The Evolution of Sand Casting Through 3D Printing Technology
The world of manufacturing is undergoing a significant transformation, and one of the most intriguing developments is the integration of 3D printing technology into traditional sand casting processes. Sand casting has been a staple in metalworking for centuries, providing a reliable method for creating complex parts and prototypes. However, the rise of 3D printing has introduced a new level of efficiency, precision, and innovation to this age-old technique.
Sand casting involves creating a mold out of sand that can withstand high temperatures, allowing liquid metal to be poured into it to form a variety of shapes and components. Traditionally, this process requires skilled artisans to painstakingly shape molds by hand or use components made from metal or plastic. Although reliable, these methods can be time-consuming and often lead to high production costs, especially for small batches or specialized designs.
The Evolution of Sand Casting Through 3D Printing Technology
One of the significant advantages of 3D printed sand molds is the reduction in lead time. Traditional sand casting can take days or even weeks, especially when multiple prototypes are necessary. With 3D printing, manufacturers can quickly iterate on designs, allowing them to test and refine their products faster. This agility is crucial in today’s fast-paced market, where companies must adapt quickly to changing customer demands and preferences.
3d print sand casting
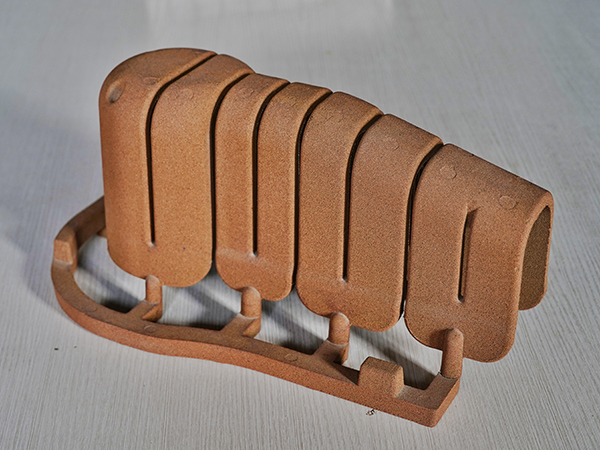
Moreover, the precision offered by 3D printing minimizes the need for post-processing. Because the molds are created with such accuracy, parts can be produced with better surface finishes and tighter tolerances. This reduction in additional machining not only saves time but also significantly lowers costs, particularly in industries where precision is paramount, such as aerospace and automotive.
Another benefit of incorporating 3D printing into sand casting is the potential for material optimization. Manufacturers can use different types of sand or additives to enhance the performance of molds, enabling them to produce parts that are lighter, stronger, or more heat-resistant. This flexibility allows for greater experimentation and innovation in product development.
Furthermore, embracing 3D printing in sand casting promotes sustainability. By reducing waste associated with traditional manufacturing methods, companies can lower their environmental impact. The ability to design molds that perfectly fit the required geometry means less excess material, contributing to a greener manufacturing process.
In conclusion, the integration of 3D printing technology into sand casting represents a significant leap forward in manufacturing. With faster lead times, reduced costs, enhanced precision, and a focus on sustainability, this evolution not only benefits manufacturers but also paves the way for more innovative and efficient production methods. As 3D printing technology continues to advance, we can expect to see even more exciting developments in the world of sand casting, further solidifying its place in modern manufacturing practices.
Post time:Aug . 28, 2024 22:26
Next:How Accurate is Sand Casting? | Understanding Sand Casting Precision