3D Printing Patterns for Sand Casting
In recent years, the industrial landscape has been revolutionized by the advent of 3D printing technology, and its application in sand casting has garnered particular attention. Sand casting, a traditional manufacturing process, involves the creation of metal parts by pouring molten metal into a mold made of sand. However, the introduction of 3D printing has transformed this age-old technique, offering numerous advantages that enhance both efficiency and quality.
The primary benefit of using 3D printing to create patterns for sand casting lies in the ability to produce complex geometries that were once challenging or even impossible to achieve with conventional methods. Traditional pattern-making often requires extensive design modifications to accommodate milling, but with 3D printing, intricate designs with undercuts and intricate details can be directly printed. This not only boosts creativity but also reduces material waste, as designers can produce exactly what they envision without the need for excessive modifications.
Moreover, 3D printing allows for rapid prototyping, significantly shortening the lead time from design to production. In traditional sand casting, creating patterns can be time-consuming, involving machining various components and assembling them into a mold. In contrast, a 3D printer can create a complete pattern in days, or even hours, allowing manufacturers to respond swiftly to market demands and changes in design specifications. This agility is particularly valuable in industries such as aerospace and automotive, where the ability to test and refine parts quickly can provide a competitive edge.
3d printing patterns for sand casting
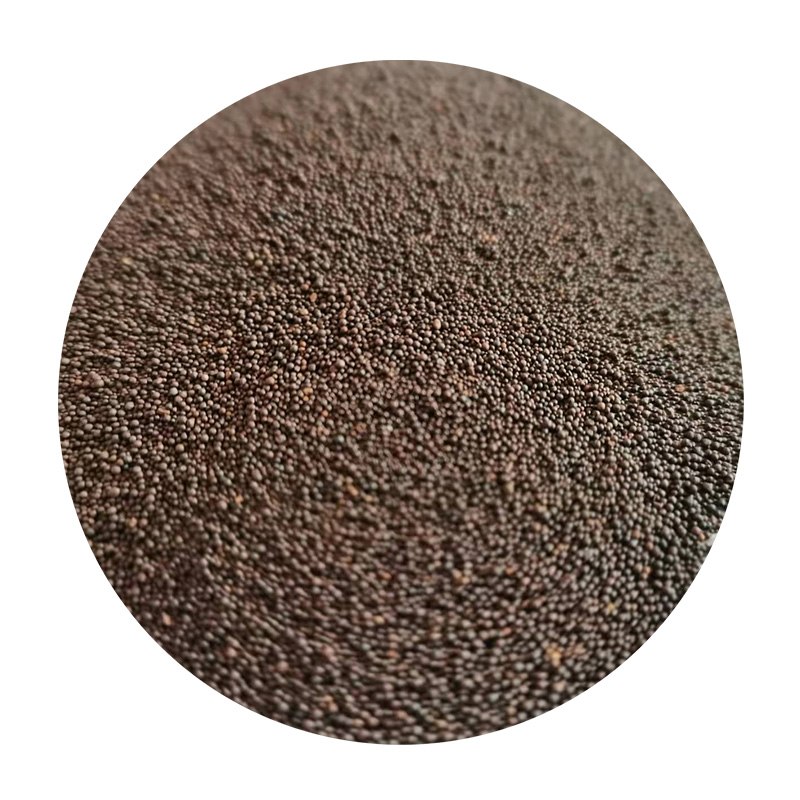
Another noteworthy advantage is the reduction of costs associated with pattern production. While the initial investment in 3D printing technology can be substantial, the overall cost per part can be lower than conventional methods when considering the elimination of tooling costs, reduced labor, and minimized scrap material. This makes 3D printing a financially appealing option, especially for small to medium-sized production runs where traditional methods may not be cost-effective.
Additionally, 3D printing offers the potential for on-demand production. By printing patterns as needed, companies can minimize inventory costs and storage space. This flexibility supports just-in-time manufacturing practices, aligning with modern supply chain strategies that prioritize efficiency.
However, it is important to note that the integration of 3D printing into sand casting processes is not without challenges. Material selection for printing patterns is critical, as the material must withstand the heat and pressure of the casting process. Furthermore, post-processing and surface finish requirements must be addressed to ensure that the final cast product meets quality standards.
In conclusion, the application of 3D printing for producing patterns in sand casting represents a significant advancement in manufacturing technology. By enabling complex designs, reducing lead times, lowering costs, and supporting on-demand production, 3D printing has the potential to enhance the efficiency and quality of sand casting operations. As technology continues to evolve, we can expect even greater innovations that will shape the future of metal casting and manufacturing as a whole.
Post time:Aug . 28, 2024 02:03
Next:Super Sand Bond G2 - Den beste løsningen for slitesterk forsegling