Parts of Sand Casting
Sand casting is one of the oldest and most widely used manufacturing processes for creating metal parts. It offers a unique combination of versatility and cost-effectiveness, making it particularly suitable for producing complex designs in various sizes. This article will explore the essential components of the sand casting process, highlighting their significance and functionality.
At the heart of the sand casting process is the mold. A mold is a hollow cavity into which molten metal is poured to form a specific shape. Molds are typically created using two halves, called cope and drag. The cope is the upper half, while the drag is the lower half. The two halves come together to create the desired shape. Molds can be made from various materials, but sand is the most common due to its availability, cost-effectiveness, and ability to withstand high temperatures. The sand used in the molds is often mixed with a binder such as clay to improve its strength.
Parts of Sand Casting
A critical aspect of the sand casting process is the pattern. A pattern is a replica of the object to be cast and is used to create the mold cavity. Patterns can be made from various materials, including wood, metal, or plastic, and can be either solid or split patterns. Split patterns consist of two halves, allowing for easier mold removal. The pattern's size must be slightly larger than the final product to account for shrinkage as the metal cools.
parts of sand casting
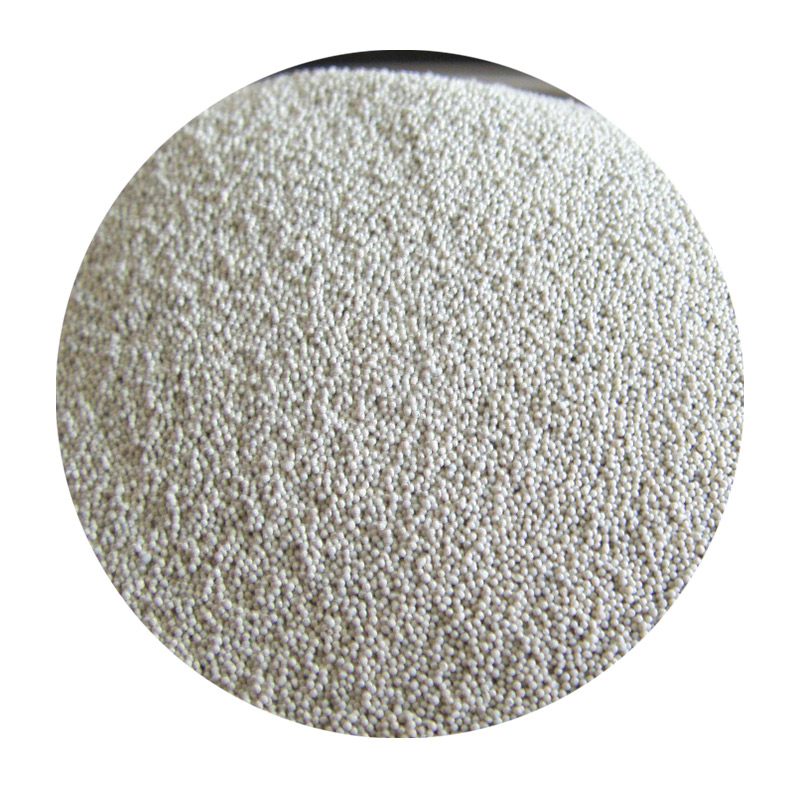
Once the pattern is created, it is placed in a flask, which holds the sand in place during the molding process. The sand is packed tightly around the pattern to form the mold. This step requires skill to ensure that the sand retains its shape and does not crumble when the pattern is removed. After the sand is packed, the pattern is removed, leaving a negative impression of the desired shape.
When the mold is ready, the next step involves pouring the molten metal into the mold cavity. The metal is heated until it reaches a liquid state and is then poured through a pouring basin into the mold. It is important to control the pouring process to avoid defects such as air bubbles or inclusions, which can compromise the integrity of the casting.
Finally, once the metal has solidified, the mold is broken open to reveal the cast part. This step often requires additional finishing processes, such as machining, to achieve the required tolerances and surface finish.
In conclusion, the parts of sand casting include molds, cores, patterns, flasks, and the molten metal itself, each playing a crucial role in the overall process. The versatility of sand casting allows for the production of a wide array of metal components, from simple to complex shapes. This traditional method continues to be a preferred choice in various industries due to its adaptability, cost-efficiency, and ability to produce high-quality castings. Whether it is for automotive parts, machinery components, or artistic sculptures, sand casting remains a fundamental technique in modern manufacturing.
Post time:Aug . 18, 2024 03:36
Next:Understanding Steel Sand Casting Techniques for Enhanced Manufacturing Processes