Advantages and Disadvantages of the Sand Casting Process
Sand casting is one of the oldest and most widely used manufacturing processes for metal casting. It involves creating a mold from sand to form a specific shape, which is then filled with molten metal. While sand casting has numerous advantages that make it appealing for various applications, it also has its disadvantages that may impact its suitability for certain projects.
Advantages of Sand Casting
1. Cost-Effectiveness One of the primary advantages of sand casting is its cost-effectiveness. The materials required for molding, such as sand, clay, and water, are relatively inexpensive. This makes sand casting a viable option for both small-scale and large-scale production.
2. Versatility Sand casting is highly versatile and can accommodate a wide range of metals, including aluminum, bronze, and iron. This flexibility allows engineers and manufacturers to create complex shapes and sizes tailored to specific applications.
3. Large Part Capability Sand casting can produce large components that might be difficult or impossible to manufacture using other processes. This characteristic is particularly beneficial in industries such as automotive and aerospace, where large and complex parts are often required.
4. Design Flexibility The process allows for significant design freedom. With sand molds, intricate designs can be achieved, enabling the production of components with complex geometries that would be challenging to manufacture through other casting methods.
5. Short Lead Times The setup time for sand casting is generally shorter compared to other processes. This is because molds can be created relatively quickly, which allows manufacturers to respond faster to market demands and changes in design.
advantages and disadvantages of sand casting process
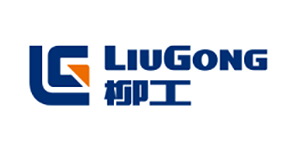
Disadvantages of Sand Casting
1. Surface Finish One of the main drawbacks of sand casting is that it often results in a rough surface finish compared to other casting methods, such as investment casting. Additional machining may be required to achieve a smoother surface, which can increase production time and costs.
2. Dimensional Tolerances Sand casting typically has lower dimensional accuracy and tighter tolerances compared to more advanced casting techniques. This can be a limitation for projects that require high precision.
3. Environmental Concerns The sand casting process can pose environmental concerns, as it may generate dust and waste materials that need proper management. Moreover, the use of chemical binders in sand can also have environmental implications.
4. Labor-Intensive Although the process itself can be quick, sand casting is often labor-intensive, requiring skilled workers for mold preparation and metal pouring. This can increase labor costs and result in a dependence on skilled labor.
5. Limited Production Rate While sand casting is suitable for low to medium production runs, it may not be the best option for high-volume production due to the slower mold preparation and cooling times involved.
In conclusion, sand casting remains a popular choice in the manufacturing industry due to its cost-effectiveness, versatility, and ability to produce large and complex shapes. However, manufacturers must also consider its limitations, such as surface finish quality and environmental impacts, when deciding whether to employ this casting process for their specific needs. Balancing these advantages and disadvantages is essential for optimizing production methods in various manufacturing applications.
Post time:Aug . 29, 2024 06:41
Next:Innovative 3D Sand Printing Solutions for Custom Manufacturing