Sand Casting 101 An Introduction to an Age-Old Art
Sand casting is one of the oldest and most versatile metal casting processes. Its simplicity, cost-effectiveness, and ability to produce complex shapes make it a popular choice in various industries, ranging from automotive to aerospace. Understanding the fundamentals of sand casting can provide insights into its widespread application and significance in manufacturing.
What is Sand Casting?
At its core, sand casting involves creating a mold from a sand mixture, pouring metal into this mold, and allowing it to solidify to form a desired shape. The process begins with the preparation of a sand mold, which consists of two halves the cope (the top half) and the drag (the bottom half). The mixture typically consists of sand, a bonding agent (usually clay), and water, allowing it to retain shape.
The Sand Casting Process
1. Pattern Making The first step is to create a pattern that represents the desired final product. Patterns can be made from various materials, including wood, metal, or plastic, and they are usually larger than the final casting to account for shrinkage during cooling.
2. Mold Creation The pattern is then used to create a sand mold. The pattern is pressed into the sand mixture, creating a cavity that represents the part's shape. Once both halves of the mold are created, they are joined together, ensuring proper alignment.
3. Pouring the Metal Molten metal is prepared and poured into the mold cavity. The temperature of the metal can reach up to 1600°C (2912°F) or more, depending on the type of metal being used. The design of the mold must include gating systems and vents to allow air to escape and ensure the smooth flow of the molten metal.
sand casting 101
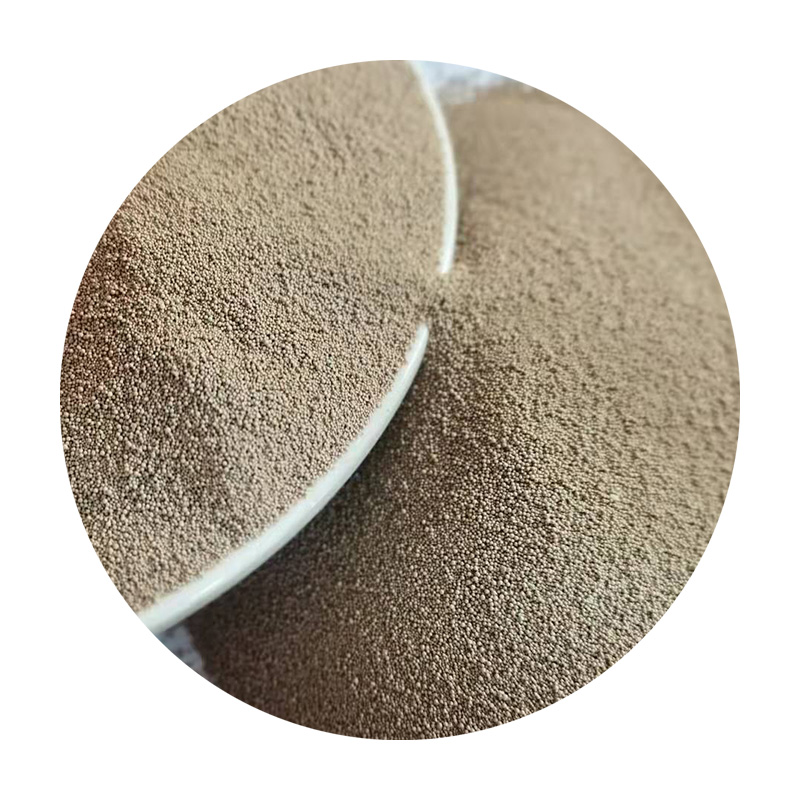
4. Cooling and Solidification After the metal is poured, it takes some time to cool and solidify. This time can vary based on the size of the casting and the type of metal. Once solidified, the mold is broken apart to reveal the casting.
5. Finishing The final step involves removing any excess material (known as flashing) and performing secondary operations, such as machining or surface treatment, to achieve the desired finish and tolerance levels.
Advantages of Sand Casting
One of the primary advantages of sand casting is its flexibility. It can accommodate a wide range of metals, including ferrous and non-ferrous alloys. The process allows for the production of large and complex geometries that may be difficult or impossible to achieve with other casting methods. Additionally, sand molds are relatively inexpensive to produce and can be reused, making the process cost-effective for large production runs or one-off prototypes.
Another significant benefit is the ability to cast large components. Many industries rely on sand casting for producing parts such as engine blocks, frames, and other structural components that require durability and precision.
Challenges in Sand Casting
Despite its many benefits, sand casting is not without challenges. The surface finish of sand-cast components may not be as smooth as those produced by other methods, and achieving tight tolerances can be difficult. Additionally, the strength of the sand mold can be a limiting factor in very intricate designs.
In conclusion, sand casting remains a fundamental manufacturing process with a rich history and a promising future. Its ability to create complex shapes, accommodate various materials, and remain economically viable makes it a critical technique in modern manufacturing. Whether you are a seasoned engineer or a newcomer to the casting world, understanding the basics of sand casting can greatly enhance your appreciation of this enduring art.
Post time:Aug . 16, 2024 14:36
Next:Cast of the Sandcastle Project Unveiled with Exciting New Faces