Types of Sand Used in Sand Casting
Sand casting is a versatile and widely-used manufacturing process that involves pouring molten metal into a mold made of sand. The characteristics of the sand used in this process are crucial as they directly influence the quality of the final product. Different types of sand are employed based on various factors such as availability, cost, and the specific properties required for the casting process. This article discusses the primary types of sand used in sand casting, highlighting their unique features and applications.
1. Silica Sand
Silica sand is the most commonly used sand in the sand casting process. Composed mostly of silicon dioxide (SiO2), it has excellent resistance to high temperatures and is relatively inexpensive. The grain size and shape of silica sand can vary, which affects the permeability and flow characteristics of the molding material. It is ideal for producing a range of castings, from small components to large industrial parts. Silica sand also offers good thermal stability, making it suitable for high-temperature applications.
2. Olivine Sand
Olivine sand is another type of sand that is gaining popularity in the casting industry. It is composed mainly of magnesium iron silicate and is less susceptible to expansion, which leads to a reduced risk of casting defects such as cracks. Olivine sand has good thermal properties and is often used in steel and iron foundries. It is particularly valued for its ability to withstand high temperatures without breaking down, providing a longer lifespan compared to silica sand.
3. Zircon Sand
Zircon sand is derived from the mineral zirconium silicate and is known for its high melting point and low thermal expansion. It is often used in core making, where precision and dimensional stability are crucial. Zircon sand offers outstanding resistance to chemical attack and is beneficial for complex mold designs, ensuring excellent surface finish and dimensional accuracy. However, its higher cost compared to other sands limits its use to specialized applications.
types of sand used in sand casting
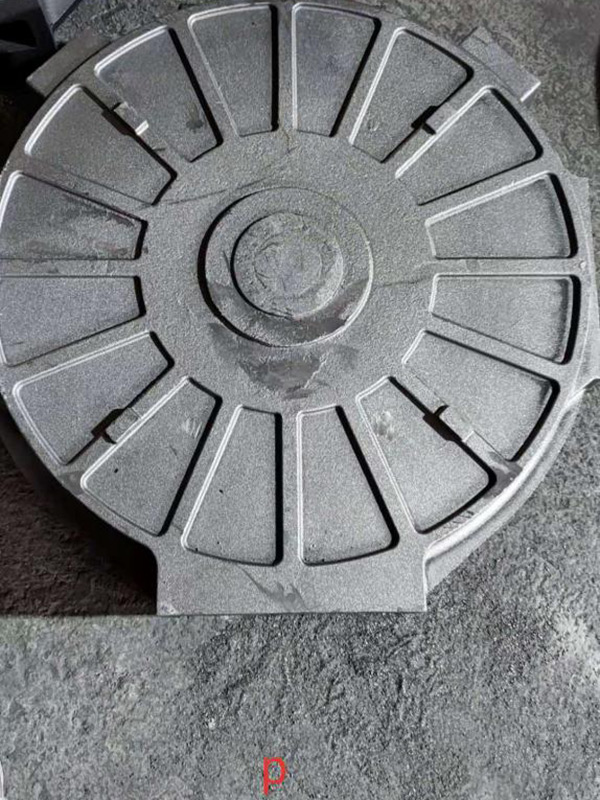
4. Chromite Sand
Chromite sand is another specialty sand used in the casting industry, primarily in the production of ferrous and non-ferrous castings. It is characterized by its high density and excellent thermal properties. Chromite sand is known for its resistance to metal penetration, making it suitable for molds and cores in high-temperature applications. The black color and fine particle size of chromite improve the surface finish of castings, giving them a smooth appearance.
5. Green Sand
Green sand refers to a mixture of silica sand, clay, and moisture. This type of sand is used for making molds in its natural, moist state, allowing it to retain its shape and strength. The clay binder helps the sand particles stick together, making green sand an ideal choice for creating intricate designs. Its excellent molding properties and ability to be recycled makes it a popular choice among foundries, especially for producing castings in bulk.
6. CO2 Sand
CO2 sand involves the use of a mixture of silica sand and a specific carbonate binder that, when exposed to carbon dioxide, undergoes a hardening process. This type of sand is known for its high strength and durability. CO2 sand is often used in processes that require a quick turnaround and is particularly valuable in applications where precision and surface finish are paramount.
Conclusion
The choice of sand in sand casting significantly impacts the quality of the final product. By understanding the different types of sand available, manufacturers can select the most suitable option based on their specific casting requirements. Silica sand remains a staple due to its affordability and versatility, while other types such as olivine, zircon, chromite, green sand, and CO2 sand offer specialized benefits for more demanding applications. As technology in material science evolves, we can anticipate further advancements in the types of sands used, contributing to improved casting processes and products.
Post time:Aug . 12, 2024 23:26
Next:Exploring the Creative Process Behind Sand Casting Techniques in Modern Manufacturing