3D Printing in Sand Casting Revolutionizing Traditional Manufacturing
In the world of manufacturing, traditional methods are often praised for their reliability and time-tested effectiveness. However, the advent of additive manufacturing, more commonly known as 3D printing, has begun to transform conventional techniques. One area where this transformation is particularly impactful is sand casting, a process traditionally used to create metal parts and components. By integrating 3D printing technology into sand casting, manufacturers are finding innovative solutions that enhance efficiency, reduce costs, and improve overall product quality.
Sand casting has been a staple in manufacturing for centuries. The process involves creating a mold from sand in which molten metal is poured to create desired shapes and components. Traditionally, these molds are produced either through manual labor or by utilizing more rigid tooling methods. While effective, these approaches can be time-consuming and costly, particularly for low-volume productions or custom parts. That’s where 3D printing comes into play.
3D Printing in Sand Casting Revolutionizing Traditional Manufacturing
Moreover, using 3D printing in sand casting significantly reduces lead times. Traditional sand casting often requires multiple steps, including pattern creation, mold assembly, and sometimes extensive finishing work. In contrast, 3D printing allows manufacturers to iterate designs quickly and produce molds in a matter of days or even hours. This rapid prototyping capability is particularly advantageous in industries like aerospace and automotive, where design iterations and custom parts are commonplace.
3d printing sand casting
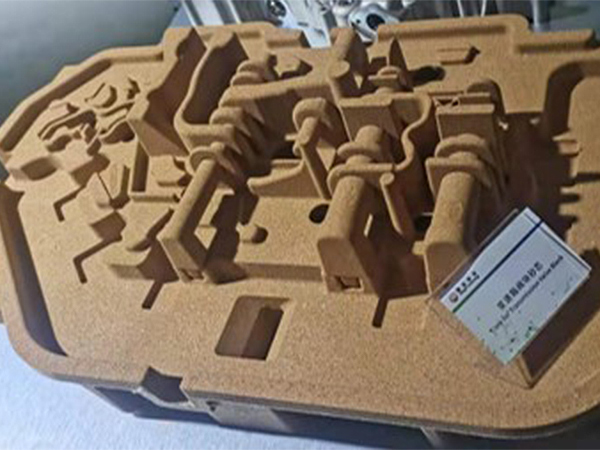
Additionally, the cost benefits of using 3D printing for sand casting can be substantial. With less material waste and the ability to produce molds on demand, manufacturers can minimize their inventory costs. Furthermore, the reduction in labor intensity and time translates to lower overall manufacturing costs. For companies looking to remain competitive in today’s fast-paced market, these financial advantages can be pivotal.
Environmental sustainability is another significant advantage offered by the integration of 3D printing into sand casting processes. Traditional casting methods often produce considerable waste, both in terms of resources and the energy required for production. In contrast, 3D printing can use recycled materials and allows for a more efficient use of raw materials. As companies strive to meet stricter environmental regulations and social responsibility standards, adopting 3D printing technology clearly aligns with these goals.
However, the transition to 3D printing in sand casting does come with its challenges. The initial investment in 3D printing technology and training can be high, particularly for smaller operations. Additionally, there can be a learning curve associated with the technology and materials used. Thus, manufacturers looking to adopt this innovative solution must assess their capacity for change and be prepared to invest in both technological infrastructure and workforce training.
In conclusion, the intersection of 3D printing and sand casting is opening new frontiers in manufacturing. By leveraging the advantages of additive manufacturing, businesses are optimizing their production processes, reducing costs, and achieving greater design flexibility while ensuring sustainability. As technology continues to evolve and more industries recognize these benefits, it is clear that 3D printing will play an increasingly crucial role in the future of sand casting and manufacturing at large. As we look to the horizon, the future of production seems not only promising but also profoundly transformative.
Post time:Jul . 29, 2024 06:10
Next:Exploring the Properties and Applications of Sand Casting Alloys in Modern Manufacturing Techniques