Advantages and Disadvantages of Sand Casting Process
Sand casting is one of the oldest and most widely used metal casting processes, where molten metal is poured into a sand mold to create a desired shape. This method has been employed in various industries due to its unique properties and capabilities. However, like any manufacturing process, sand casting comes with its own set of advantages and disadvantages.
Advantages of Sand Casting
1. Cost-Effectiveness One of the primary advantages of sand casting is its cost-effectiveness. The materials used, such as sand and metal, are relatively inexpensive, making it a suitable choice for producing large volumes of metal parts without extensive investment.
2. Versatility Sand casting can be used for a wide range of metals, including iron, aluminum, bronze, and brass. This versatility allows it to cater to various applications, from automotive components to intricate machine parts.
3. Complex Geometries The sand casting process can produce complex shapes and intricate details, which may not be achievable through other casting methods. As a result, it is ideal for creating intricate designs that would be challenging to manufacture otherwise.
4. Scalability Sand casting can be easily scaled for both small and large production runs. Whether producing a single custom part or high volumes of a standard component, sand casting adapts well to different production needs.
advantages and disadvantages of sand casting process
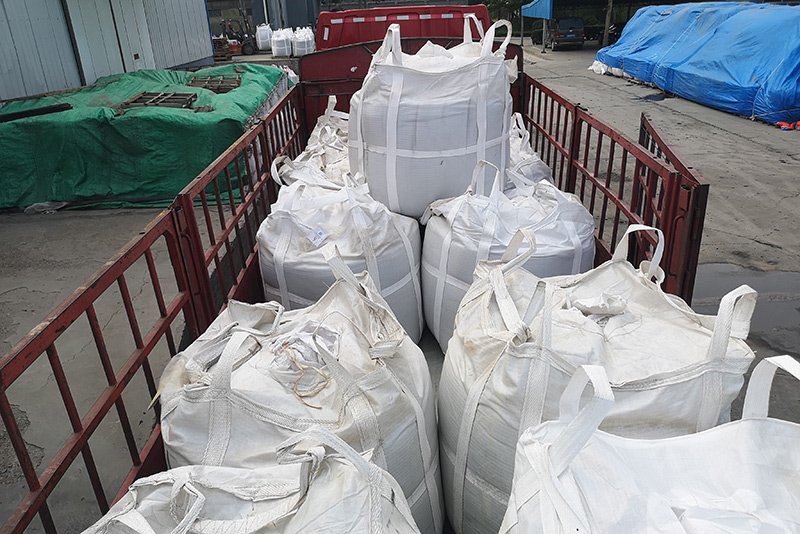
Disadvantages of Sand Casting
1. Surface Finish While sand casting can achieve complex shapes, the surface finish tends to be rougher compared to other processes like investment casting or die casting. This limitation often requires additional machining or finishing processes to achieve the desired surface quality.
2. Dimensional Tolerance The dimensional tolerances achievable with sand casting are generally not as tight as those possible with other casting methods. This can be a drawback when precise dimensions are critical for part functionality.
3. Labor-Intensive The sand casting process often requires a significant amount of manual labor, particularly during the mold-making phase. This can increase production time and labor costs.
4. Environmental Concerns The use of sand as a mold material raises environmental concerns, as the disposal of used sand can lead to waste management issues. Additionally, the emissions from metal casting can have adverse effects on the environment if not properly managed.
5. Limitations in Production Speed Compared to other casting methods, sand casting may be slower, particularly for high-volume production. The time-consuming process of creating molds and cooling times for the metal can hinder overall production efficiency.
In conclusion, sand casting remains a popular manufacturing process due to its cost-effectiveness and versatility in producing complex geometries. However, manufacturers must weigh the advantages against the disadvantages, particularly in terms of surface finish, dimensional tolerance, and production efficiency. By understanding these factors, businesses can make informed decisions on when to use sand casting in their production processes.
Post time:Aug . 28, 2024 13:24
Next:การหล่อโฟมที่หายไป - เทคนิคการผลิตที่ทันสมัย