Foundry Sand Contamination Causes, Effects, and Mitigation Strategies
The foundry industry plays a crucial role in manufacturing various metal products, ranging from automotive parts to industrial machinery. Central to this process is the use of foundry sand, a key material that forms molds for metal casting. However, foundry sand is not immune to contamination, which can significantly affect product quality and operational efficiency. This article explores the causes, effects, and potential remediation strategies for foundry sand contamination.
Causes of Contamination
Foundry sand contamination can arise from several sources. One primary cause is the recycling of used sand. As sand is reused in multiple casting cycles, it can accumulate impurities such as metal residues, organic matter, and dust. Contaminated sand can lead to defects in the final product, such as surface imperfections or structural weaknesses.
Additionally, the introduction of foreign materials during the handling and storage processes can also lead to contamination. Dust and debris from the surrounding environment, as well as improper storage methods, can compromise the purity of the sand. Chemical additives used to enhance the properties of the sand can also react with other materials, leading to further contamination.
Effects of Contamination
The impacts of foundry sand contamination can be far-reaching
. Firstly, the presence of impurities can significantly impair the mechanical properties of cast products, leading to issues such as brittleness or decreased tensile strength. This not only affects product performance but can also result in costly recalls and reputational damage for manufacturers.Moreover, contaminated sand can lead to increased wear and tear on machinery, as impurities can interfere with the casting process and lead to defects. This can elevate operational costs due to the need for more frequent maintenance and repairs. Ineffectively managed foundry sand contamination can also lead to environmental issues, as improperly disposed of contaminated materials can pollute surrounding ecosystems.
foundry sand contamination
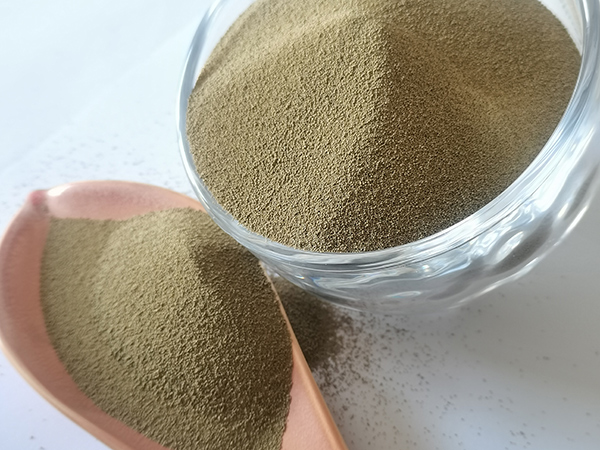
Mitigation Strategies
To combat the challenges posed by foundry sand contamination, several mitigation strategies can be implemented. The first step involves thorough quality control procedures to ensure the cleanliness of foundry sand. Regular inspection and testing can help identify contaminants early in the process, allowing for timely remediation.
Furthermore, adopting advanced sand management techniques, such as sand reclamation systems, can significantly reduce the level of contamination. These systems can effectively separate impurities from used sand, allowing it to be reused with minimal impact on product quality.
Education and training for workers on proper handling and storage practices can also mitigate contamination risks. Ensuring that staff understands the importance of maintaining the integrity of foundry sand can lead to better practices and reduced contamination rates.
Another crucial aspect is the transition to more environmentally-friendly materials and additives that may pose less risk of contamination. By incorporating synthetic or modified sands, foundries can reduce reliance on traditional materials, thus limiting the sources of potential contamination.
Conclusion
Foundry sand contamination presents significant challenges to the foundry industry, resulting in product defects, increased costs, and environmental concerns. However, with proactive measures such as rigorous quality control, advanced sand management systems, and employee training, the risks associated with contamination can be effectively mitigated. As the industry continues to evolve, adopting innovative solutions will be key to ensuring high-quality products and sustainable operational practices.
Post time:Aug . 14, 2024 14:11
Next:Exploring the Techniques and Benefits of Sand Casting in China's Manufacturing Industry