Difference Between Die Casting and Sand Casting
When it comes to metal casting techniques, two of the most common methods are die casting and sand casting. Each method has its own unique advantages, applications, and considerations, making them suitable for different types of projects and industries. Understanding the differences between these two casting techniques is crucial for selecting the best method for a specific manufacturing need.
Die Casting
Die casting is a manufacturing process that involves forcing molten metal into a mold, or die, under high pressure. This process is typically used for non-ferrous metals like aluminum, zinc, and magnesium. Die casting offers a range of benefits, including high production rates, dimensional accuracy, and smooth surface finishes. The process is highly automated, making it efficient for large-scale production runs. Products created through die casting often require minimal machining, which helps reduce overall production costs.
However, die casting has its limitations. The initial investment for die casting equipment and molds can be significant. The molds themselves must be highly durable and are usually made from steel to withstand high pressures and temperatures. This means die casting is most cost-effective for high-volume production where the setup costs can be spread over many parts. Furthermore, the process is less suitable for large or complex shapes due to the limitations of the die geometry.
difference between die casting and sand casting
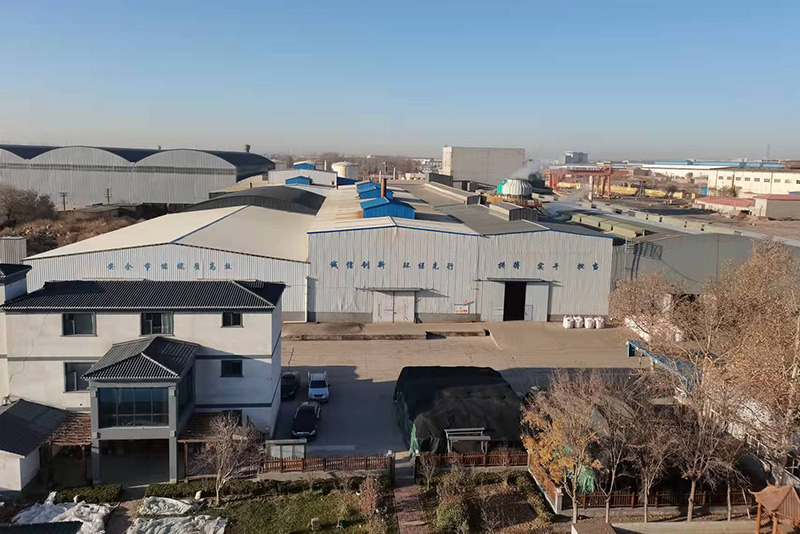
Sand Casting
On the other hand, sand casting is a more traditional method that involves creating a mold from sand mixed with a binding agent. The molten metal is then poured into the mold to take its shape. Sand casting is versatile and can accommodate a wide range of metals, both ferrous and non-ferrous. It is particularly beneficial for creating large castings, intricate designs, or prototypes.
One of the main advantages of sand casting is its lower cost for small production runs. The molds can be made quickly and do not require the same level of investment as die casting. Additionally, sand casting allows for greater flexibility in terms of design and mold complexity. However, this method typically results in a rougher surface finish and lower dimensional accuracy compared to die casting, which may require more extensive post-processing work.
Conclusion
In summary, the choice between die casting and sand casting largely depends on the specific needs of the project. Die casting excels in high-volume, precision production with excellent surface finishes, while sand casting offers flexibility and lower initial costs for smaller runs or more complex parts. Manufacturers must weigh the advantages and drawbacks of each method when deciding which casting process best meets their production requirements. Ultimately, understanding these differences will ensure that the right casting method is utilized for optimal results.
Post time:Aug . 24, 2024 00:48
Next:चीनमा बालुवा ढालने प्रविधि र यसको फाइदाहरू