How to Make Foundry Sand
Foundry sand is a critical ingredient in the metal casting process, serving as a mold material for shaping metals into various forms. It provides a perfect balance of durability, heat resistance, and fine grain quality needed for efficient casting. To understand how to make foundry sand, it’s essential to explore its components, preparation process, and applications.
Understanding Foundry Sand
Foundry sand is typically composed of silica, clay, and water. Silica sand, derived from quartz, is the primary component due to its high melting point and thermal stability. Clay is used to bind the sand grains together, while water helps in maintaining the appropriate moisture level for creating molds. Some foundries also employ additives to enhance specific properties such as strength and permeability.
Step 1 Selecting the Right Sand
The first step in making foundry sand is selecting high-quality silica sand. The ideal sand grains should be round, well-graded, and free of impurities. The grain size significantly affects the final mold quality; fine sand provides excellent detail, while coarser sand offers better strength. Manufacturers often test the sand for its grain size distribution using a sieve analysis to ensure consistency with foundry requirements.
Step 2 Adding Clay
After selecting the sand, the next step is to incorporate clay. Bentonite clay is commonly used due to its exceptional binding properties. Typically, a mixture containing 5% to 10% clay by weight is added to the sand. The clay enhances the sand’s plasticity, allowing it to retain the mold shape better during the metal pouring process.
To mix the clay with the sand effectively, it is advisable to add water gradually, ensuring a homogeneous mixture. The moisture content is crucial, as too much water can lead to mold defects like swelling, while too little can cause the mold to crack.
Step 3 Incorporating Additional Additives
how to make foundry sand
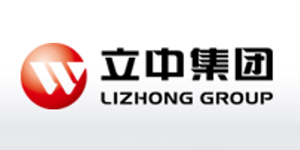
Depending on the specific casting requirements, other additives may be incorporated into the sand mixture. Common additives include
- Coal Dust Improves the sand's thermal stability and helps to reduce oxidation during pouring. - Resins Serve as binders, enhancing mold strength and reducing the need for moisture. - Other Clays Different types of clay may be mixed to achieve desired properties like heat resistance and flexibility.
These additives should be mixed thoroughly to ensure even distribution throughout the sand mixture.
Step 4 Conditioning the Sand
Once the sand, clay, water, and any additives are combined, the mixture must be conditioned. This process involves mixing the sand in a sand muller or mixer to ensure uniformity and develop the desired properties. Conditioning helps to improve the sand's cohesion and allows for optimal mold formation.
Step 5 Testing the Foundry Sand
Before using the sand for casting, it’s vital to conduct a series of tests to confirm its suitability for the intended application. Common tests include checking the green strength (the sand's ability to maintain shape when moist), permeability (the ability to allow gases to escape), and collapse strength (the ability to withstand the weight of molten metal).
Conclusion
Making foundry sand is an intricate process requiring attention to detail at each step. From the selection of high-quality silica to the careful mixing of clay and additives, each phase contributes to the performance of the sand in casting operations. Properly prepared foundry sand not only ensures the production of high-quality metal components but also enhances the overall efficiency of the foundry. As industries evolve, mastering the art of creating the perfect foundry sand will remain essential for effective metal casting.
Post time:Aug . 04, 2024 02:41
Next:Exploring Different Types of Foundry Sands for Enhanced Casting Performance and Quality