Sand Casting Service An Essential Manufacturing Process
Sand casting, one of the oldest and most widely used metal casting processes, plays a crucial role in modern manufacturing. It involves creating metal parts by pouring molten metal into a sand mold, which solidifies to form the final product. This article explores the significance of sand casting services, their advantages, applications, and the technology behind this manufacturing method.
Understanding Sand Casting
The sand casting process begins with creating a mold from a mixture of sand, clay, and water. This mixture is shaped into a cavity that reflects the desired object. Once the mold is prepared, molten metal—usually aluminum, iron, or bronze—is poured into the cavity. After cooling and solidifying, the mold is broken away to reveal the cast part. This process can produce a wide variety of parts, ranging from simple shapes to complex structures with intricate details.
Advantages of Sand Casting
One of the primary reasons for the popularity of sand casting services is their versatility. The process is suitable for casting a wide range of metals and allows for varying sizes, from small components to large structures. Additionally, the relative low cost of materials used in sand casting, combined with the ability to produce complex shapes, makes it an economical choice for many manufacturers.
Speed is another advantage. Sand molds can be made relatively quickly, enabling fast turnaround times for production. This is particularly beneficial for projects requiring prototypes and small batch runs. Moreover, sand casting is ideal for creating parts that require high strength and durability, which is often essential in industries such as automotive, aerospace, and construction.
Applications of Sand Casting
sand casting service
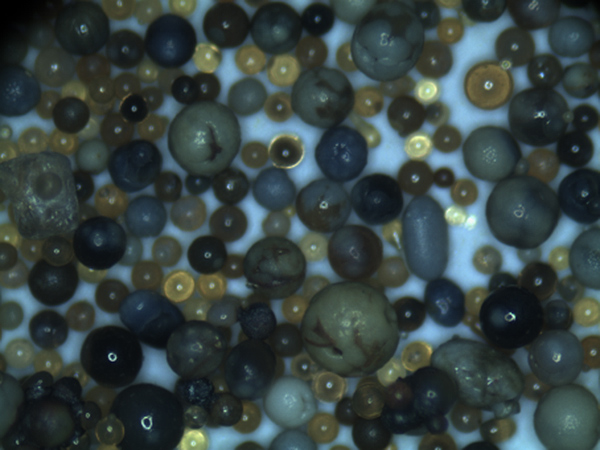
Sand casting is utilized across a variety of industries due to its adaptability. In the automotive sector, it is commonly used for producing engine blocks, transmission housings, and other critical components. The aerospace industry also relies on sand casting to create lightweight yet strong parts that can withstand extreme conditions.
Furthermore, sand casting services play a vital role in manufacturing machinery and tools, as well as in the production of artistic and decorative metal pieces. Custom sand casting is also gaining traction among hobbyists and small businesses looking to create unique designs without the need for expensive tooling.
Innovations in Sand Casting Technology
While sand casting is a traditional method, technological advancements have improved its efficiency and precision. The introduction of computer-aided design (CAD) allows for better mold designs, resulting in a more accurate representation of the intended part. Furthermore, modern techniques like 3D printing are being integrated into the sand casting process, enabling faster mold creation and enhanced design complexity.
Another notable innovation is the use of environmentally friendly sand mixtures that minimize waste and reduce the environmental impact of the casting process. As sustainability becomes increasingly important across industries, these advancements help sand casting services adapt to environmental regulations and customer expectations.
Conclusion
In summary, sand casting services remain a foundational component of the manufacturing landscape. Its versatility, cost-effectiveness, and ability to produce high-quality parts for a wide range of applications ensure its continuing relevance in an ever-evolving industry. As technology advances, the process is poised to become more efficient and environmentally friendly, solidifying its position as a preferred choice for manufacturers around the globe. Whether for large-scale production or custom projects, sand casting continues to be an indispensable method for creating durable and precise metal components.
Post time:Aug . 01, 2024 10:01
Next:Exploring the Benefits and Techniques of Wet Sanding for Resin Projects and Finishes