Dry Sand Casting An Essential Technique in Metal Foundry
Dry sand casting is a widely used metal casting process that employs dry sand as the primary molding material. This innovative technique has gained popularity in the foundry industry due to its unique advantages, including versatility, precision, and cost-effectiveness.
At its core, dry sand casting involves creating a mold from a mixture of sand and a binder, which solidifies when exposed to heat. The sand used in this process is usually silica-based and is dried to remove moisture, resulting in a fine, smooth texture. The use of dry sand as opposed to wet sand eliminates the complications associated with moisture, such as gas evolution during the casting process that can often lead to defects in the final product.
One of the key benefits of dry sand casting is the ability to produce high-quality, intricate shapes. The dry sand mold can easily capture fine details, making it an ideal method for creating complex geometries that would be difficult to achieve with other casting techniques. This has made dry sand casting a preferred choice for many industries, including automotive, aerospace, and machinery manufacturing, where precision is paramount.
The versatility of dry sand casting is also noteworthy. It can be utilized for a wide range of metals, including aluminum, brass, bronze, and iron. This adaptability allows foundries to cater to various customer needs and production requirements, enhancing their competitiveness in the market. Additionally, dry sand molds can be reused several times, making the process more sustainable and cost-efficient. The recyclability of the sand further contributes to reducing waste and keeping production costs down.
dry sand casting
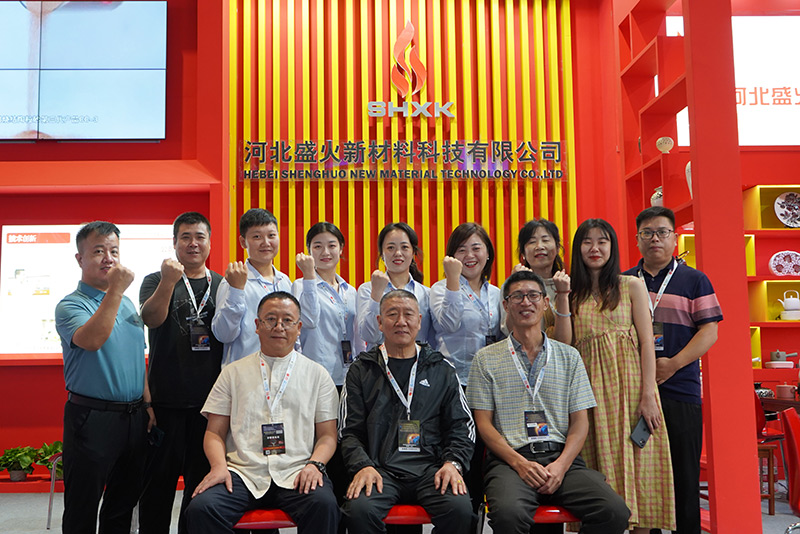
In terms of the process, dry sand casting begins with the preparation of the mold. The dry sand is mixed with a binder, typically resins or clays, which help hold the sand particles together. This mixture is then packed around a pattern—usually made of metal or wood—to form the mold. Once the mold is formed, the pattern is removed, leaving a cavity that is ready to receive molten metal.
After the mold is prepared, molten metal is poured into the cavity. Once the metal cools and solidifies, the mold is broken to reveal the final cast piece. Post-processing steps, such as grinding or machining, may be required to refine the surface finish and achieve precise dimensions.
Despite its many advantages, dry sand casting does come with some challenges. The process may require a greater initial investment in equipment and materials compared to other casting methods. Furthermore, achieving the right balance of sand and binder is crucial to avoid defects, such as mold collapse or improper filling.
In conclusion, dry sand casting is a significant technique in the metal casting industry, offering numerous benefits such as high precision, cost-effectiveness, and versatility across various metals. With its ability to produce intricate shapes and reusable molds, it plays a vital role in modern manufacturing processes. As industries continue to evolve, dry sand casting is expected to remain a cornerstone of efficient and sustainable production, meeting the demands of a dynamic market while minimizing environmental impact. This process not only reflects the ingenuity of engineering but also highlights the ongoing quest for innovation in the world of metalworking.
Post time:Sep . 28, 2024 23:19
Next:Innovative Approaches to Unique Sand Casting Techniques for Modern Manufacturing