The Art and Science of Large Sand Casting
Large sand casting is a well-established manufacturing process that has been utilized for centuries. It combines creativity and engineering to produce complex metal parts used in a range of industries, from automotive to aerospace. This method involves creating a mold from sand, into which molten metal is poured to form the final product. Its versatility and cost-effectiveness make it a favored technique among manufacturers.
The Process of Large Sand Casting
The first step in the large sand casting process is to create a mold. This involves forming a mixture of sand, water, and a binding agent to ensure that the mold retains its shape. The molding material is packed around a pattern, which is a replica of the part to be cast. Patterns can be made from various materials, including metal, plastic, or wood, depending on the complexity and size of the desired object.
Once the mold is created, it is carefully removed from the pattern. This removal must be done with precision to avoid damaging the sand mold. The two halves of the mold are then assembled, and any necessary cores are placed inside to create internal cavities in the finished casting. These cores are typically made from a similar sand mixture but may include additives to improve their strength.
The next step is pouring the molten metal into the mold. The type of metal used varies according to the application's requirements, with common choices including aluminum, iron, and steel. Heating the metal until it melts requires careful temperature control to ensure the metal flows smoothly and fills all the intricate details of the mold.
After pouring, the metal is left to cool and solidify. This stage can take anywhere from minutes to hours, depending on the thickness of the casting and the type of metal used. Once cooled, the mold is broken apart to reveal the casting. The sand mold can generally be reused with some recycling of the sand, promoting sustainability in the process.
large sand casting
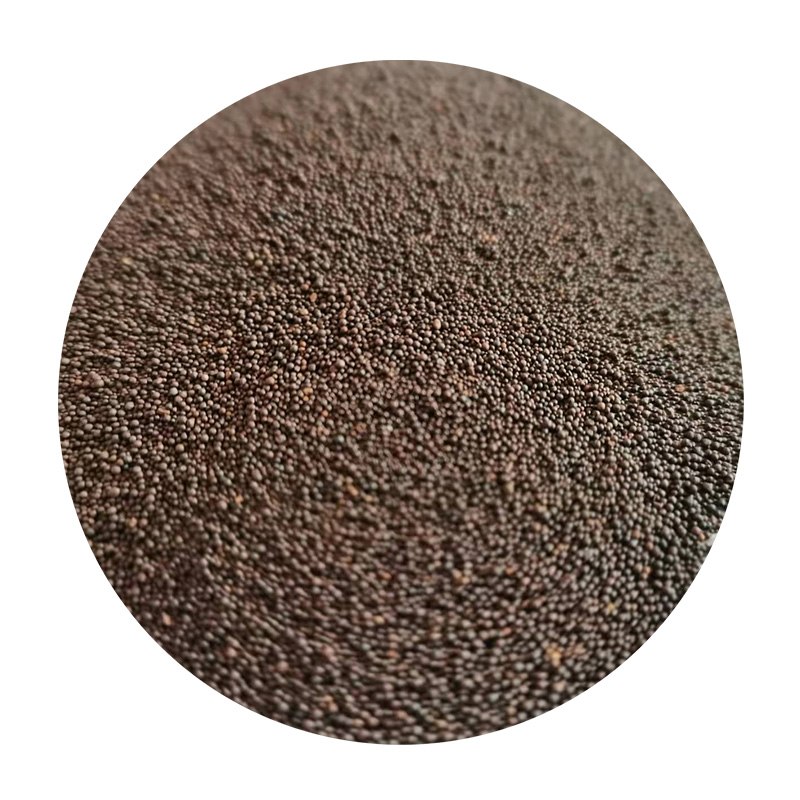
Advantages of Large Sand Casting
Large sand casting has several advantages that contribute to its enduring popularity. One of the primary benefits is its ability to produce large and complex shapes that would be challenging or expensive to create using other methods. The flexibility in mold design allows for intricate details and customizations, catering to specific technical requirements.
Moreover, casting in sand is a relatively low-cost process, especially for short production runs
. The materials—sand and binding agents—are inexpensive, and the equipment required is less demanding than that needed for other methods, such as die casting or machining. This makes large sand casting an attractive option for small manufacturers or those producing prototypes.Another advantage is the scalability of the process. While it is efficient for small batches, large sand casting can also be adapted for mass production. With the capability to create multiple molds, production can ramp up significantly without compromising quality.
Challenges and Considerations
Despite its advantages, large sand casting does present challenges. Defects such as sand inclusion, gas porosity, and dimensional inaccuracies can occur, impacting the integrity of the final product. Hence, strict quality control measures are essential throughout the process, from pattern making to the final inspection.
In summary, large sand casting encompasses a blend of art and engineering, allowing manufacturers to produce complex metal parts efficiently and cost-effectively. With its versatility, it remains a crucial technology in various industries, continually evolving to meet modern production demands. As technological advancements in materials and techniques emerge, large sand casting will likely adapt, further enhancing its role in manufacturing.
Post time:Aug . 05, 2024 02:36
Next:Explore the Talented Cast Behind the 2014 Film Sand Castles and Their Remarkable Performances