Sand Used for Sand Casting An In-Depth Analysis
Sand casting, one of the oldest and most versatile manufacturing processes, incorporates the use of sand as the primary molding material. This technique allows for the production of intricate metal components in various shapes and sizes, making it a favored option in industries ranging from automotive to aerospace. Understanding the properties and types of sand used in sand casting is crucial for optimizing the casting process and ensuring high-quality outcomes.
Types of Sand Used in Sand Casting
The most commonly used sand for sand casting is silica sand, which boasts high melting points and excellent thermal stability. Silica sand is primarily composed of silicon dioxide (SiO2), making it suitable for reclaiming and reusing in multiple casting cycles. However, other types of sand, such as olivine sand, zircon sand, and chromite sand, are also utilized based on specific requirements and desired characteristics.
1. Silica Sand This is the most prevalent sand type due to its availability and cost-effectiveness. Silica sand provides excellent durability and strength, enabling it to retain its shape during the casting process. However, its angular grains can sometimes lead to defects in the final product if not handled correctly.
2. Olivine Sand Known for its high refractoriness and resistance to thermal shock, olivine sand is often used for casting ferrous metals. It has a lower thermal expansion than silica sand, which can minimize defects caused by thermal stresses in certain applications.
3. Zircon Sand With a very high melting point and excellent thermal conductivity, zircon sand is ideal for casting high-temperature alloys. Its low thermal expansion and chemical inertness make it suitable for precision molds, although it is more expensive than silica sand.
4. Chromite Sand This sand is particularly useful in the casting of high-performance steel components. Chromite sand has excellent thermal properties and is resistant to basic slags, making it ideal for high-temperature applications. Its stability under extreme conditions ensures fewer defects.
Properties of Sand for Casting
sand used for sand casting
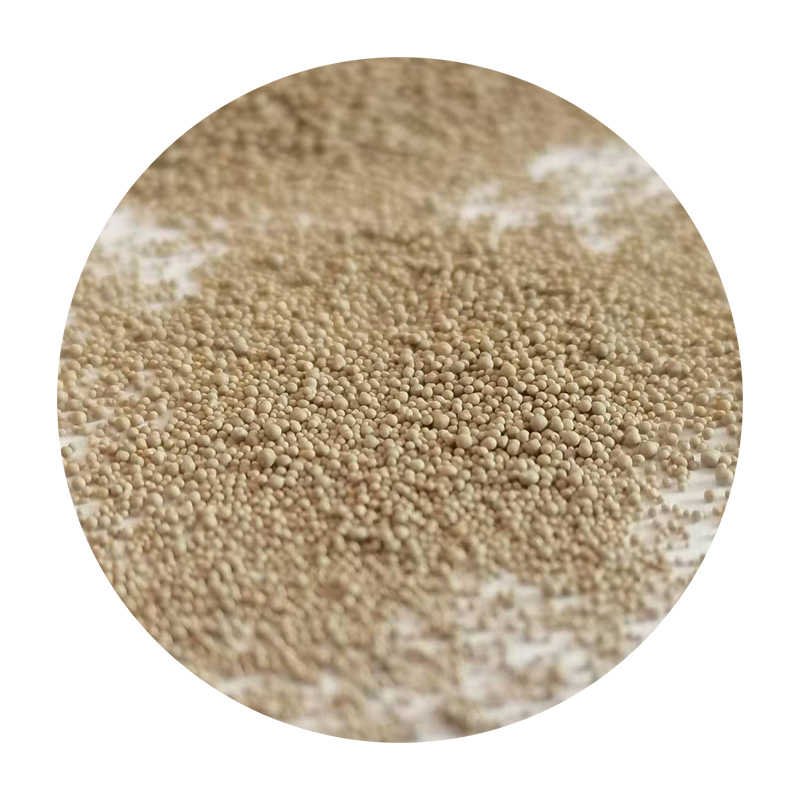
The efficiency of sand casting heavily depends on various properties of the molding sand, including its grain size, cohesiveness, permeability, and moisture content. These properties influence the ability of the sand to hold its shape under the molten metal's weight and heat.
1. Grain Size The size of the sand grains affects the surface finish of the cast products. Finer sands produce smoother surfaces but may not be as strong as coarser sands. Therefore, a balance must be struck depending on the desired surface quality and strength requirements.
2. Cohesiveness This property allows sand particles to stick together, forming a rigid mold. Different binders can be used to enhance cohesiveness. Oil and resin binders are commonly mixed with sand to improve its stability and durability.
3. Permeability Permeability is the ability of the mold to allow gases to escape during the casting process. High permeability is crucial to prevent defects caused by trapped gases, leading to poor surface finishes and structural integrity.
4. Moisture Content The correct moisture content in sand is vital for effective bonding. Too much moisture can make the mold weak and increase the risk of defects, while too little can result in poor surface finishes.
The Role of Additives
In the quest for optimal casting performance, various additives are often mixed with sand to enhance its properties. Clay is one common additive that improves the sand's cohesiveness, while chemical binders might be used to improve the mechanical strength of molds. The specific combination of sand and additives depends heavily on the requirements of the casting process, particularly the type of metal being poured and the complexity of the mold.
Conclusion
The selection of appropriate sand and its properties significantly affect the efficiency of the sand casting process and the quality of the final products. As industries continue to evolve and push the boundaries of manufacturing, advancements in casting technologies and the development of specialized sands will likely remain at the forefront of research and innovation. Understanding the nuances of sand utilized in sand casting is essential for engineers and manufacturers aiming to achieve excellence in production and meet the varying demands of contemporary markets.
Post time:9 月 . 28, 2024 08:28
Next:Benefits of Sand Casting Processes in Manufacturing and Production Techniques