How Sand Casting is Done
Sand casting is one of the oldest and most versatile metal casting processes utilized in the manufacturing industry. It involves creating a mold for molten metal to cool and solidify into a desired shape. The process is distinguished by its use of sand as the primary molding material, making it both cost-effective and efficient for producing complex geometries. This article will outline the steps involved in sand casting, along with its advantages and applications.
Step 1 Pattern Making
The first step in the sand casting process is the creation of a pattern, which is a replica of the final product. Patterns can be made from various materials such as wood, metal, or plastic and are designed slightly larger than the desired final dimensions of the casting. This allows for shrinkage that occurs as the metal cools. The pattern also includes additional features, such as risers and gates, which facilitate the flow of molten metal into the mold.
Step 2 Preparing the Mold
Once the pattern is complete, it's time to create the mold. The most commonly used material for sand molds is a mixture of sand and a binder, typically clay, which enhances the cohesiveness of the sand grains. To prepare the mold, the sand mixture is packed tightly around the pattern, ensuring it captures all the details. The packing can be done by hand or with the aid of machinery, depending on the size and complexity of the mold. After the mold is formed, the pattern is removed, leaving a cavity that will hold the molten metal.
Step 3 Pouring the Metal
With the mold prepared, the next step is to melt the metal that will fill the cavity. Common metals used in sand casting include aluminum, brass, and iron due to their favorable melting points and properties. The molten metal is carefully poured into the mold through the gating system. It is essential to monitor the temperature during this process to ensure that the metal flows properly and fills all parts of the mold without causing defects.
Step 4 Cooling and Solidification
how sand casting is done
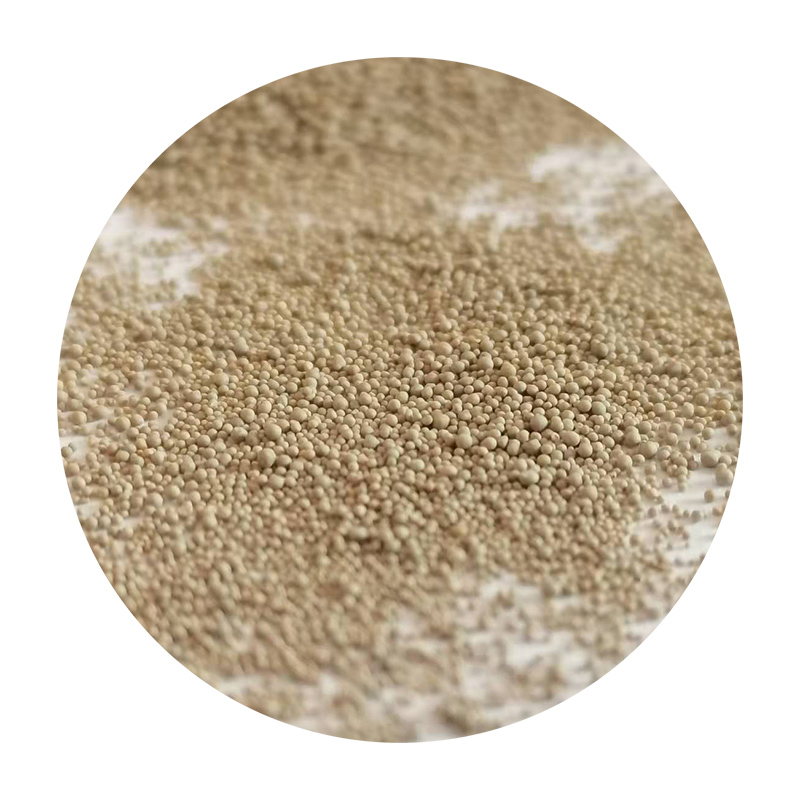
Once the molten metal is poured into the mold, it begins to cool and solidify. This cooling time can vary based on the type of metal, the thickness of the casting, and environmental conditions. After a sufficient amount of time has passed, the mold is typically broken open to reveal the cast item. The sand mold can be reused multiple times, provided it remains intact.
Step 5 Finishing Operations
After the metal has cooled and solidified, the casting often requires some finishing operations. This can include sandblasting to remove any sand particles, grinding to smooth out the surfaces, or machining to achieve precise dimensions. These post-processing steps are crucial for ensuring the final product meets the desired specifications, particularly in applications where tight tolerances are crucial.
Advantages of Sand Casting
Sand casting is favored for several reasons. Its ability to produce complex geometries with internal features is unmatched by many other casting processes. Additionally, the method is economical, especially for low to medium production runs. The flexibility in materials and the ability to create large parts make it suitable for a wide array of applications, from automotive components to artistic sculptures.
Applications
Industries that commonly utilize sand casting include automotive, aerospace, and construction, highlighting its relevance in various sectors. The versatility and cost-effectiveness of sand casting ensure its continued importance in manufacturing, catering to both mass production and custom requirements.
In conclusion, sand casting remains a pivotal method in the field of metalworking. Its simple yet effective process allows for the creation of intricate designs while maintaining affordability and efficiency. As technology advances, sand casting processes continue to evolve, enhancing production capabilities and expanding its applications across different industries.
Post time:Jul . 28, 2024 15:07
Next:Different Varieties of Sand Utilized in the Sand Casting Process for Metal Fabrication