Lost Foam Casting An Innovative Approach to Metal Casting
Lost foam casting is a sophisticated metal casting process that uniquely combines the advantages of traditional sand casting with advanced modeling techniques. This method has gained popularity in various industries due to its ability to produce complex geometries with excellent surface finishes without the need for elaborate tooling.
At its core, lost foam casting involves creating a foam pattern that is coated with a thin layer of sand, typically mixed with a bonding agent. This pattern is made from a polystyrene or polyvinyl chloride foam, which is lightweight and can be easily shaped and detailed. Once the foam pattern is constructed, it is coated in dry sand and compacted to create a mold. The key innovation of this process lies in the fact that the foam pattern is not removed prior to pouring the metal; instead, it is vaporized by the heat of the molten metal, thus creating a cavity into which the metal is poured.
Lost Foam Casting An Innovative Approach to Metal Casting
Another significant benefit is the reduction of waste material. In lost foam casting, since the foam is consumed in the process, there is minimal leftover material compared to other casting techniques, where patterns are often reused multiple times. This not only leads to a cleaner production process but also contributes to a more sustainable approach in manufacturing.
lost-foam casting
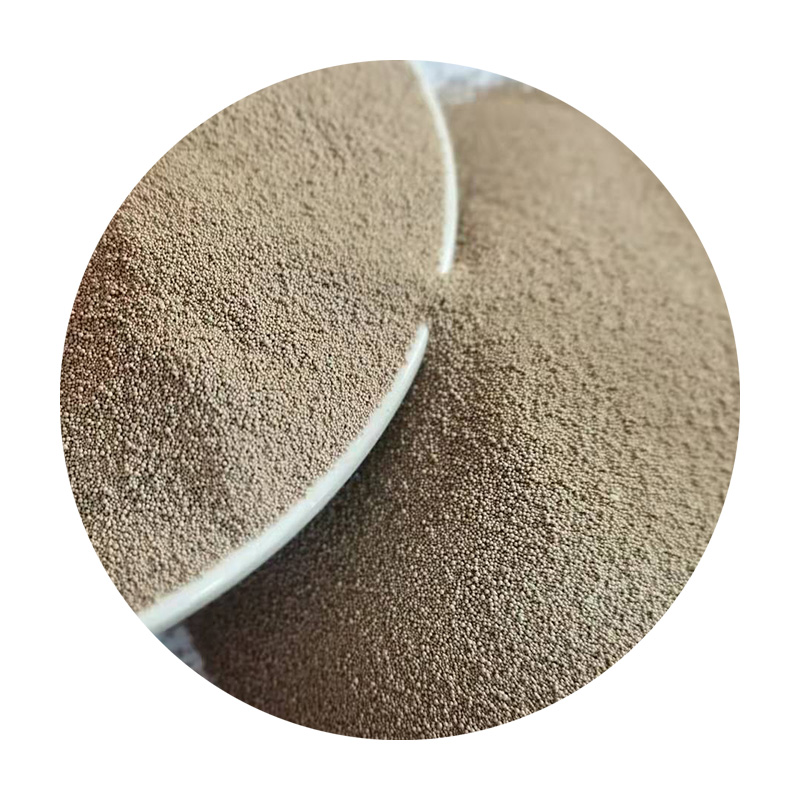
The smooth surface finish that lost foam casting offers is another advantage that sets it apart from conventional casting methods. The foam pattern produces molds that capture even the finest details, which can also reduce or eliminate the need for secondary finishing processes. This attribute is particularly valuable in applications where aesthetics and precision are crucial, such as in automotive or aerospace components.
However, the lost foam casting process is not without its challenges. One significant factor is the control of the vaporization process. If the metal is poured too quickly or at an excessively high temperature, it can lead to issues such as gas entrapment, which may compromise the integrity of the final product. Therefore, achieving optimal pouring conditions is vital for the success of this casting method.
Furthermore, while the initial investment in lost foam casting can be higher due to the need for specialized equipment and pattern-making capabilities, the long-term savings achieved through reduced waste and improved production efficiency often outweigh these costs.
In recent years, advancements in foam materials and production technology have further enhanced the capabilities of lost foam casting. Innovation in this sector continues to drive interest and application, particularly as industries look for methods that can accommodate both lean manufacturing principles and the demand for increased customization of products.
In conclusion, lost foam casting represents a unique and efficient alternative to traditional metal casting methods, offering significant advantages in terms of design flexibility, material efficiency, and surface finish quality. As technology continues to advance, this process is likely to play an increasingly important role in various manufacturing sectors, paving the way for new possibilities in the production of complex metal components.
Post time:Jul . 25, 2024 14:12
Next:Innovative Techniques in Sand 3D Printing for Creative Manufacturing Solutions and Applications