Understanding Sand Casting Components An Essential Guide
Sand casting, also known as sand mold casting, is an integral part of metalworking that has been widely used in various industries for thousands of years. It is a versatile and cost-effective method of producing complex metal parts with high precision. This process is characterized by the use of sand as a primary molding material, allowing for the reproduction of intricate designs and shapes. In this article, we will explore the components involved in sand casting, highlighting their roles and importance in achieving a successful casting.
1. Mold Patterns
The mold pattern is a critical component of the sand casting process. Patterns are replicas of the final product and can be made from various materials, including wood, metal, or plastic. The pattern is used to create an impression in the sand, forming the cavity into which molten metal will be poured. Patterns are typically slightly larger than the final product to account for shrinkage that occurs when the metal cools and solidifies. The design of the pattern can greatly influence the quality of the cast, as factors such as surface finish and dimensional accuracy depend on its precision.
2. Sand
The type of sand used in sand casting is another crucial component. The most commonly used sand is silica sand, which is mixed with a binder (such as clay) and water to enable it to hold its shape. The mixture must have the right balance of cohesiveness and permeability to ensure that it can withstand the molten metal and allow gases to escape during the pouring process. Different types of sand and binders can be employed depending on the specific requirements of the casting, such as the desired surface finish and strength.
3. Flask
The flask is a container that holds the sand mold. It is typically composed of two parts the cope (top half) and the drag (bottom half). The flask must be sturdy enough to withstand the pressure of the poured metal while also allowing for ease of removal of the molded part. Using a flask aids in maintaining the shape of the mold during the pouring and cooling processes, which is essential for achieving dimensional stability in the final product.
sand casting components
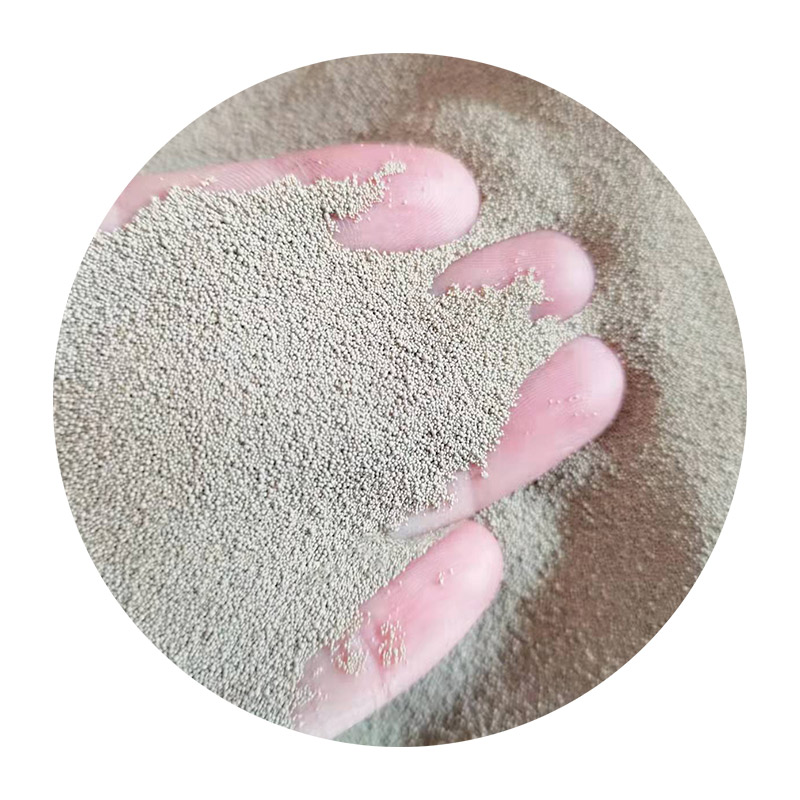
4. Core
Cores are additional components used in sand casting to create internal cavities within the cast object. These are usually made from sand and are placed inside the mold cavity before pouring the molten metal. Cores are essential for complex designs that require hollow sections, as they allow for the production of features that would otherwise be difficult to achieve. The core must be securely positioned to prevent displacement during pouring, which could lead to defects in the final casting.
5. Pouring System
The pouring system is responsible for delivering molten metal into the mold cavity. It usually consists of a pouring basin, sprue, runners, and gates. The pouring basin is where the molten metal is initially held before being guided through the sprue and into the runners, ultimately reaching the mold cavity through the gates. A well-designed pouring system is crucial for ensuring a steady and controlled flow of metal, which minimizes turbulence and helps prevent defects such as air pockets or inclusions.
6. Finishing Tools
Finally, after the casting has cooled and solidified, various finishing tools are used to remove excess material, smooth rough edges, and achieve the desired surface finish. Techniques such as sandblasting, machining, and grinding may be employed to ensure that the final product meets quality standards and specifications.
In conclusion, understanding the components of sand casting is vital for anyone involved in the manufacturing sector. Each component plays a crucial role in the overall success of the casting process, directly impacting the quality, precision, and efficiency of metal parts production. With the right materials and techniques, sand casting can yield high-quality products that meet the diverse needs of modern industries.
Post time:Aug . 22, 2024 05:56
Next:Applications and Benefits of Foundry Sand in Various Industries