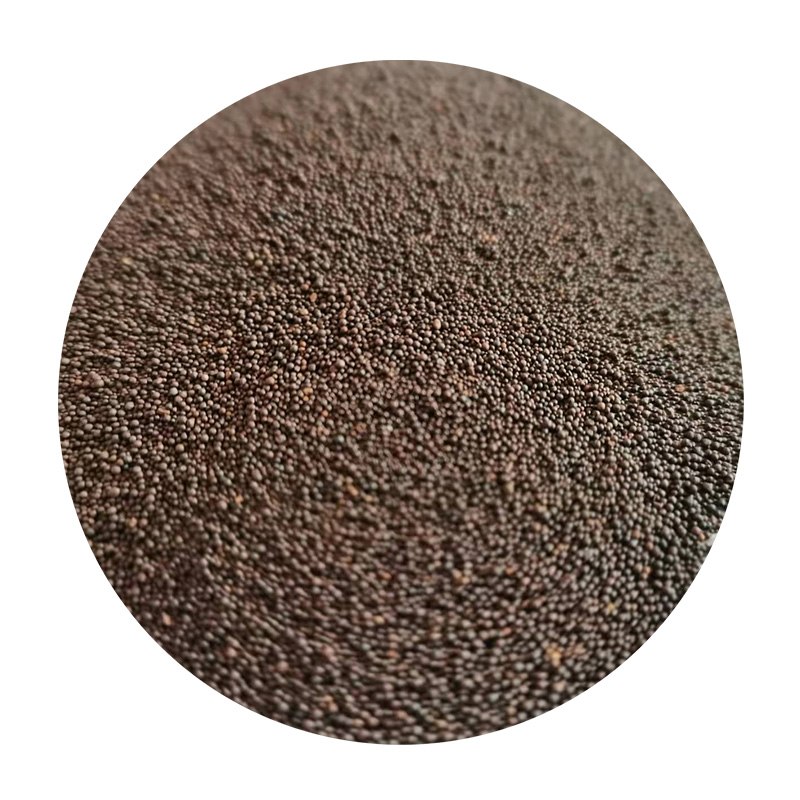
sand casting 101. Once the metal has cooled and solidified, the mold is broken open, and the casting is removed. Sand casting is preferred for its versatility and cost-effectiveness. It can be used to produce both small and large parts, and the tooling costs are relatively low compared to other casting methods. Sand casting also allows for the production of complex shapes and designs that would be difficult to achieve with other methods. However, there are some limitations to sand casting. The surface finish of sand castings is not as smooth as other casting methods, and there may be some porosity in the final part. Additionally, sand casting is not suitable for high precision parts as the tolerances may not be as tight. In conclusion, sand casting is a versatile and cost-effective method of metal casting that is widely used in various industries. While it may not be suitable for all applications, it is a reliable and proven method for producing complex metal parts. With the right design and process controls, sand casting can be a highly effective solution for many manufacturing needs. Post time:Jul . 11, 2024 02:41
Next:Resin coated fracturing sand enhances well productivity and efficiency in oil extraction operations.