Sand Casting Techniques An Overview
Sand casting, a time-honored and versatile metal casting process, is widely utilized in manufacturing alloys and intricate components across various industries. This technique has stood the test of time due to its simplicity, cost-effectiveness, and ability to create complex shapes with excellent dimensional accuracy. This article delves into the fundamentals of sand casting techniques, their advantages, and some common applications.
The Sand Casting Process
The sand casting process involves several key steps. First, a pattern, typically made of metal, plastic, or wood, is created to represent the object being cast. This pattern is then embedded in a mixture of sand and a binder, forming a mold. The sand is usually coarse, which allows for the quick and easy removal of the pattern once the mold is formed.
1. Mold Creation The pattern is placed in a specially designed mold box. Sand is packed around the pattern, and the two halves of the mold box are brought together. The binder in the sand helps retain its shape, ensuring that the mold cavity accurately reflects the details of the pattern.
2. Pattern Removal After the mold has been made, the pattern is carefully removed, leaving a hollow cavity in the shape of the desired part. This step is crucial, as any imperfections in the mold can lead to defects in the final product.
3. Pouring the Metal The next stage involves heating the metal until it reaches a molten state. The molten metal is then poured into the mold cavity through a gating system that facilitates smooth filling of the mold. Temperature control during this phase is essential to prevent defects such as porosity or cold shuts.
4. Cooling and Solidification Once the mold is filled, the molten metal is allowed to cool and solidify. The time required for cooling can vary based on the material and thickness of the casting. This phase is critical; if the cooling occurs too quickly or too slowly, it can affect the integrity of the casting.
sand casting techniques
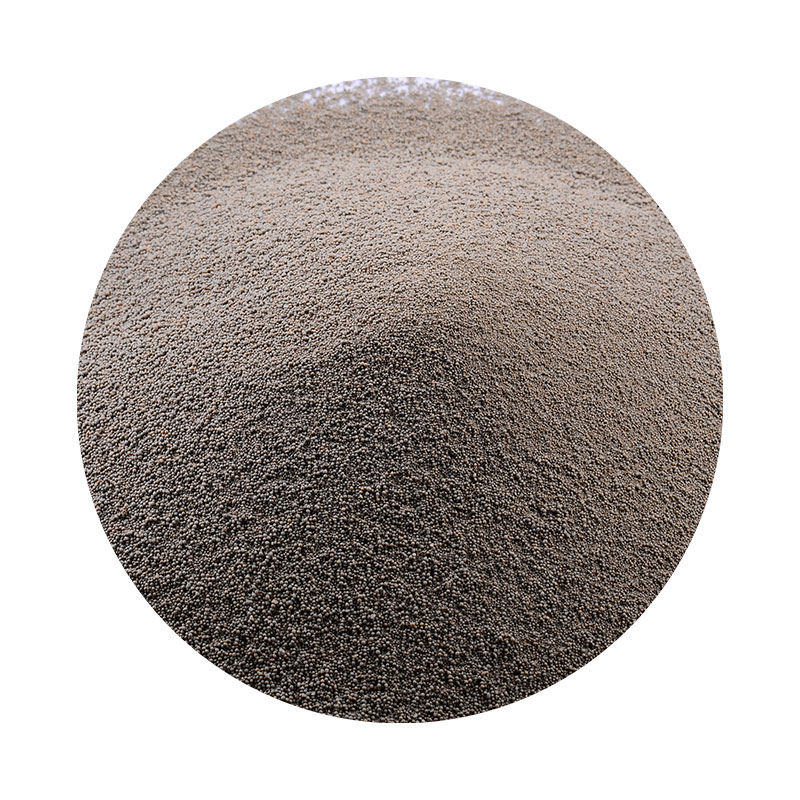
5. Mold Removal and Finishing After solidification, the mold is broken apart, and the casting is removed. Any excess material, known as flash, must be trimmed off, and surface finishing processes may be applied to improve the final appearance and dimensions of the casting.
Advantages of Sand Casting
Sand casting offers several distinct advantages that contribute to its widespread use
- Cost-Effectiveness The materials used for sand molds are relatively inexpensive, making it an attractive option for both small and large production runs. - Versatility This technique can accommodate a wide variety of metals, including aluminum, iron, and bronze, making it suitable for different applications. - Complex Shapes Sand casting can produce parts with intricate geometries that are often challenging to achieve with other methods. - Large Size Capability The process can be scaled to produce parts of large sizes, which is beneficial for industries like aerospace and automotive.
Applications
Sand casting is used in a diverse array of applications. In the automotive industry, it is commonly employed to manufacture engine blocks, transmission cases, and other structural components. The aerospace sector utilizes sand casting for producing components that require high precision and durability. Similarly, in the construction and machine tool industries, sand casting plays a vital role in creating tools, fittings, and decorative elements.
Conclusion
In conclusion, sand casting techniques offer a robust solution for manufacturers looking to produce complex and high-quality metal components. Its cost-effectiveness, versatility, and ability to create intricate designs make it a preferred choice in various industries. As technology progresses, innovations in sand casting are likely to enhance its capabilities further, ensuring that this traditional method remains relevant in the modern manufacturing landscape.
Post time:Aug . 01, 2024 08:56
Next:Achieving Smooth Finishes on 3D Printed Parts Using Sanding Techniques for Resin Models