The Sand Casting Process An In-Depth Look
Sand casting, a venerable manufacturing technique, has been used for centuries to create complex metal shapes and components. With its origins tracing back to ancient civilizations, this process remains a cornerstone in the field of metallurgy and engineering due to its versatility, cost-effectiveness, and ability to produce intricate designs. In this article, we will explore the sand casting process, its advantages, materials, and applications.
Overview of Sand Casting
Sand casting involves creating a mold from a mixture of sand and a bonding agent, which is then used to produce metal castings. The basic steps in the sand casting process include pattern making, mold preparation, pouring, and finishing. Each step plays a crucial role in ensuring the quality and accuracy of the final product.
Step 1 Pattern Making
The first step in sand casting is the creation of a pattern, which acts as a model for the metal piece being produced. Patterns can be made from various materials, including wood, metal, or plastic, and they are typically slightly oversized to account for shrinkage that occurs as the metal cools. There are two primary types of patterns single-piece patterns and multi-piece patterns. The choice of pattern depends on the complexity of the design and the number of castings required.
Step 2 Mold Preparation
Once the pattern is created, the next step is to prepare the mold. This involves taking the pattern and embedding it into a mixture of sand and a bonding agent, typically clay or resin. The sand used in sand casting is usually silica, owing to its high melting point and thermal stability. The sand and bonding agent are mixed and pressed around the pattern to form a mold cavity. The mold is then taken apart, and the pattern is removed, leaving a cavity that mirrors the shape of the desired metal piece.
To ensure the mold can withstand the heat of the molten metal, it is often baked or cured
. Furthermore, gates and risers are created to allow for the flow of molten metal and to compensate for shrinkage during cooling.Step 3 Pouring
describe sand casting process
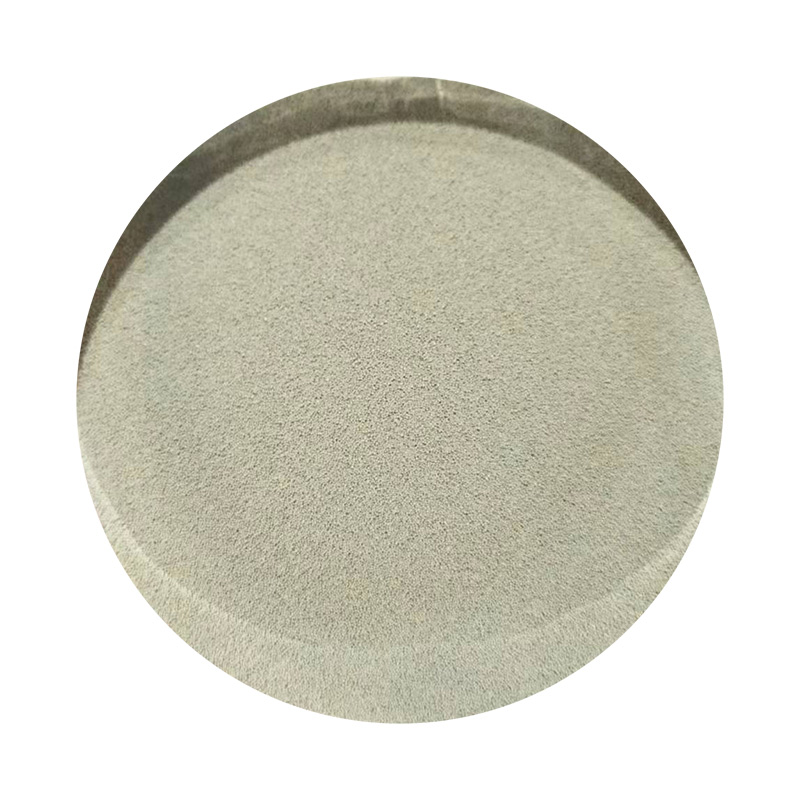
After the mold has been prepared, the next step is pouring the molten metal into the mold cavity. The metal is heated until it reaches a liquid state and is then poured through the gates into the mold. This process requires precision; if the temperature of the molten metal is too low, it may solidify before completely filling the mold, leading to flaws or incomplete castings. Conversely, if the temperature is too high, it can lead to defects such as gas porosity or excessive oxidation.
Step 4 Cooling and Finishing
Once the mold is filled, the metal must cool and solidify. Depending on the type of metal and the thickness of the casting, this can take anywhere from a few minutes to several hours. After the metal has cooled sufficiently, the mold is broken apart to reveal the cast piece. This step, known as shakeout, can be quite labor-intensive, especially for complex designs.
Following the removal of the casting, finishing processes are applied to achieve the desired tolerances and surface finish. This may include trimming excess metal, grinding, sanding, or machining to refine the product further.
Advantages of Sand Casting
The sand casting process offers several significant advantages. Firstly, it is capable of producing large parts in a cost-effective manner, making it ideal for both small and large production runs. Secondly, the use of sand as a mold material allows for excellent flexibility in design, supporting intricate, complex shapes that might be difficult or impossible to achieve with other methods. Finally, sand casting can accommodate a wide variety of metals, including aluminum, brass, steel, and iron.
Applications of Sand Casting
Sand casting is utilized across diverse industries, including automotive, aerospace, marine, and general manufacturing. Components such as engine blocks, pump housings, and specialized machinery parts are often produced using this method. Furthermore, its ability to create custom one-off parts makes it an invaluable technique for prototype development.
Conclusion
The sand casting process is a time-honored technique that combines art and engineering to produce metal components of varying complexity. Its unique capabilities, from flexibility in design to cost-effectiveness and suitability for various metals, ensure its relevance in modern manufacturing. As industries continue to evolve, sand casting remains a vital process, underscoring the harmony between tradition and innovation in the world of metallurgy.
Post time:Nov . 20, 2024 05:21
Next:iron sand casting