Advantages of Lost Foam Casting
Lost foam casting is an innovative manufacturing process that has gained popularity in various industries due to its unique characteristics and advantages over traditional casting methods. This casting technique involves creating patterns from expanded polystyrene (EPS) foam, which are then used to produce metal castings. Below, we explore the key advantages of lost foam casting, explaining why it has become a preferred choice for many manufacturers.
1. Precision and Detail
One of the most significant advantages of lost foam casting is its ability to produce highly detailed and intricate designs. The foam patterns can capture fine features and complex geometries that might be challenging to achieve with conventional casting methods. This precision is particularly beneficial in industries such as aerospace, automotive, and artistic applications where exact specifications and complex shapes are crucial.
Lost foam casting is an efficient process that minimizes material waste. The foam patterns are created to closely match the final dimensions of the casting, which reduces the need for extensive machining and finishing. This not only saves raw materials but also lowers production costs. Furthermore, since the foam is burnt away during the casting process, it does not leave behind any patterns or molds, making the process environmentally friendly.
3. Single-Step Process
In traditional casting methods, multiple steps are often required to create a mold, pour the metal, and finish the product. Lost foam casting simplifies this process into a single step. The foam pattern is directly coated with a refractory material, and metal is poured directly onto it. This streamlined approach accelerates production times and decreases labor costs, making it an attractive option for manufacturers looking to improve efficiency.
advantages of lost foam casting
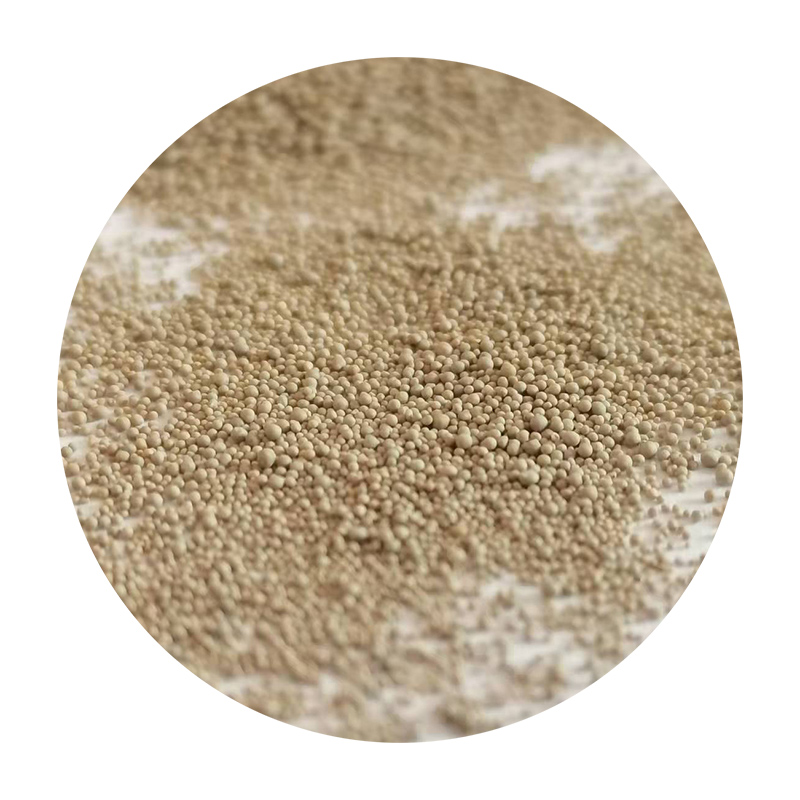
4. Versatility in Materials
Lost foam casting can be used with a variety of metals, including aluminum, iron, and bronze. This versatility allows manufacturers to tailor the casting process to meet the specific requirements of their products. Whether it’s lightweight components for vehicles or intricate parts for machinery, lost foam casting can accommodate a wide range of materials, enhancing its application potential across different sectors.
5. Excellent Surface Finish
The surface finish achieved through lost foam casting is generally superior to that of other casting processes. The nature of the foam pattern allows for a smooth surface that often eliminates the need for additional machining or surface treatment. This leads to significant reductions in post-casting processes, further enhancing cost-effectiveness and production efficiency.
6. Cost-Effectiveness for Low to Medium Volume Production
While lost foam casting can be more expensive for high-volume production due to the costs associated with foam pattern creation, it proves to be extremely cost-effective for low to medium volume runs. The reduced tooling costs and minimized waste make it an appealing option for custom parts or limited production series, providing manufacturers with flexibility and economic advantages.
Conclusion
In summary, lost foam casting offers a range of advantages that make it an attractive option for modern manufacturing. From its ability to produce intricate designs with a high degree of precision to its cost-effective nature and reduced environmental impact, this casting method presents numerous benefits. As industries continue to seek innovative and efficient production methods, lost foam casting is likely to play an increasingly prominent role in the future of manufacturing.
Post time:Aug . 17, 2024 11:07
Next:Exploring the Types of Sand Utilized in Foundry Applications and Their Importance