3D Printing Patterns for Sand Casting Revolutionizing Manufacturing
In recent years, the manufacturing industry has witnessed a significant transformation with the advent of additive manufacturing, more popularly known as 3D printing. Among its various applications, 3D printing patterns for sand casting stands out as a revolutionary approach that enhances efficiency, reduces costs, and enables greater design flexibility.
Sand casting is one of the oldest and most versatile metal casting processes. It involves creating a mold from sand to pour molten metal and produce complex shapes. Traditionally, patterns used in sand casting were made from wood, metal, or plastic, which required extensive machining and finishing processes. This not only consumed a lot of time but also incurred high costs, particularly for low-volume production runs. However, with 3D printing technology, manufacturers can create precise patterns directly from digital models, streamlining the entire production process.
3D Printing Patterns for Sand Casting Revolutionizing Manufacturing
Additionally, 3D printing reduces lead time significantly. Traditional pattern-making can take weeks, especially if multiple iterations are required. In contrast, creating a 3D model and printing it can take mere days. This rapid prototyping capability allows manufacturers to quickly iterate and refine their designs, facilitating faster development cycles and increased responsiveness to market demands.
3d printing patterns for sand casting
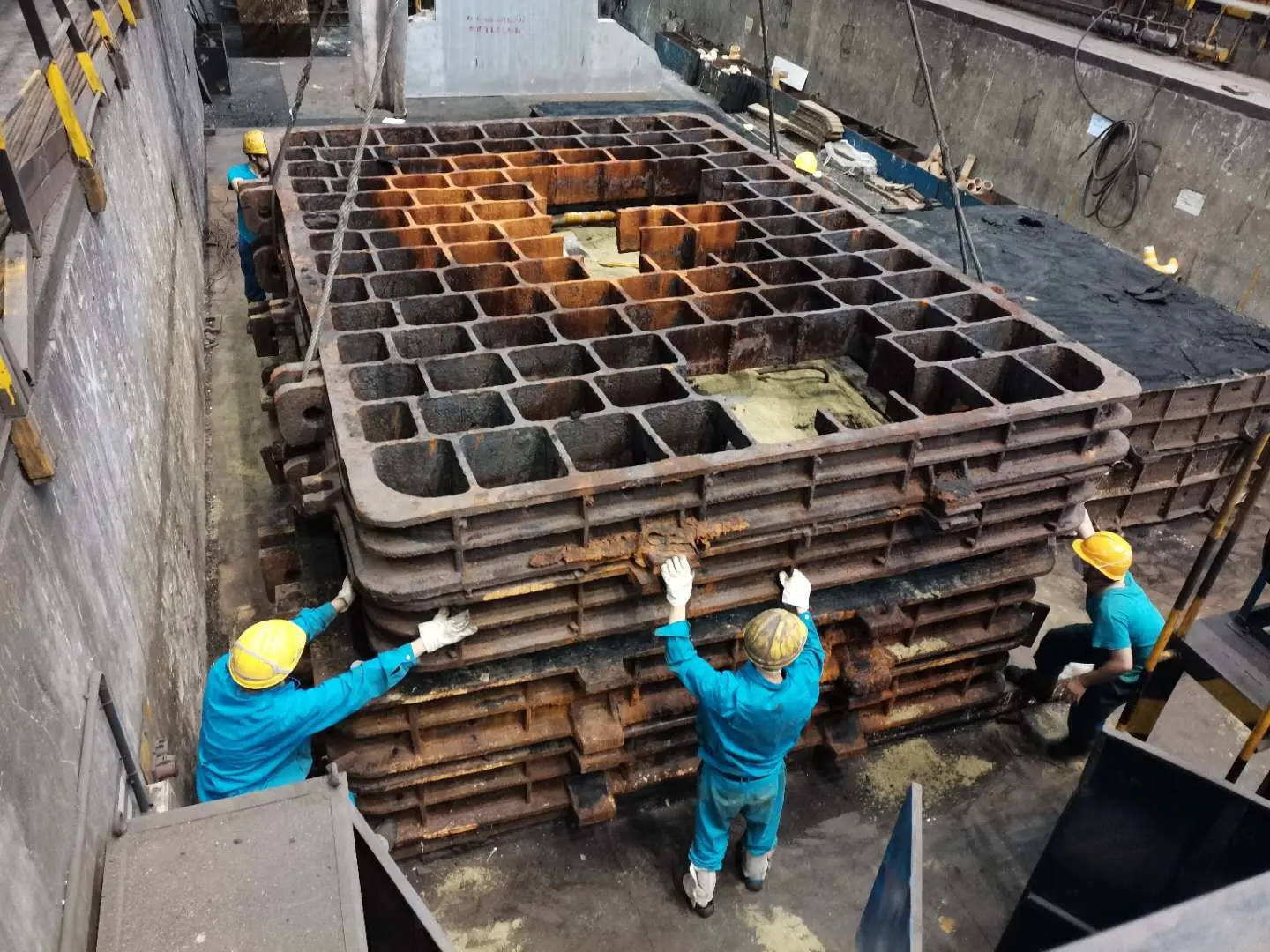
Cost efficiency is another critical benefit of utilizing 3D printing for sand casting patterns. While initial investment in 3D printing technology may seem substantial, the reduction in time and labor costs far outweighs this expense. Moreover, since 3D printing allows for the creation of patterns without the need for extensive tooling, it minimizes material waste, contributing to a more sustainable manufacturing process.
The material choices for 3D-printed patterns also enhance the advantages of this technology. Materials such as sand, resin, or thermoplastics can be used depending on the specific requirements of the casting process. Some 3D printing techniques, such as Binder Jetting, specifically use sand to create molds directly, thereby eliminating the need for a separate pattern altogether.
Furthermore, the incorporation of 3D printing in sand casting promotes collaboration across various departments within an organization. Engineers, designers, and production teams can work together using shared digital models, facilitating a more integrated workflow. This collaboration can lead to innovations in design and manufacturing processes, ultimately resulting in higher quality products.
Despite its numerous advantages, there are challenges that come with the adoption of 3D printing for sand casting patterns. Issues such as surface finish, dimensional accuracy, and the need for post-processing can impact the final output. However, ongoing advancements in 3D printing technology and materials are continually addressing these challenges, making it a more viable option for manufacturers.
In conclusion, 3D printing patterns for sand casting represents a significant leap forward in the manufacturing Landscape. With its ability to reduce lead times, enable complex designs, and lower costs, this technology is shaping the future of casting processes. As the industry continues to evolve, we can expect 3D printing to play an increasingly integral role in enhancing production efficiency and driving innovation across various sectors. The fusion of traditional casting techniques with cutting-edge 3D printing technology promises a new era of precision engineering and sustainable manufacturing practices.
Post time:Aug . 07, 2024 19:45
Next:Exploring the Techniques and Benefits of Sanding 3D Printed Objects for Smooth Finishes