Sand Casting An Overview of a Traditional Manufacturing Process
Sand casting, also known as sand mold casting, is one of the oldest and most widely used metal casting processes. It involves creating a mold from sand and then pouring molten metal into that mold to produce a solid object. This method, which dates back over 5,000 years, is favored for its versatility, cost-effectiveness, and ability to create complex shapes with excellent dimensional accuracy.
The Sand Casting Process
The sand casting process begins with the creation of a mold. The first step is to produce a pattern that reflects the object to be cast. Generally made from metal or plastic, the pattern is a replica of the final product. Once the pattern is ready, it is placed inside a flask, a sturdy frame that holds the sand. The space around the pattern is filled with a mixture of sand, clay, and water, which serves as a binder to hold the sand grains together.
After the mold is packed tightly around the pattern, the next step is to remove the pattern, leaving a cavity in the shape of the intended object. This cavity is where the molten metal will be poured. Two halves of the mold (the cope and the drag) are usually created, allowing for easy assembly and disassembly. Additional features such as sprues and risers are added to facilitate the flow of molten metal and allow trapped gases to escape.
Once the mold is prepared, it is heated and subjected to a quality check for any possible defects. After ensuring that the mold is ready, molten metal (usually aluminum, iron, or steel) is poured into the mold cavity. The metal needs to be heated to a temperature specific to the alloy being used, making careful temperature control critical at this stage.
After the metal has cooled and solidified, the mold is broken open, and the casting is removed. It is then cleaned of any sand particles and excess material, often requiring additional processes such as machining or polishing to achieve the desired finish.
Advantages of Sand Casting
describe sand casting
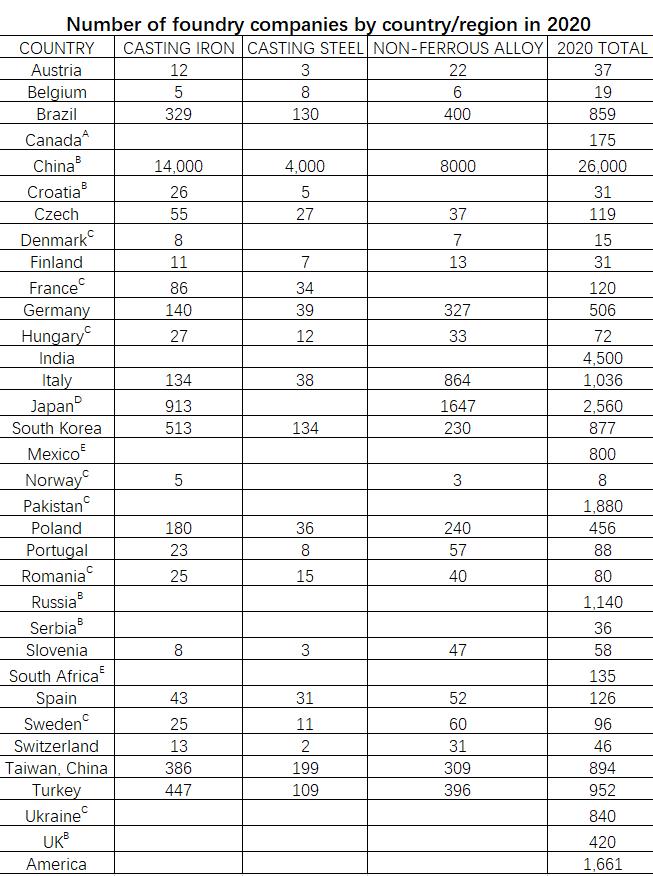
One of the primary advantages of sand casting is its flexibility in terms of the types of metals used. Nearly all metals can be cast using this method, making it suitable for various industries, including automotive, aerospace, and art. Additionally, the low cost of sand and the ability to reuse sand for multiple casts make sand casting an economically friendly choice.
Another benefit is the process's ability to produce large components. Unlike other casting methods that might be limited in size, sand casting can accommodate significant objects, making it the preferred choice for heavy industrial parts, machinery housings, and large sculptures.
Limitations and Challenges
Despite its many advantages, sand casting is not without its challenges. The surface finish of sand-cast products is typically rough compared to those produced by other methods. This often necessitates post-casting processes to achieve a smoother finish. Additionally, since the molds are made of sand, they are not reusable for high-volume production, which can limit efficiency in mass manufacturing applications.
Moreover, the complexity of the molds can affect production time. Designing intricate patterns and ensuring accurate mold assembly require skilled labor and adequate time, which can lead to higher costs in some cases.
Conclusion
Sand casting remains a fundamental technique in the casting industry, praised for its versatility and cost-effectiveness. While there are challenges associated with the process, its ability to mold various materials into complex shapes makes it an invaluable asset in manufacturing across multiple sectors. As technology continues to advance, the integration of new materials and methods will likely enhance the efficiency and efficacy of sand casting, maintaining its relevance in modern production.
Post time:Aug . 09, 2024 17:20
Next:Exploring the Properties and Applications of Sintered Sand in Advanced Material Manufacturing