Affordable Sand Casting A Cost-Effective Solution for Metal Parts
Sand casting, one of the oldest sand-casting techniques, continues to be a popular method for producing metal parts with complex shapes. Whether you are a small workshop, a startup, or an established manufacturer, understanding how to leverage cheap sand casting can significantly enhance your productivity and reduce costs. This article explores the benefits, processes, and considerations involved in affordable sand casting.
What is Sand Casting?
Sand casting is a process that involves creating a mold from a sand mixture and then pouring molten metal into this mold to create a metal part. The mold is typically made from silica sand mixed with a binder like clay to help it hold shape. After the metal cools and hardens, the sand mold is broken away, revealing the cast part. This technique is versatile and can be used for a wide range of metal alloys, including aluminum, bronze, and iron.
Benefits of Cheap Sand Casting
1. Cost-Effectiveness The primary advantage of sand casting is its low cost. The raw materials, including sand and binder, are inexpensive, and the process does not require the expensive tooling needed for methods like injection molding. This makes sand casting particularly appealing for low-volume production runs, prototypes, and custom parts.
2. Flexibility Sand casting is highly adaptable. It can accommodate a variety of part sizes, from small components to large, intricate designs. Additionally, the casting process allows for easy modifications to designs without significant upfront costs, making it ideal for research and development scenarios.
3. Complex Geometries Unlike some other casting processes, sand casting can produce parts with complex geometries and intricate details. This is particularly useful in industries such as automotive and aerospace, where components often have elaborate shapes.
4. Short Lead Times The sand casting process typically has shorter lead times compared to other manufacturing methods. Once the mold is created, multiple parts can be produced quickly, making it an efficient choice for projects with tight deadlines.
The Sand Casting Process
The cheap sand casting process generally involves several stages
cheap sand casting
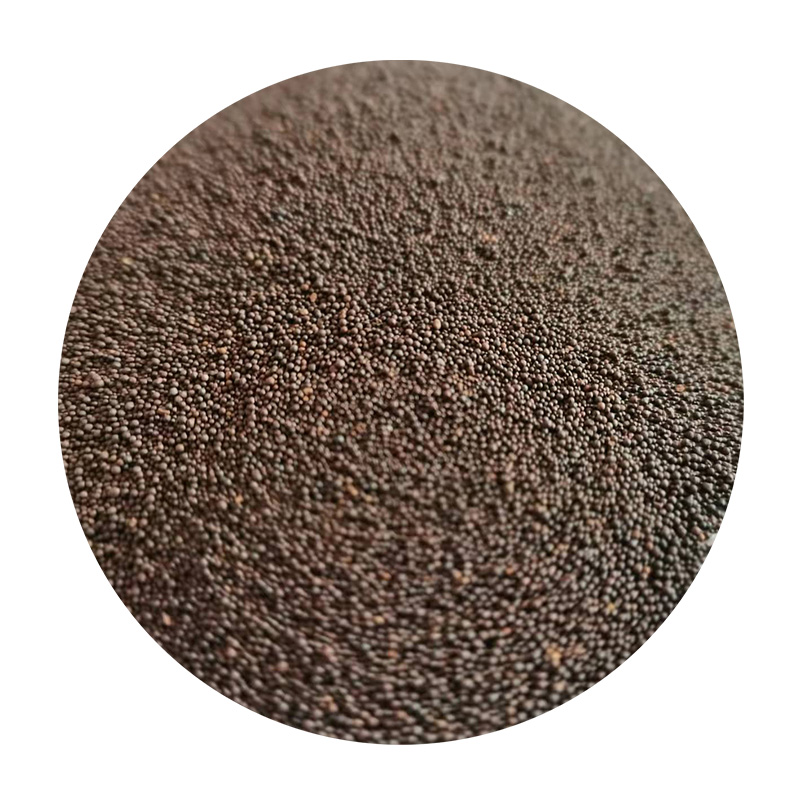
1. Pattern Making A pattern is created to form the mold. Patterns can be made from various materials like wood, metal, or plastic, depending on the production volume and desired surface finish.
2. Mold Preparation The pattern is placed in a sand mixture to form the mold. The sand is compacted around the pattern, and once it is set, the pattern is removed, leaving a hollow mold.
3. Pouring Molten metal is poured into the mold cavity through a gating system. This needs to be done carefully to avoid defects like air pockets or incomplete fills.
4. Cooling and Finishing After the metal cools and solidifies, the sand mold is broken away, revealing the cast part. Any excess material or imperfections are trimmed, and the part is finished as necessary.
Considerations for Using Sand Casting
While sand casting offers many advantages, there are some considerations to keep in mind
- Surface Finish Parts produced through sand casting may have a rougher surface finish compared to other methods. Additional machining may be necessary to achieve the desired quality.
- Material Limitations Certain metals may not be suitable for sand casting, especially those that require precise tolerances and surface finishes.
- Labor-Intensive The process can be labor-intensive, especially for larger productions. Effective training and experience of the workforce are essential for maintaining quality.
Conclusion
Cheap sand casting is a powerful option for manufacturers looking to create high-quality metal parts efficiently and cost-effectively. Understanding its process, benefits, and limitations can help businesses optimize their manufacturing strategies and cater to a wide range of industries. With the right approach, sand casting can pave the way for innovation and creativity in metal production.
Post time:Aug . 11, 2024 08:52
Next:Exploring the Properties and Applications of Sintered Sand in Modern Manufacturing Techniques