How to Sand Cast A Comprehensive Guide
Sand casting, a metal casting process characterized by the use of sand as the mold material, has been employed for centuries in various industries, from automotive to art. Its popularity stems from its versatility, cost-effectiveness, and the ability to produce complex shapes. This article will guide you through the steps of sand casting, providing insight into techniques, materials, and best practices.
Materials Needed
Before diving into the sand casting process, gather the necessary materials 1. Pattern This is an exact replica of the object you wish to cast, typically made from wood, metal, or plastic. 2. Sand The primary mold material, usually a mixture of silica sand, clay, and water to enhance its binding properties. 3. Binder Bentonite clay is often used as a binder to hold the sand grains together. 4. Release Agent This helps prevent the pattern from sticking to the sand mold. 5. Metal The material you will be casting, commonly aluminum, bronze, or iron. 6. Furnace To melt the metal before pouring it into the mold. 7. Tools Additional tools may include a riddle, trowel, and safety gear like gloves and goggles.
Step-by-Step Process
1. Creating the Pattern Begin by designing and crafting a pattern of your desired object. The pattern should be slightly larger than the final product due to metal shrinkage during cooling. Smooth and polish the pattern to achieve a clean surface finish.
How to Sand Cast A Comprehensive Guide
3. Molding Begin by applying a release agent to the pattern to facilitate easy removal. Place the pattern in a flask (a container for the sand) and pack damp sand around it, ensuring that it’s densely packed. Carefully remove the pattern after the sand has been compacted to form a cavity.
how to sand cast
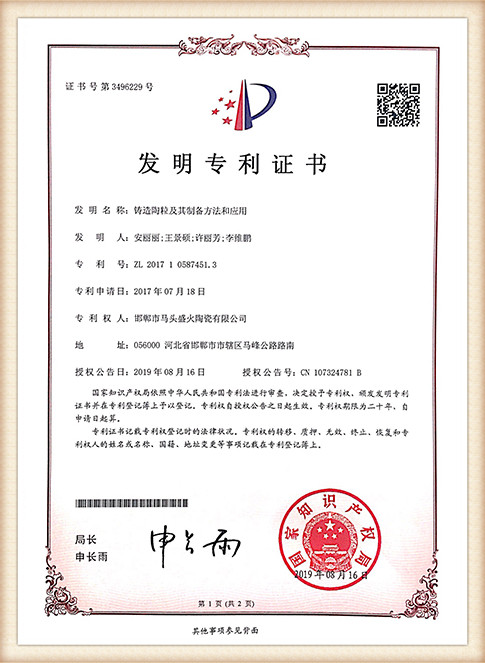
4. Creating the Runner and Sprue Introduce a runner (a channel for the molten metal) and a sprue (the entry point) in the sand mold. These should be strategically placed to ensure the metal flows evenly and fills all areas of the mold.
5. Melting the Metal Using a furnace, melt your selected metal to the appropriate temperature. Always follow safety protocols during this step, using protective gear to prevent injuries from the heat or molten metal.
6. Pouring the Metal Once the metal is molten, carefully pour it into the sprue, ensuring a continuous flow to avoid air pockets. Allow it to flow into all areas of the mold until completely filled.
7. Cooling Let the mold cool for the appropriate amount of time. The cooling time will depend on the metal being cast and the thickness of the mold. It's essential not to rush this process; premature removal can lead to defects.
8. Breaking Out the Casting After the mold is cool, gently break it apart to reveal your cast object. Use a hammer or chisel if necessary, but take care not to damage the casting.
9. Finishing Touches Finally, clean any residual sand from the casting. You may need to use grinding or filing tools to finish edges, remove imperfections, and achieve the desired surface finish.
Conclusion
Sand casting is an accessible and effective way to create metal parts with intricate designs. With the right materials and techniques, both amateur and professional metalworkers can produce high-quality castings. By following this guide, you can embark on your sand casting journey and explore the endless possibilities this age-old technique has to offer. Always remember to prioritize safety and take your time to perfect your craft!
Post time:Aug . 06, 2024 13:11
Next:Exploring the Innovations and Trends in Sand Casting Industries for Future Manufacturing Solutions