The Accuracy of Sand Casting An In-Depth Analysis
Sand casting is one of the oldest and most widely used manufacturing processes for producing metal parts. It involves creating a mold from sand, into which molten metal is poured to form the desired shape. While this process is known for its versatility and cost-effectiveness, a key question arises how accurate is sand casting?
Understanding Sand Casting Accuracy
The accuracy of sand casting refers to how closely the final casted part matches the intended design specifications. Several factors influence the accuracy of sand casting, including the properties of the sand, the precision of the mold design, and the casting process itself.
1. Mold Composition and Design The type of sand used in the mold has a significant impact on the accuracy of the casting. Commonly, silica sand is used, which can be combined with various binders to enhance its properties. The mold design, including the dimensions and surface finish, also plays a vital role. A well-designed mold will minimize defects and dimensional inaccuracies, ensuring a more precise final product.
2. Pouring Technique The method by which molten metal is poured into the mold greatly influences the outcome. A consistent pouring technique helps in maintaining uniform temperature and flow rate, which reduces the likelihood of defects such as misalignment or shrinkage. If the metal cools too quickly or in an uneven manner, it can lead to warping and inaccuracies in the final part.
3. Cooling and Solidification The cooling rate of the molten metal affects its microstructure and, consequently, the mechanical properties of the final part. Rapid cooling can lead to greater thermal stresses, causing dimensional changes. Sand casting typically allows for a slower cooling process, which can enhance accuracy by minimizing distortion.
how accurate is sand casting
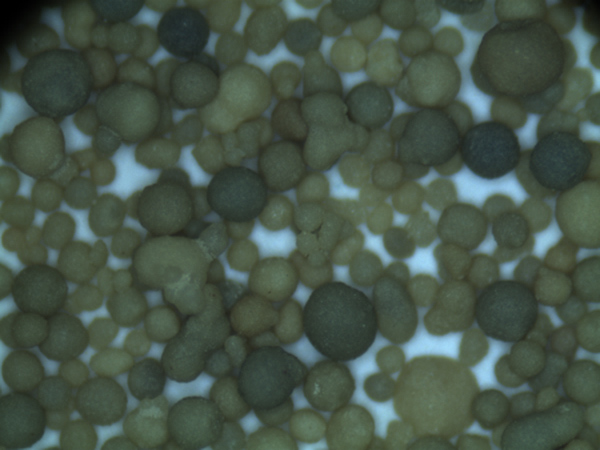
4. Post-Casting Processes After casting, various secondary processes such as machining, grinding, or surface finishing may be employed to achieve the desired specifications. While these processes can improve dimensional accuracy, they also add time and cost to production.
Tolerance Levels in Sand Casting
Sand casting is capable of achieving tolerances within ±0.5% to ±2% of the nominal dimension, depending on the size and complexity of the part. For smaller or more intricate components, tighter tolerances can be reached through careful control of the casting process and mold design. However, it is essential to note that while sand casting can achieve commendable accuracy, it may not rival the precision of other casting methods such as investment casting, which can achieve tolerances of ±0.1 mm.
Advantages and Limitations
The advantages of sand casting include its ability to produce large and complex shapes, versatility in material options, and lower production costs. However, the limitations lie in its surface finish and inherent tolerances, which may not be suitable for all applications. Industries that require higher precision components often opt for more advanced techniques, while still recognizing the benefits of sand casting for larger parts where such precision is less critical.
Conclusion
In conclusion, sand casting is a widely used method with a respectable level of accuracy suitable for various applications. While it may not achieve the extreme precision offered by more modern techniques, it remains an invaluable process in metalworking due to its adaptability and effectiveness. As technology advances, enhancements in materials and processes continue to improve the accuracy of sand casting, making it a relevant choice for production in multiple industries. Understanding its capabilities and limitations is essential for manufacturers when deciding whether sand casting is suitable for their specific needs.
Post time:Aug . 18, 2024 13:30
Next:Techniques for Sand Casting Stainless Steel in Modern Manufacturing Processes