The Importance of Sand Used in Foundry Processes
In the world of manufacturing and metal casting, the choice of materials is crucial to achieving high-quality products. Among these materials, sand is one of the most significant components in foundry operations. It serves as a mold-making substance, shaping metal casts that are integral to various industries, including automotive, aerospace, and construction.
Types of Sand Used in Foundry
The most commonly used sand in foundries is silica sand, which primarily consists of silicon dioxide (SiO2). Its high melting point, chemical stability, and availability make it an ideal choice for casting processes. Silica sand is often treated and processed to enhance its properties, leading to the creation of special sands for specific applications.
Another type of sand used is chromite sand, known for its excellent thermal stability and resistance to metal penetration. This makes it suitable for high-temperature applications where other types of sand might fail. Additionally, olivine sand is preferred for certain castings due to its high melting point and lower thermal expansion properties, giving it a distinct advantage in the production of delicate and complex molds.
The Role of Sand in the Casting Process
The primary role of sand in the foundry lies in its ability to create molds into which molten metal is poured. The sand must possess specific qualities such as grain size, shape, and permeability. Grain size affects the surface finish of the castings; too fine a grain can lead to defects, while too coarse can result in weak molds that do not hold their shape when filled with metal.
Permeability is an essential characteristic, as it allows gases produced during the casting process to escape, preventing defects like blowholes and porosity. A well-balanced mixture of sand with an appropriate binder, often clay, is critical in achieving the right consistency and strength of the mold.
Environmental Considerations
sand used in foundry
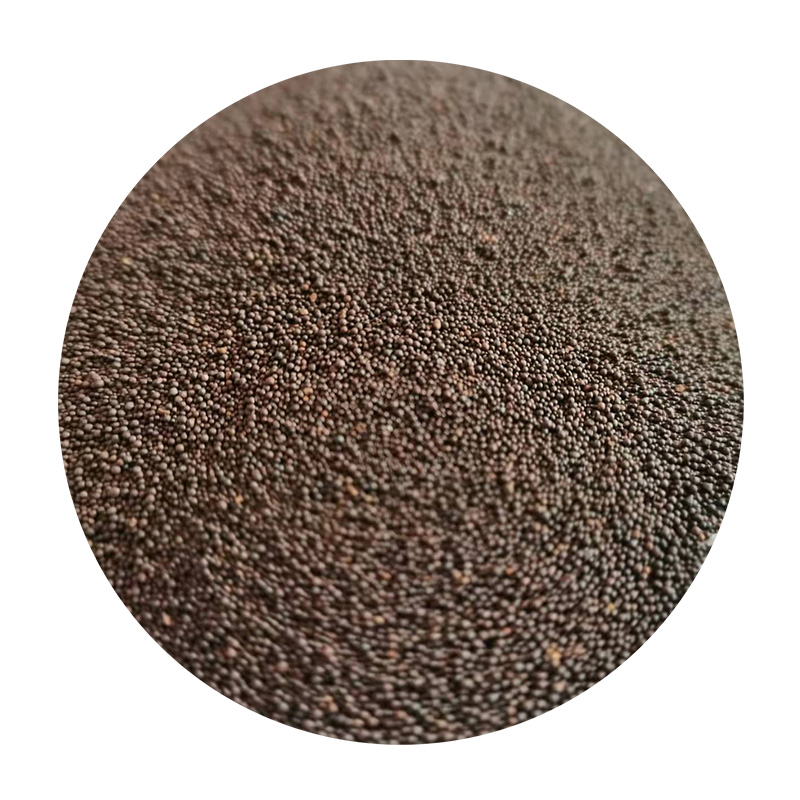
While sand is a natural resource, its extraction and processing can have environmental impacts. Many foundries are now looking for sustainable practices, such as recycling sand from used molds. This not only reduces waste but also minimizes the need for new sand excavation. Moreover, advancements in synthetic sands, which mimic the properties of natural sands but are manufactured from industrial by-products, offer an eco-friendly alternative.
Innovations in Sand Technology
As technology evolves, so does the science of sand in foundries. Innovations such as 3D printing in sand casting are revolutionizing how manufacturers approach mold-making. Instead of traditional methods, 3D printing allows for greater precision and complexity in mold designs. This technology reduces waste and shortens lead times, enabling quicker production cycles.
Furthermore, the development of advanced binders that enhance the binding properties of sand is leading to molds that are more durable and resistant to heat. These new materials are paving the way for more efficient foundry processes and higher quality castings.
Challenges Ahead
Despite the advances in sand technology, foundries face challenges such as rising costs of raw materials and stricter regulations regarding environmental impact. The demand for high-quality products means that foundries must innovate constantly and improve their processes to stay competitive.
Additionally, the fluctuating availability of certain types of sand, especially those tied to specific geographical locations, places pressure on foundry operations. Developing alternative materials or sourcing sustainably from local producers can help mitigate these risks.
Conclusion
In conclusion, sand plays a vital role in foundry operations, impacting the quality, efficiency, and sustainability of metal casting processes. As foundries continue to innovate and adapt to changing market demands, the development and utilization of sand will undoubtedly evolve. The integration of new technologies and sustainable practices will ensure that sand remains a critical component in the future of metal manufacturing. By understanding and improving the properties of sand used in foundries, manufacturers can secure their position in an increasingly competitive industry.
Post time:វិច្ឆិកា . 19, 2024 03:24
Next:Understanding the Process and Benefits of Sand Casting in Metal Fabrication