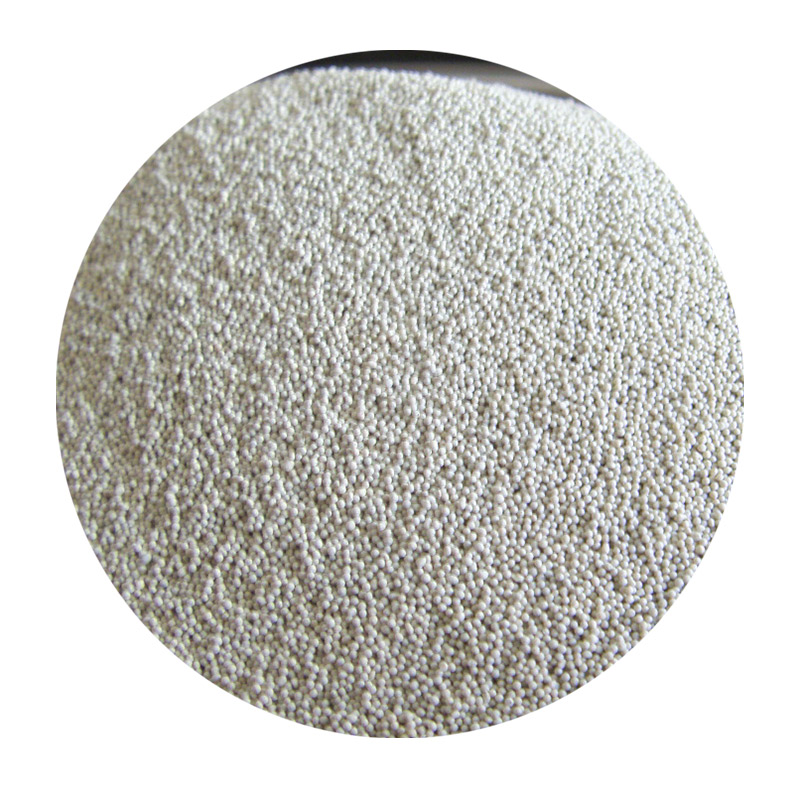
sand casting. It is often used for producing automotive parts, industrial machinery components, and even artistic sculptures. The process is particularly well-suited for producing large parts that would be difficult or expensive to produce using other casting methods. One of the key advantages of sand casting is its cost-effectiveness. Unlike other casting methods that require expensive molds to be made, sand casting uses readily available materials like sand and wood, making it a cost-effective option for producing large quantities of parts. Additionally, sand casting is a relatively simple process that can be easily scaled up or down to accommodate different production volumes. Despite its advantages, sand casting does have some limitations. The process can be time-consuming, as the mold must be carefully prepared and the metal allowed to cool and solidify. Additionally, sand casting may not be suitable for producing parts with very tight tolerances or intricate details, as the sand mold may not be able to accurately reproduce complex shapes. In conclusion, sand casting is a versatile and cost-effective method of metal casting that has been used for centuries to produce a wide range of parts. While it may not be suitable for all applications, sand casting remains a popular choice for producing large, complex parts in a cost-effective manner. Whether you're looking to produce automotive parts or ornate sculptures, sand casting can offer a reliable and efficient solution for your casting needs. Post time:Jul . 11, 2024 02:41
Next:sand casting process for creating metal parts using molds made from sand