Understanding Sand Casting A Time-Honored Metal Forming Technique
Sand casting, also known as sand molded casting, is one of the oldest and most versatile metal casting processes used throughout the world. This technique has stood the test of time and continues to play a vital role in various industries, from automotive to aerospace. The fundamental principle involves pouring molten metal into a mould made of sand, which is then allowed to solidify, creating a solid metal component.
The Sand Casting Process
The sand casting process can be broken down into several key steps pattern making, molding, pouring, cooling, and finishing.
1. Pattern Making The first step in sand casting involves creating a pattern, which is essentially a replica of the final product. Patterns can be made from a variety of materials, including wood, metal, or plastic, and are designed to be slightly larger than the desired product due to the shrinkage that occurs when the metal cools.
2. Molding Once the pattern is ready, it is placed in a molding box, and sand mixed with a binding agent is packed around it to create a mould. The sand must be compacted thoroughly to capture all the details of the pattern. After the sand has set, the pattern is removed, leaving a cavity in the shape of the desired part.
3. Pouring With the mould prepared, the next step is to melt the metal and pour it into the cavity. This is usually done in a furnace where the metal is heated to its melting point. Once the metal is liquefied, it is carefully poured into the mould, ensuring that it fills all areas of the cavity to prevent defects.
sand casting description
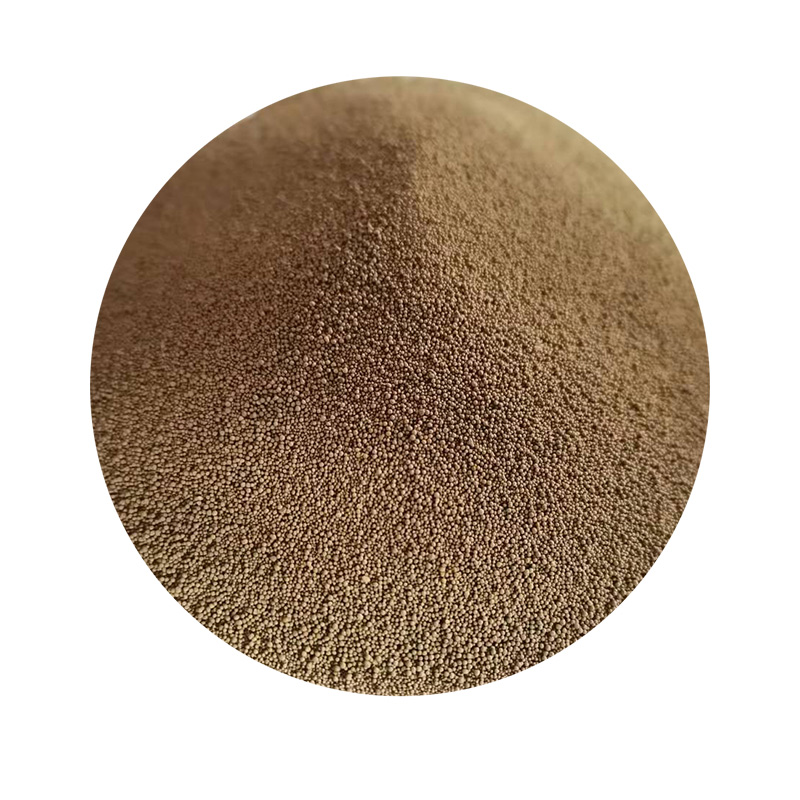
4. Cooling After the molten metal has been poured, it is allowed to cool and solidify. The cooling time varies depending on the size and thickness of the casting. Once cooled, the sand mould is broken apart to retrieve the solid metal component.
5. Finishing Finally, the casting will often require some finishing processes such as sandblasting, machining, or grinding to achieve the desired surface quality and dimensional accuracy. This step is essential to remove any irregularities and ensure that the part meets the required specifications.
Advantages of Sand Casting
One of the most significant advantages of sand casting is its adaptability to a wide range of metal alloys, including iron, aluminum, and bronze. This flexibility allows for the production of complex shapes and sizes, making sand casting suitable for both small and large components.
Additionally, sand casting is cost-effective for low to medium production runs, as the moulds can be reused multiple times. The materials required for sand casting, primarily sand, are readily available and inexpensive, further reducing production costs.
Conclusion
Despite the advent of modern manufacturing techniques, sand casting remains a crucial method for producing metal components. Its simplicity and effectiveness contribute to its lasting popularity in various sectors. As industries continue to evolve, sand casting is likely to adapt and thrive, ensuring its place in the future of manufacturing. Whether producing intricate components for machinery or large-scale structures, sand casting showcases the perfect blend of tradition and innovation in metalworking.
Post time:Aug . 07, 2024 04:40
Next:Exploring the Richness of Gold Sands and Their Impact on Coastal Ecosystems and Local Economies