Sand Used for Sand Casting An Essential Material in Metalworking
Sand casting is one of the oldest and most widely utilized metal casting processes, valued for its versatility, cost-effectiveness, and accessibility. At the heart of this ancient technique lies a simple yet vital ingredient sand. This article will explore the types of sand used in sand casting, their properties, and the overall significance of sand in the casting process.
Types of Sand Used in Sand Casting
The most commonly used type of sand in sand casting is silica sand, which is primarily composed of silicon dioxide (SiO₂). Silica sand is renowned for its grain shape, size, and excellent thermal properties, making it ideal for forming molds and cores. The grains are usually round or sub-angular, which enhances the flowability and compaction of the sand mixture.
Another type of sand often used is olivine sand, which is composed of the mineral olivine (Mg₂SiO₄). This type of sand has a melting point much higher than that of silica sand, making it suitable for casting non-ferrous metals and for applications requiring higher temperature resistance.
In addition to these, chemically bonded sands like furan sand and phenolic sand are sometimes employed. These sands are mixed with chemical binders that harden when heated, providing superior strength and producing finer surfaces than traditional silica sand.
Properties of Casting Sand
Several key properties of casting sand impact the quality and success of the sand casting process
1. Refractoriness The ability of the sand to withstand high temperatures without deforming or losing its structural integrity is crucial. This ensures that the mold maintains its shape during metal pouring.
sand used for sand casting
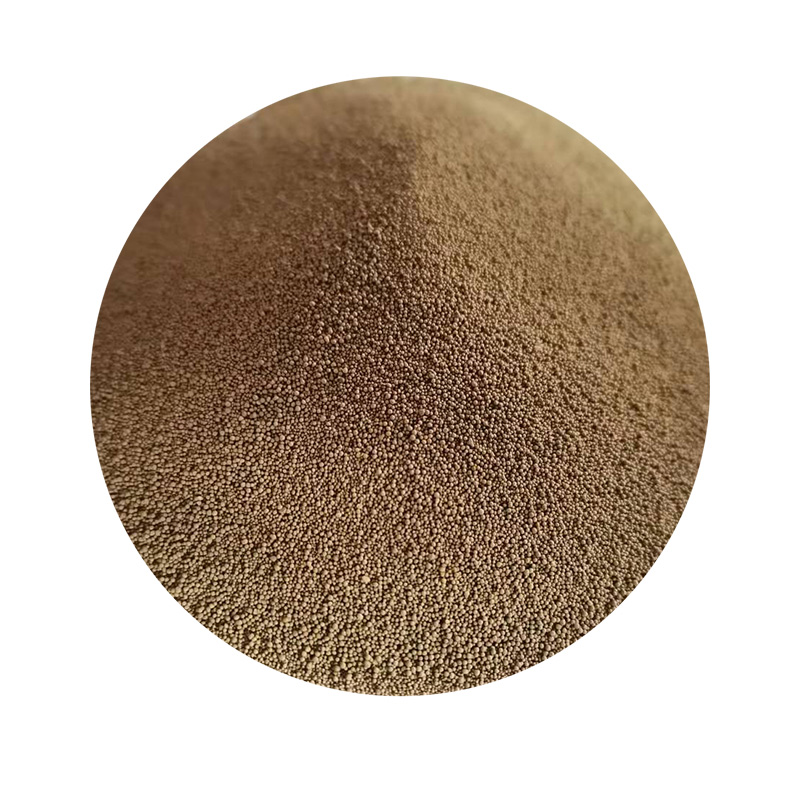
2. Permeability A good casting sand must allow gases, which are produced during the molten metal pouring, to escape without damaging the mold. If the sand is too porous, it may lead to casting defects like blowholes.
3. Cohesiveness This property refers to the ability of sand particles to stick together. Properly cohesive sand ensures that the mold holds its form during the pouring and cooling process.
4. Grain Size The size of sand grains affects the surface finish of the final casting. Finer sands produce smoother surfaces but may be less permeable, while coarser grains promote better airflow but yield rougher finishes.
5. Moisture Content The water content of the sand mixture plays a critical role in binding the grains together and influencing the mold's strength. Too much moisture can weaken the mold, while too little can lead to cracks and other defects.
The Role of Sand in the Casting Process
The process of sand casting begins with creating a mold by compacting sand around a pattern that represents the shape of the desired metal object. The sand is often mixed with clay and water to enhance its properties and facilitate molding. Once the pattern is removed, the resulting cavity is poured with molten metal.
After cooling, the sand mold is broken away to reveal the cast object. In many cases, the sand can be reused by cleaning and reconditioning it, making sand casting an environmentally friendly option.
Conclusion
In conclusion, sand is an indispensable material in the sand casting process. Its variety, properties, and ability to be reused make it a favorite choice among metalworkers across various industries. As technology continues to evolve, the methods and materials associated with sand casting may change, but the significance of sand in creating complex and precise metal parts will undoubtedly persist. The continuing research into enhanced sand materials promises improvements in casting performance, efficiency, and sustainability, ensuring that sand casting remains a vital component of modern manufacturing.
Post time:11 月 . 08, 2024 12:55
Next:Innovative Techniques in Cast Iron Sand Casting for Enhanced Manufacturing Efficiency