cavity that will be filled with molten steel. The choice of sand—typically silica—along with the binder significantly influences the quality of the mold. The molding sand must possess excellent thermal properties, permeability, and cohesiveness to withstand the heat of the molten metal.
Creating the Mold
The first step in the steel sand casting process is preparing the mold. The pattern is often made from metal, wood, or plastic and is designed to accommodate the shrinkage that occurs during cooling. The mold halves, which are set into a flask, are packed with the sand mixture. This is followed by the addition of core pieces if there are any internal cavities required in the final product.
Once the mold is prepared and set, it is subjected to a process called hardening to ensure it can withstand the molten steel's temperature, which can exceed 1500°C (2732°F). Techniques like oil-bonded sand or chemical binders are employed to enhance the mold's strength and stability.
Melting and Pouring Steel
steel sand casting process
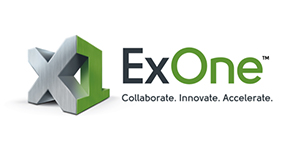
After the mold is prepared, the next step involves melting the steel. This can be accomplished using various furnaces—induction, electric arc, or cupola furnaces—depending on the desired composition and scale of production. Once the steel reaches the appropriate temperature, it is poured into the mold through a system of gates and runners designed to ensure even distribution and minimize turbulence, which can otherwise introduce defects into the cast.
Cooling and Finishing
Once the mold is filled, allowing the molten steel to cool and solidify is crucial. The cooling time will vary based on the thickness and complexity of the casting. After the steel has cooled, the mold is broken away, revealing the cast component. The casting may be rough and require further processing, such as trimming, grinding, or surface finishing, to achieve the defined specifications.
Advantages and Applications
The steel sand casting process boasts several advantages. It is capable of producing large and complex shapes that would be challenging for other manufacturing techniques. The use of sand as a molding material is cost-effective and provides flexibility for designing various patterns. Furthermore, the durability and strength of steel ensure that the final products can withstand high-stress environments, making them ideal for critical applications.
Steel sand casting finds applications in manufacturing components such as engine blocks, gears, and various structural parts. Its ability to cost-effectively produce high-strength components makes it indispensable in industries demanding reliability and performance.
Conclusion
In summary, the steel sand casting process is a foundational technique in metalworking, combining simplicity with the ability to produce complex shapes. Its applications span multiple industries and highlight the ongoing relevance of traditional manufacturing methods in today's technological landscape. As innovations continue to refine this process, steel sand casting will undoubtedly maintain its status as a cornerstone of engineering solutions.
Post time:Aug . 18, 2024 10:05
Next:The History and Evolution of Sand Casting Techniques Over the Centuries