The Differences Between Sand Casting and Die Casting
Casting processes are widely used in manufacturing for creating complex parts and components from various metals. Two of the most prevalent casting methods are sand casting and die casting. While both techniques have their unique advantages and applications, they differ significantly in terms of materials used, manufacturing processes, costs, and the quality of the finished products. This article explores the primary differences between sand casting and die casting.
1. Casting Process
Sand Casting involves creating a mold from a mixture of sand, clay, and water. The sand is packed around a pattern, which is then removed, leaving a hollow cavity shaped like the desired component. Molten metal is poured into this mold, and after it solidifies, the sand mold is broken away to retrieve the cast part. This method is versatile and can accommodate a wide variety of sizes and shapes.
In contrast, Die Casting employs a more complex mold made from steel or other durable materials. The process involves injecting molten metal under high pressure into a pre-formed, intricately designed mold (or die). This high-pressure injection allows for the production of parts with thin walls and smooth surfaces, making it ideal for mass-producing complex shapes with precision.
2. Materials Used
The choice of materials differs between the two casting methods. Sand Casting can work with a wide range of materials, including aluminum, bronze, iron, and various alloys. This versatility makes it suitable for large parts or small production runs.
On the other hand, Die Casting is typically limited to non-ferrous metals like aluminum, zinc, and magnesium due to the high temperatures involved and the material properties needed for the dies
. However, die casting can produce parts with better surface finish and dimensional accuracy compared to sand casting.difference between sand casting and die casting
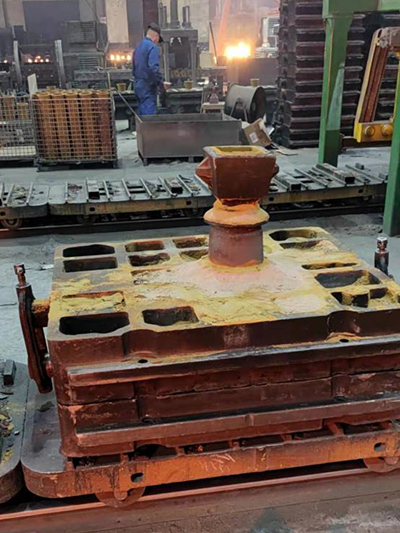
3. Cost Considerations
Cost differs significantly between these two methods. Sand Casting generally has lower initial costs since it requires simpler molds and less expensive equipment. This makes it a more economical choice for low-volume production or prototyping. However, the surface finish and dimensional tolerances might not be as high, which could lead to additional costs in post-processing.
Conversely, Die Casting entails higher tooling costs and requires intricate, reusable molds that can be expensive to produce. Despite the higher initial costs, die casting becomes more economical in high-volume production scenarios due to its efficiency and reduced finishing costs. The ability to produce parts with fine details and smoother finishes also translates into lower assembly costs.
4. Product Quality and Precision
One of the most significant differences between the two methods is in the quality and precision of the final products. Sand Casting can produce large, heavy items but often results in rougher surfaces and less precise dimensions. It may require significant machining for critical applications where tolerances are tight.
Die Casting, however, excels in producing parts with excellent dimensional stability and surface quality. The precision of the die casting process results in components that often require little to no secondary machining. This advantage makes die casting a preferred choice for components that need to fit tightly or operate in precision mechanisms.
Conclusion
In summary, both sand casting and die casting have their own merits and applications, shaped by their processes, materials, costs, and product quality. While sand casting offers flexibility and lower costs for small batches or prototypes, die casting stands out in terms of precision and efficiency for mass production. Understanding these differences is vital for manufacturers in selecting the appropriate casting method for their specific needs.
Post time:Jul . 20, 2024 10:46
Next:Exploring the Innovative Properties and Applications of G2 Super Sand Bond Technology in Construction